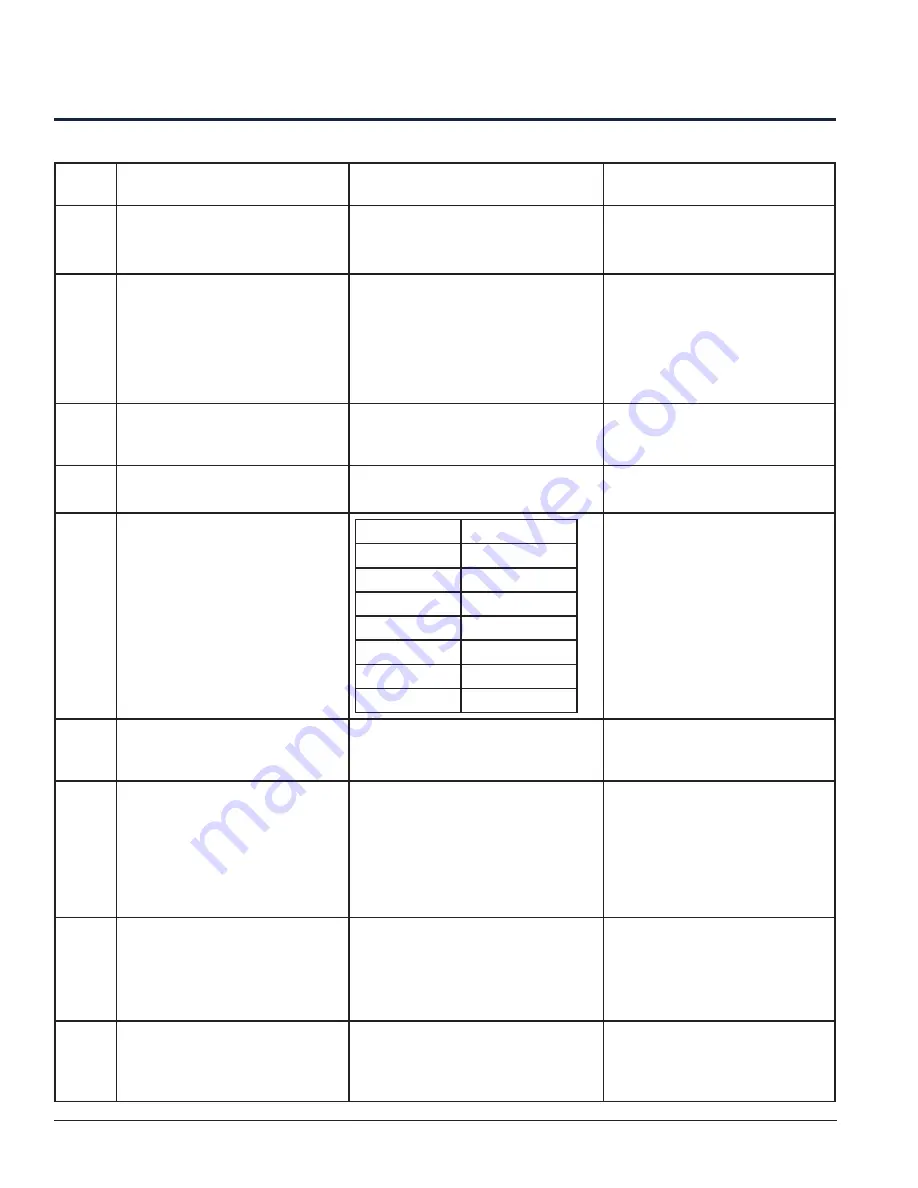
18
8. Electrical Components –
EFLS617SIW / EFLS517SIW /
EFLS417SIW
Electrical Component Resistance and Specification Table
S. No. Component
Resistance
Specification
1
Door Lock
--
Supply voltage 120 V (95-132 V
60Hz) / 230 V (180-265 V 50-60
Hz), Coil insulation: F
2
Dispenser Solenoid valve
Coils resistance @25ºC 990±10% Ω
Cold water temperature-25 ºC
Hot water temperature-60 ºC
Coils room temperature-60 ºC
Nominal Voltage-120 V
Voltage tolerance-(-15% + 10%)
Nominal Frequency-60 Hz
3
Motor
--
200 V, 4 A, 330 Hz. (Max.),
RPM (Max.), - 18,600, Insulation
Class-F
4
Heating Element
(Not applicable for 417 series) 13 Ω to 15 Ω
120 V, 60 Hz, 1000 W
5
NTC
(Not applicable for 417 series)
Temp
Ω
0 ºC
15771 ± 6.1%
30 ºC
3891 ± 4%
40 ºC
2573 ± 3.4%
50 ºC
1742 ± 2.8%
60 ºC
1204 ± 2.2%
70 ºC
849 ± 2.4%
95 ºC
383 ± 3.6%
--
6
Pressure Sensor
--
5 ± 0.25 V DC, 5 mA (Max.)
85 ºC operating temp (Max.)
44 Hz empty drum
7
LED Drum Light
(Not applicable for 417 series)
--
Everlight LED
ELSW-F91C1-OLPGS-C6500
350 mA (Max. LED Current)
Power 1 W
Min. Flux:35 Lumen (55 Typical)
White LED (Cold White) Typical
6500 K
8
Recirculation pump
(Not applicable for 417 series)
and Concentrated Wash Pump
(Not applicable for 417 and 517
series)
31.5 ± 10% Ω @20 ºC
Nominal Voltage-120 V, 60
Hz, Insulation Class F (155),
Working Voltage 95-132 V
9
Drain Pump
Winding Resistance-14 ± 10% Ω
Rated-120 VAC / 60 Hz,
Working Voltage-95-132 V AC,
Current and Power with Rotor
locked-1.4 A, 80 W Max.
Summary of Contents for EFLS417SIW
Page 2: ...2 ...
Page 8: ...8 4 Product Features 4 1 EFLS617SIW EFLS517SIW EFLS417SIW ...
Page 16: ...16 7 2 3 Main Control Board Electrical Characteristics ...
Page 17: ...17 7 3 Wiring Diagram EFLS617SIW EFLS517SIW EFLS417SIW Electrical Characteristics ...