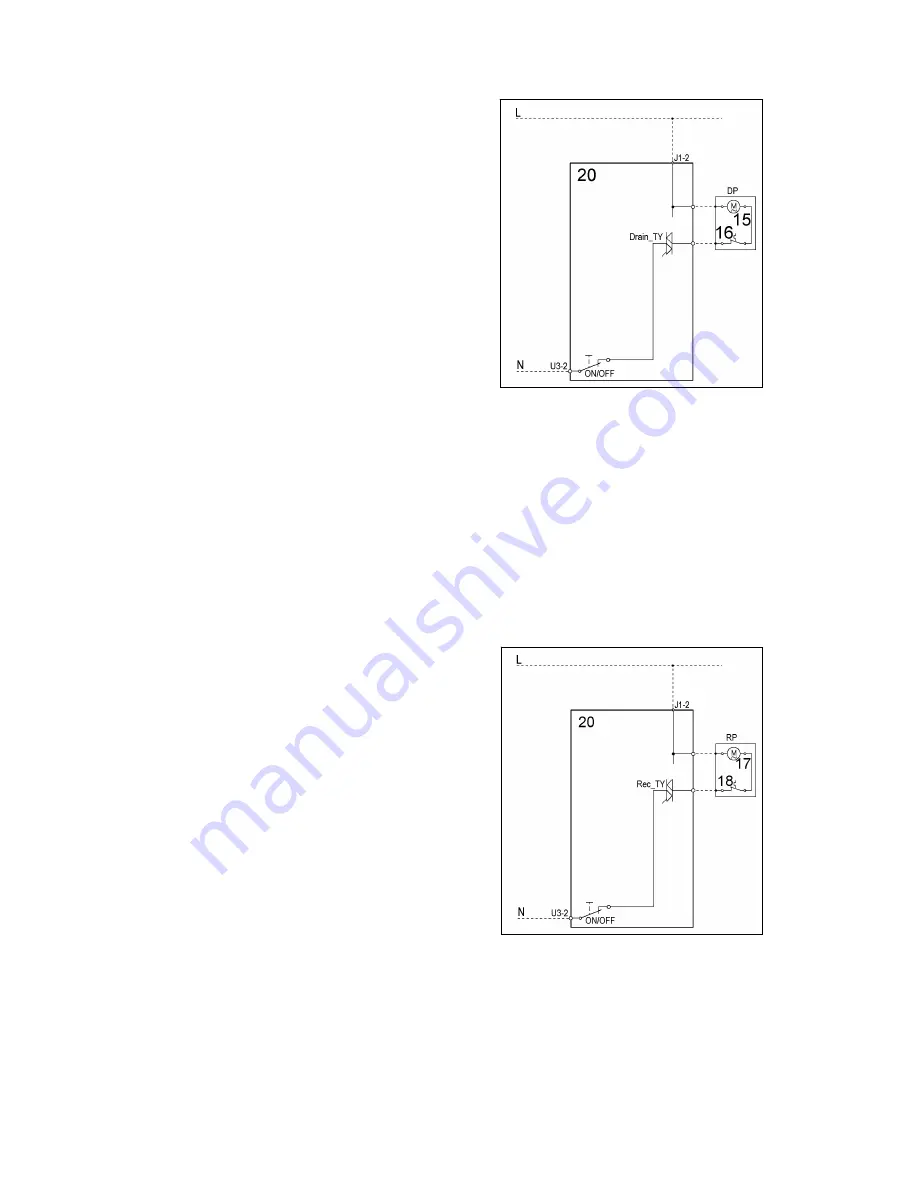
SOI/DT 2010-03 dmm
52/78
599 72 84-41
11.5 Drain
pump
15 Drain
pump
16 Overload
cut-out
20 PCB
The PCB powers the drain pump via a triac as follows:
-
until the electronic pressure switch closes on empty, after which the pump is actuated for a brief
period or passes to the subsequent phase
-
for a pre-determined period (and possibly an alarm is displayed)
11.6
Circulation pump (where featured)
On jetsystem models, the main PCB powers the circulation pump directly through a triac
17 Drain
pump
18 Overload
cut-out
20 PCB