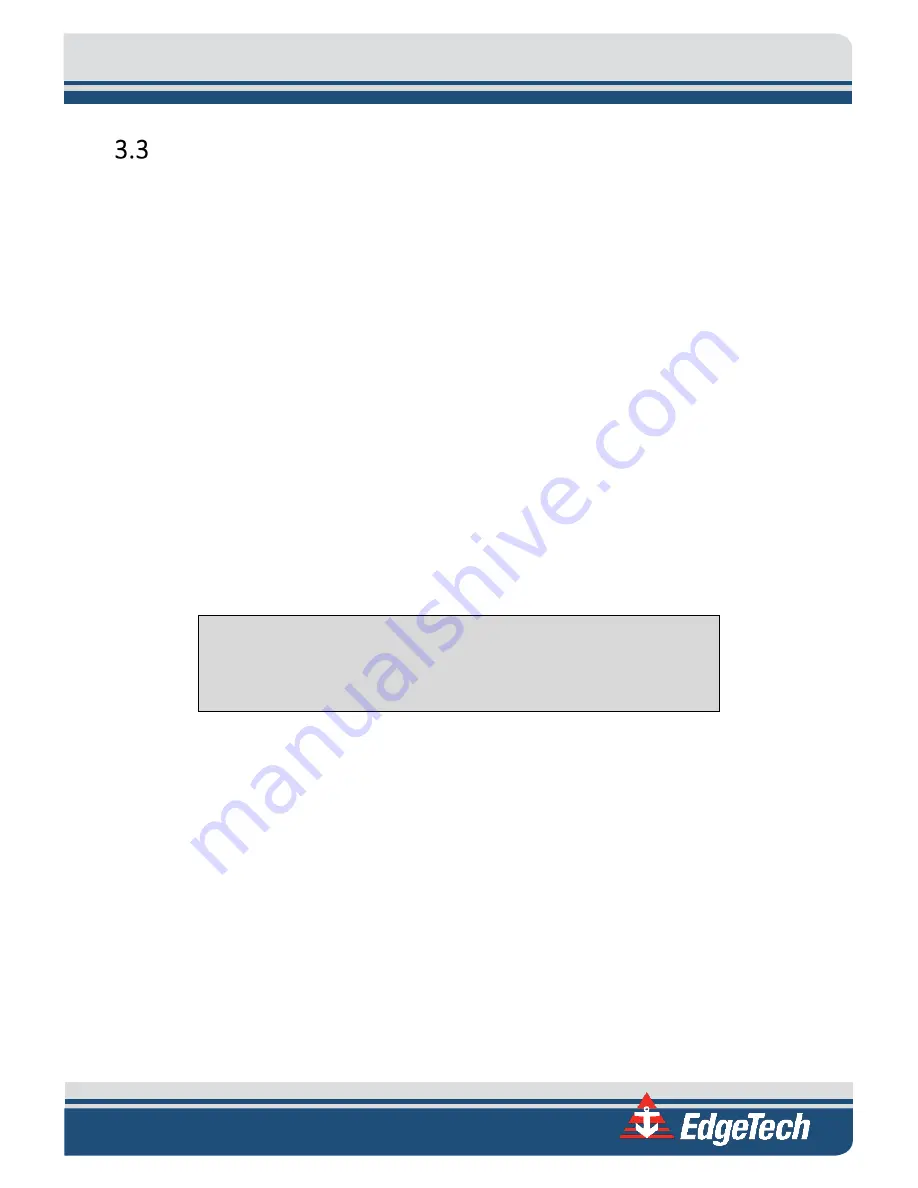
3-17
Hydrophone Offsets
The BATS computes range and bearing relative to the hydrophone, unless the system is instructed to add
or subtract corrections (offsets) which relate range and bearing to some other reference point on the
vessel. The hydrophone centerline, or zero bearing, is indicated by the index mark, shown in
and
, and is generally aligned so that it corresponds to the vessel heading.
It is difficult and time consuming to fabricate a mounting in which the hydrophone heading is aligned
within a degree of the vessel centerline, unless the vessel is in a drydock. If you have the facilities to
perform an exact mechanical alignment or if the installation is to be permanent, consider fabricating a
mount that repeatedly returns the hydrophone to the same physical location aligned to within 0.5° of the
vessel centerline.
Most operations requiring a Portable BATS will be on various vessels of opportunity, and require quick
and temporary mounting. The Desktop/Rackmount systems offer a more permanent solution. In this case
align the hydrophone with the vessel centerline as closely as possible. Use some variation of the following
procedure to determine hydrophone offsets.
3.3.1
Hydrophone Bearing Offset
The bearing offset must be determined before X, Y, and Z offsets can be measured.
