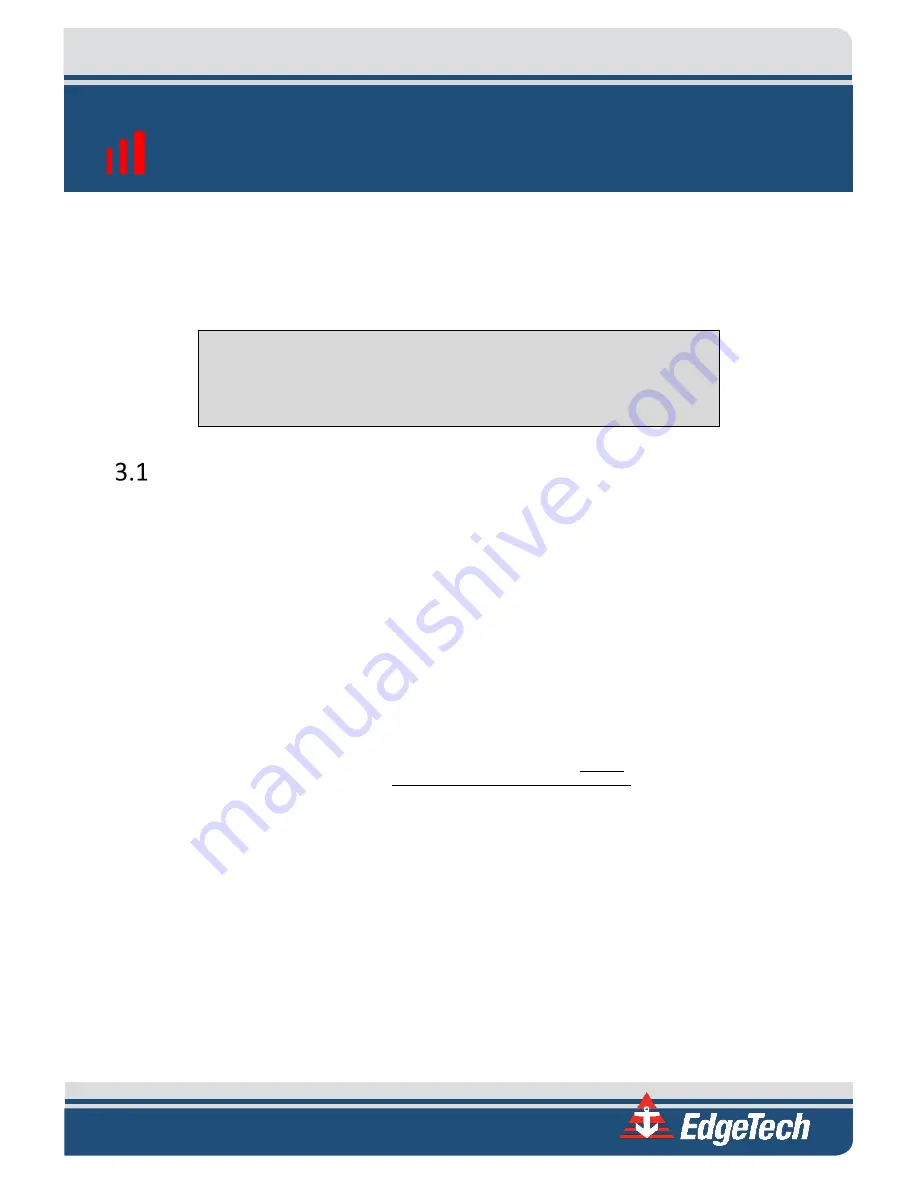
3-1
3.0
INSTALLATION
This section includes instructions for implementing a 4213C Hydrophone mounting assembly, making
proper attachment of the 4113C Deck Cable, and the Transceiver side panel interface connections.
Hydrophone bearing, X, Y, Z offsets and pitch/roll offsets are generally determined at the time of
installation. This section includes sample procedures for determining
NOTE:
EdgeTech cannot give an absolute installation procedure because
each vessel is different, therefore EdgeTech can only provide guidelines.
The hydrophone installation is critical to the operation of the BATS.
Hydrophone / Interrogator Installation
The most crucial element in the BATS’ performance is the manner and location in which the hydrophone
assembly is mounted on the vessel. When choosing a mounting location, the operator should be aware
that by nature, the BATS is an extremely sensitive Acoustic System. Hydrophone assembly must be
positioned to receive acoustic pulses coming from pinger, transponder, or responder during operation.
The hydrophone should be mounted as far as possible from noise sources, such as propellers, thrusters,
echo-sounder transducers, main engines, generators, and other underwater acoustic generating systems.
Ideally, the hydrophone should be mounted far enough from nearby reflectors to allow the direct arrival
of a signal from the acoustic source before a potential reflected signal arrives.
One meter
is the minimum
recommended distance between the hydrophone array and the nearest reflector (which is usually to the
vessel's hull or keel), shown in
. To ensure 360-degree coverage, it is important to keep the
hydrophone below the level of the vessel's keel.
