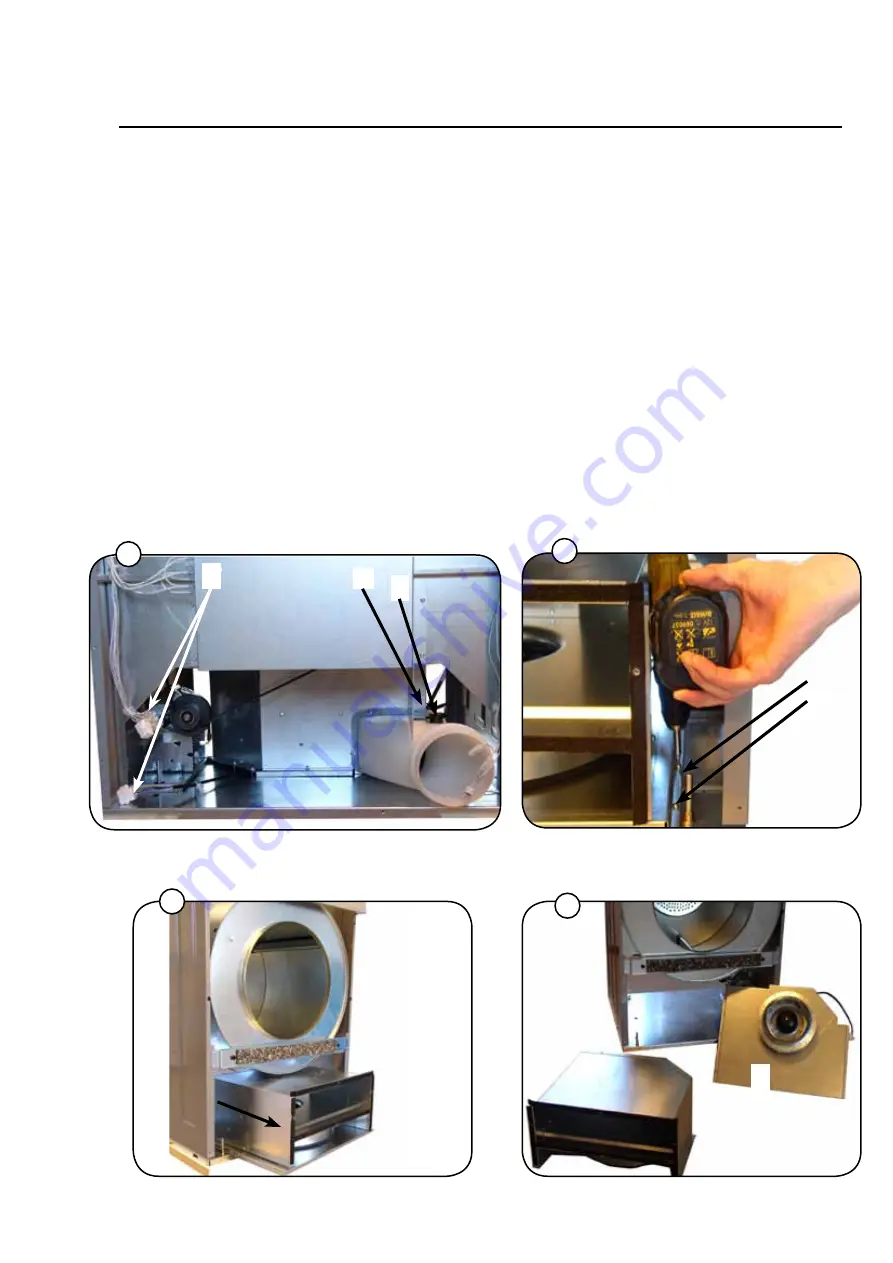
43
Motor and transmission
D
E
A
1
B
C
2
4
3
Replacement fan module:
1
. Dismount the power to the dryer.
2. Disconnect motor plug
A
and the overheating thermostats
B,
disconnect the NTC
sensor
C,
fig. 1.
3. Unscrew these two screws on the right side and three screws on the left side of
the fan house, fig. 2.
4. Remove the fan house, fig. 3.
5. Unscrew the fan house
D
and turn
fan motor on bottom plate
E
upside-down, fig. 4.