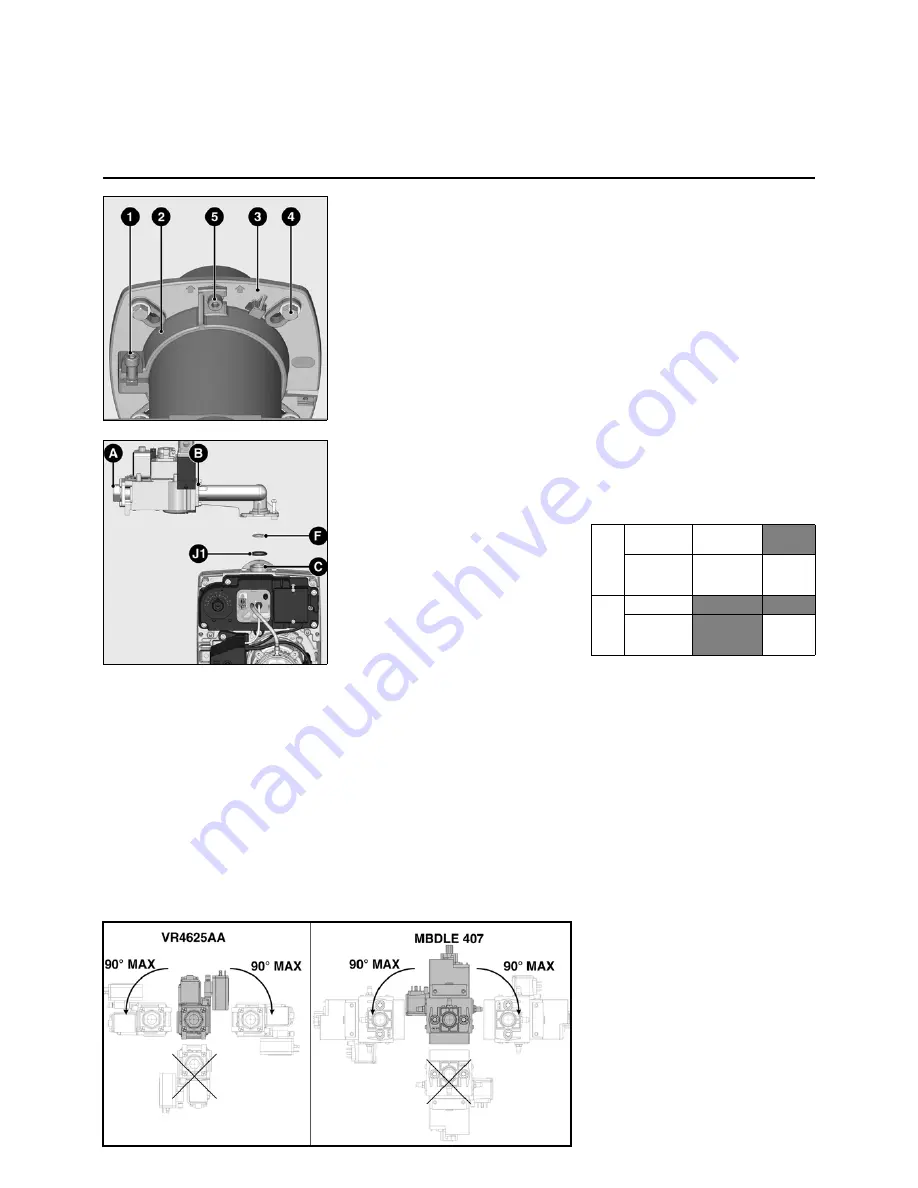
01/2009 - Art. Nr. 4200 1016 3900A
24
Assembly
Burner assembly
Burner installation position
Gas connection, installation location
Burner assembly
The burner flange
3
is equipped with
elongated holes and can be used with a
hole circle diameter of 150 - 170 mm.
These dimensions comply with EN 226.
The burner flange gasket and the
fastening screws are included with the
burner.
Sliding the pipe bracket
2
on the burner
pipe makes it possible to adjust the
installed depth of the combustion head to
the geometry of the combustion chamber
concerned. The installed depth remains
the same during fitting and removal.
Pipe bracket
2
secures the burner to the
connecting flange and therefore to the
boiler. This completely seals off the
combustion chamber.
Installation:
• Secure connecting flange
3
to the
boiler using screws
4
• Fit pipe bracket
2
to the burner pipe
and secure using screw
1
. Tighten
screw
1
to a maximum torque of 6 Nm.
• Turn the burner slightly, guide it into
the flange and secure using screw
5
.
Removal:
• Loosen screw
5
.
• Turn the burner out and pull it out of
the flange.
Gas connection
The gas line diameter should be chosen
in such a way that the pressure losses
do not exceed 5 % of the distribution
pressure.
Gas train assembly
• Remove plugs on
A
,
B
and
C
.
• Check that ring seal
J1
is present and
correctly fitted to flange
C
.
• Secure gas train on the right and left
(see below for other installation
locations).
VG1.40 shutter assembly
(see table opposite)
• Install the gas ball valve upstream of
the gas train.
Note
Allow sufficient space for access to the
different adjusting points. Bleed the gas
supply line thoroughly. Check all
connections for leaks.
Permissible installation locations for
gas valves
VG
1.40
Natural gas
Shutter
F
(metal)
Liquefied
Petroleum
Gas
Shutter
F
(black)
Shutter
GP
VG
1.55
/85
Natural gas
Liquefied
Petroleum
Gas
Shutter
GP