1.
Measure distance (d) from vessel centerline to the hydrophone location as shown in
NOTE:
Most vessels have a centerline weld or plank running down the
deck that can be used for alignment purposes. If in a seamless deck
vessel, measure the vessel beam and determine the true centerline.
2.
Weight a line to suspend the acoustic tracking source vertically in the water.
3.
As far forward on the vessel as possible, hang the weighted acoustic beacon over the side at the
same distance from the vessel centerline as the hydrophone, position B1 in
. It may be
necessary to use a length of pipe or a boathook to extend the weighted line the required distance.
The beacon should be slightly deeper than the hydrophone.
4.
Turn the System on and set it up to track the beacon in use. If you have aligned the mounting
bracket correctly, the system tracks the beacon at or very near a 0.0° bearing.
5.
If you have designed a mounting that can rotate while in the vertical position, you can rotate the
hydrophone until you obtain the correct reading. If you cannot rotate the pipe it will be necessary
to enter a bearing correction at the time of operation. Bearing Offset can be entered under the
USBL HYDROPHONE PARAMETER menu.
Summary of Contents for USBL BROADBAND ACOUSTIC TRACKING SYSTEM
Page 20: ......
Page 26: ......
Page 28: ...SECTION 2 SPECIFICATIONS 2 2 BATS 0018257_REV_A Figure 2 1 BATS USBL Portable System ...
Page 29: ...2 3 Figure 2 2 Portable BATS Transceiver Figure 2 3 Portable BATS Transceiver Side Panel ...
Page 44: ...SECTION 2 SPECIFICATIONS 2 18 Figure 2 11 BATS Portable System Mechanical Outline 0020020 ...
Page 45: ...2 19 Figure 2 12 BATS Desktop System Mechanical Outline 0020022 ...
Page 46: ...SECTION 2 SPECIFICATIONS 2 20 Figure 2 13 BATS Rackmount System Mechanical Outline 0020017 ...
Page 52: ...3 6 Figure 3 3 Hydrophone Outline Drawing 0019592 ...
Page 53: ...3 7 Figure 3 4 Hydrophone MTG Arrangement Page 1 of 2 0020018 ...
Page 54: ...3 8 Figure 3 5 Pipe Angle Bracket Arrangement Page 2 of 2 0020018 ...
Page 55: ...3 9 Figure 3 6 Angle Bracket Drawing 007327 ...
Page 56: ...3 10 Figure 3 7 15m 50ft Deck Cable for Desktop 002936 ...
Page 57: ...3 11 Figure 3 8 30m 100ft Deck Cable for Desktop 0002935 ...
Page 58: ...3 12 Figure 3 9 Deck Cable for Portable 0003458 ...
Page 60: ...3 14 Figure 3 10 Suggested Mounting Arrangement in Machined Shaft Flange OTS 0010007 ...
Page 61: ...3 15 Figure 3 11 Suggested Hydrophone Shaft Machining Through Hull 0020019 ...
Page 62: ...3 16 BATS 0018257_REV_A Figure 3 12 Gate Valve Type Installation ...
Page 65: ...3 19 Figure 3 14 Hydrophone Mounting Diagram ...
Page 78: ...3 32 BATS 0018257_REV_A Figure 3 23 Sync Interface Connector Data Diagram on Desktop Unit ...
Page 79: ...3 33 Figure 3 24 Sync Interface Connector Desktop Console 0002566 ...
Page 80: ...3 34 Figure 3 25 Analog Interface Connector Data Diagram Desktop Console ...
Page 81: ...3 35 Figure 3 26 Analog Interface Connector Desktop Console 0002984 ...
Page 82: ...3 36 Figure 3 27 Ethernet Cable 1PPS 0002474 ...
Page 83: ...3 37 Figure 3 28 BATS Portable AC Cord 0002868 ...
Page 84: ...3 38 Figure 3 29 BATS Portable COMMS Cable 0014672 ...
Page 85: ...3 39 Figure 3 30 Portable BATS Synchronization Connector ...
Page 86: ...3 40 Figure 3 31 BATS Portable Sync Cable 0002567 ...
Page 87: ...3 41 Figure 3 32 Portable BATS Analog Input Connector Data Diagram ...
Page 88: ...3 42 Figure 3 33 BATS Portable Analog Connector Assembly Drawing 0002441 ...
Page 90: ......
Page 95: ...5 5 Figure 5 3 BATS Block Diagram 1 ...
Page 96: ...5 6 Figure 5 4 BATS Block Diagram 2 ...
Page 97: ...5 7 Figure 5 5 Portable BATS Block Diagram 1 ...
Page 98: ...5 8 Figure 5 6 Portable BATS Block Diagram 2 ...