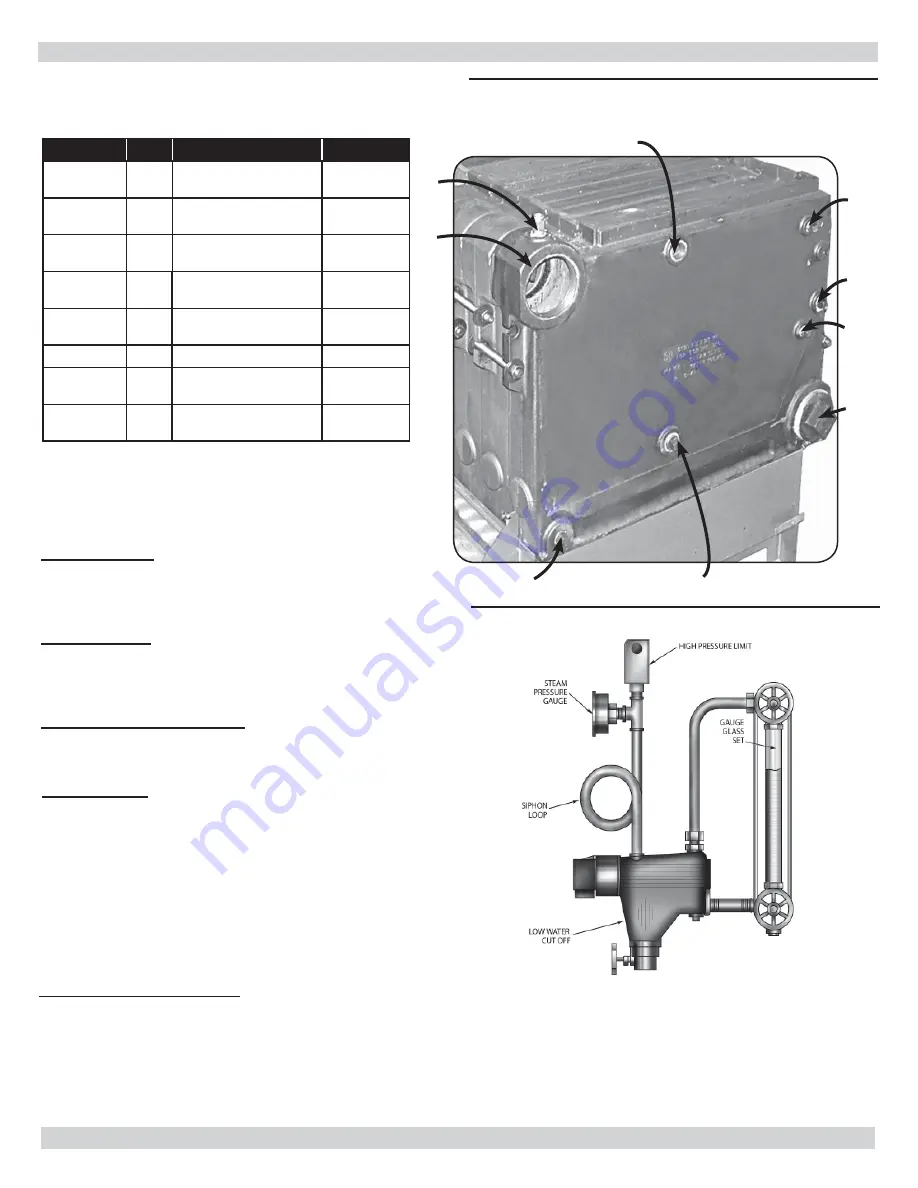
19
Illustration shows the end section and the various tap-
pings provided. Tappings are the same in both right
and left end sections.
OPENING
SIZE
STEAM
WATER
A
4”
Supply and Return
Supply and
Return
B
½”
Primary LWCO and
Gauge Glass Set
Plugged
C
¾”
Drain, Left End
Drain, Left
End
C
¾”
Drain, Right End
Drain, Right
End
D
½”
Plugged
Limit Con-
trol
E
1”
Accessories
Accessories
*F
1”
Safety Valve
Safety Relief
Valve
G
¾”
Plugged or Electronic
(Probe Type) LWCO
Plugged
*If opening F is to be used for something other than
the Safety Valve or Safety Relief Valve, or the Safety/
Relief valve is larger than 1”, the Safety/Relief Valve
must be installed in the Header Piping as near the
boiler as possible
A
B
A
B
C
D
E
F
G
BOILER TRIM
Following controls are supplied as standard equipment.
Details of their function and operation will be found in
section on Controls and Adjustments.
WATER TRIM
1. Water temperature high limit control
2. Combination temperature - pressure gauge
3. Safety relief valve (30 psi)
WATER TRIM ASSEMBLY
Locate water trim controls per chart and illustration
above.
STEAM TRIM
1.
Low Water Cut-Off (mounted externally) with blow-off
valve
2.
High Pressure Limit Control
3.
Pressure Gauge
4.
Water Gauge Glass Set
5.
Siphon Loop
6.
Safety Valve (15 psi..)
NOTE:
No shutoff of any description shall be placed between
the pressure relief valve and the boiler, or on discharge
pipes between such safety valves and the atmosphere.
Installation of the pressure relief valve shall conform
to the requirements of the ANSI/ASME Boiler and
Pressure Vessel Code, Section IV.
STEAM TRIM ASSEMBLY
Assemble Steam Trim, Low Water Cut-Off, High
Pressure Limit Control, Pressure Gauge, Water Gauge
Glass Set and Siphon Loop, as shown in Figures
30. See Illustration and Chart above for location of
controls.
Figure #30
WATER LEVEL
29” TO FLOOR
TAPPINGS
Figure 29
Figure 30