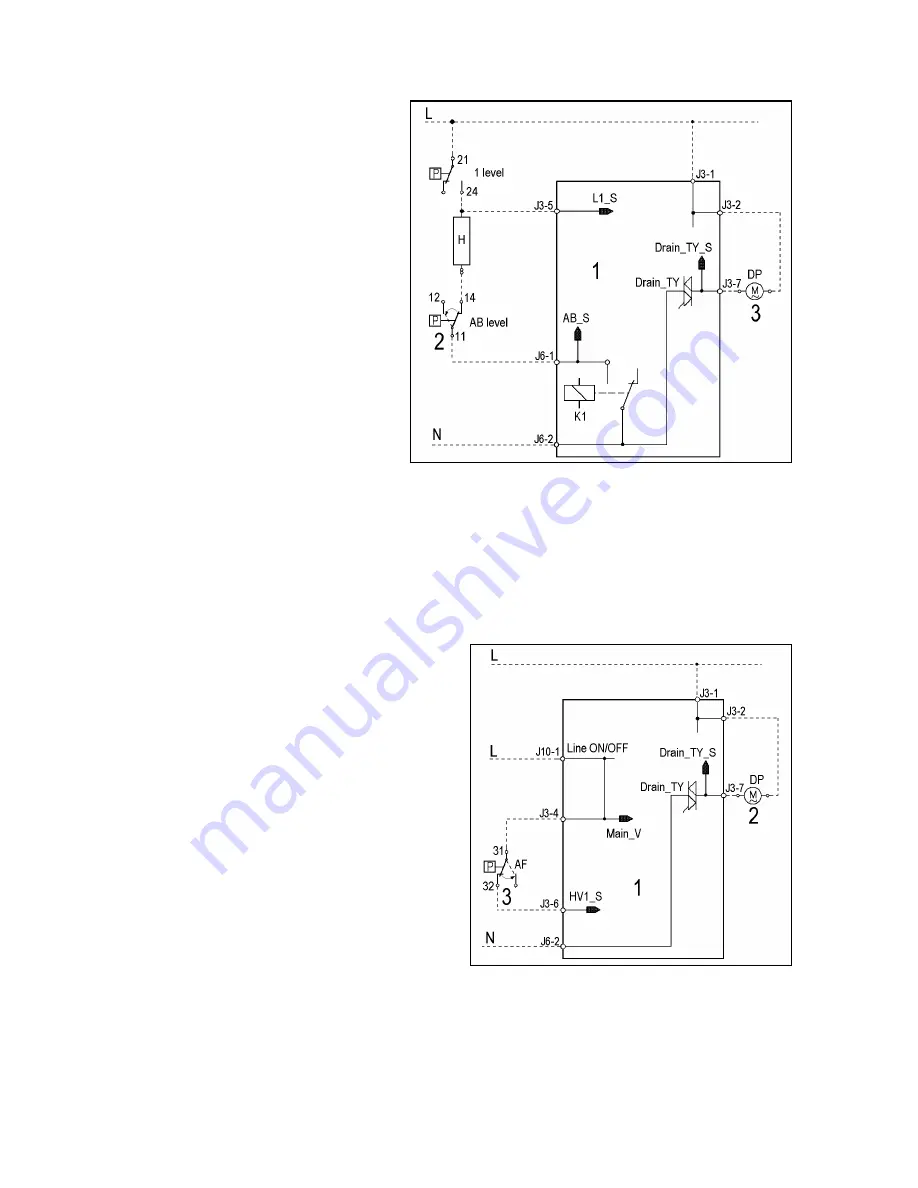
SOI/DT 2005-07 dmm
40/59
599 37 22-15
7.7 Drain
pump
1. PCB
2. Anti-boiling pressure switch
8. Drain
pump
AB_S Anti-boiling level sensor
The PCB powers the drain pump via a triac as follows:
ª
for a pre-determined period.
ª
until the anti-boiling pressure switch closes on EMPTY, after which the pump is actioned for a brief
period or passes to the subsequent phase
7.8 Anti-flooding device
1. PCB
2. Drain pump
3. Anti-overflow pressure switch
HV1_S Anti-overflow level sensor
The third pressure switch level (if featured) is used as an anti-overflow
safety device: if the pressure switch
contact should open in the FULL position, the PCB actions the drain pump until the pressure switch returns
to the EMPTY position.