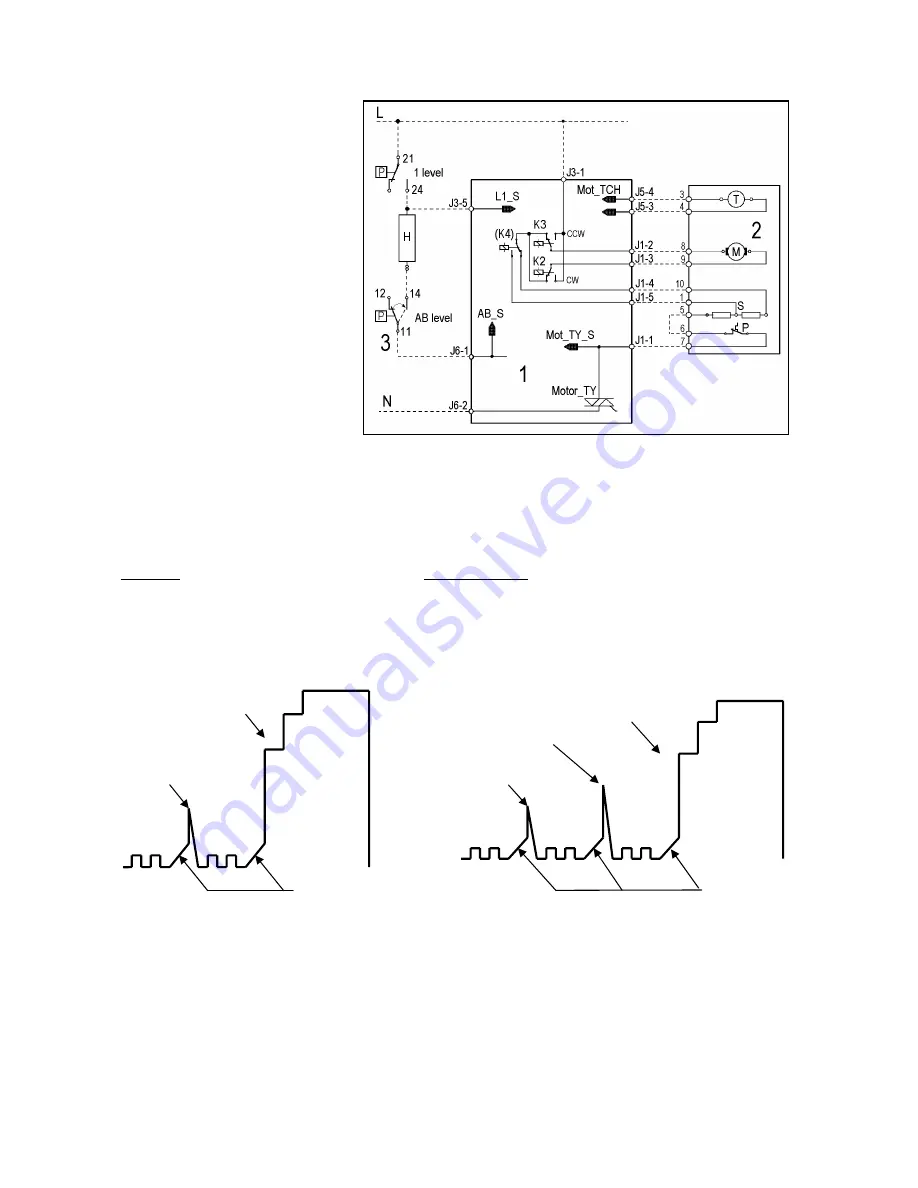
SOI/DT 2005-07 dmm
43/59
599 37 22-15
7.11 Motor
1. PCB
2. Motor
3. Anti-boiling/anti-foam
pressure switch
M = rotor
P = motor safety cut-out
S = stator
T = tachimetric generator
AB_S Anti-boiling/anti-
foam level sensor
7.12 Power supply to motor
The main PCB powers the motor via a triac. The direction of rotation is reversed by switching of the
contacts on the two relays (K2-K3), which modify the connection between the rotor and the stator.
In certain models (1200-1600rpm), a third relay (K4) is used to power the stator (full or half field) according
to the spin speed
The speed of rotation of the motor is determined by the signal received from the tachimetric generator.
During the spin phases, the microprocessor, depending on the software configuration, may perform the
anti-foam control procedure (if featured) and the anti-unbalancing control procedure
7.13 Anti-foam control system
The anti-foam control procedure (if featured) is performed via the anti-boiling pressure switch (AB).
Spin phase without foam
Spin phase with little foam
•
Spin with little foam:
if the contact of pressure switch AB closes on FULL, the spin phase is
interrupted; the drain pump continues to operate and, when the contact returns to EMPTY, the spin
phase is resumed.
•
Spin with excessive foam in the tub (critical situation):
The control system detects whether the
pressure switch commutates 5 times to FULL. In this case, the spin phase is skipped, and a one-
minute drain cycle is performed with the motor switched off; in the case of a washing phase, a
supplementary rinse is added.
FUCS
300 rpm pulse
Spin
Anti-foam
(Level AB)
300 rpm
pulse
FUCS
Spin