1
𝑚𝑚𝑚𝑚𝑚𝑚𝑚𝑚𝑚𝑚
=
�1
.
33
𝑚𝑚𝑚𝑚𝑚𝑚𝑚𝑚𝑚𝑚𝑚𝑚𝑚𝑚𝑚𝑚𝑚𝑚𝑚𝑚𝑚𝑚𝑚𝑚
𝑥𝑥
1500
𝑚𝑚𝑚𝑚𝑚𝑚𝑚𝑚𝑚𝑚𝑚𝑚
𝑚𝑚𝑚𝑚𝑠𝑠𝑠𝑠𝑠𝑠𝑠𝑠
�
2
𝑤𝑤𝑤𝑤𝑤𝑤
𝑡𝑡𝑡𝑡𝑤𝑤𝑡𝑡𝑚𝑚𝑚𝑚
𝑡𝑡𝑚𝑚𝑚𝑚𝑚𝑚
Equation 1
System performance can be degraded by multi-path or underwater signal reflections and reverberation.
To minimize the possible effects of multi-path, choose a hydrophone location that is as far away as
possible from any surface that would make a good reflector of an acoustic pulse. Any hard plate or
structure near the hydrophone has the potential to reflect pulses into the hydrophone. The air-water
interface is also an extremely efficient acoustic reflector. Avoid any mounting locations that would place
the hydrophone in the proximity of bubbles. Contact
for additional
information on a specific installation.
Summary of Contents for USBL BROADBAND ACOUSTIC TRACKING SYSTEM
Page 20: ......
Page 26: ......
Page 28: ...SECTION 2 SPECIFICATIONS 2 2 BATS 0018257_REV_A Figure 2 1 BATS USBL Portable System ...
Page 29: ...2 3 Figure 2 2 Portable BATS Transceiver Figure 2 3 Portable BATS Transceiver Side Panel ...
Page 44: ...SECTION 2 SPECIFICATIONS 2 18 Figure 2 11 BATS Portable System Mechanical Outline 0020020 ...
Page 45: ...2 19 Figure 2 12 BATS Desktop System Mechanical Outline 0020022 ...
Page 46: ...SECTION 2 SPECIFICATIONS 2 20 Figure 2 13 BATS Rackmount System Mechanical Outline 0020017 ...
Page 52: ...3 6 Figure 3 3 Hydrophone Outline Drawing 0019592 ...
Page 53: ...3 7 Figure 3 4 Hydrophone MTG Arrangement Page 1 of 2 0020018 ...
Page 54: ...3 8 Figure 3 5 Pipe Angle Bracket Arrangement Page 2 of 2 0020018 ...
Page 55: ...3 9 Figure 3 6 Angle Bracket Drawing 007327 ...
Page 56: ...3 10 Figure 3 7 15m 50ft Deck Cable for Desktop 002936 ...
Page 57: ...3 11 Figure 3 8 30m 100ft Deck Cable for Desktop 0002935 ...
Page 58: ...3 12 Figure 3 9 Deck Cable for Portable 0003458 ...
Page 60: ...3 14 Figure 3 10 Suggested Mounting Arrangement in Machined Shaft Flange OTS 0010007 ...
Page 61: ...3 15 Figure 3 11 Suggested Hydrophone Shaft Machining Through Hull 0020019 ...
Page 62: ...3 16 BATS 0018257_REV_A Figure 3 12 Gate Valve Type Installation ...
Page 65: ...3 19 Figure 3 14 Hydrophone Mounting Diagram ...
Page 78: ...3 32 BATS 0018257_REV_A Figure 3 23 Sync Interface Connector Data Diagram on Desktop Unit ...
Page 79: ...3 33 Figure 3 24 Sync Interface Connector Desktop Console 0002566 ...
Page 80: ...3 34 Figure 3 25 Analog Interface Connector Data Diagram Desktop Console ...
Page 81: ...3 35 Figure 3 26 Analog Interface Connector Desktop Console 0002984 ...
Page 82: ...3 36 Figure 3 27 Ethernet Cable 1PPS 0002474 ...
Page 83: ...3 37 Figure 3 28 BATS Portable AC Cord 0002868 ...
Page 84: ...3 38 Figure 3 29 BATS Portable COMMS Cable 0014672 ...
Page 85: ...3 39 Figure 3 30 Portable BATS Synchronization Connector ...
Page 86: ...3 40 Figure 3 31 BATS Portable Sync Cable 0002567 ...
Page 87: ...3 41 Figure 3 32 Portable BATS Analog Input Connector Data Diagram ...
Page 88: ...3 42 Figure 3 33 BATS Portable Analog Connector Assembly Drawing 0002441 ...
Page 90: ......
Page 95: ...5 5 Figure 5 3 BATS Block Diagram 1 ...
Page 96: ...5 6 Figure 5 4 BATS Block Diagram 2 ...
Page 97: ...5 7 Figure 5 5 Portable BATS Block Diagram 1 ...
Page 98: ...5 8 Figure 5 6 Portable BATS Block Diagram 2 ...