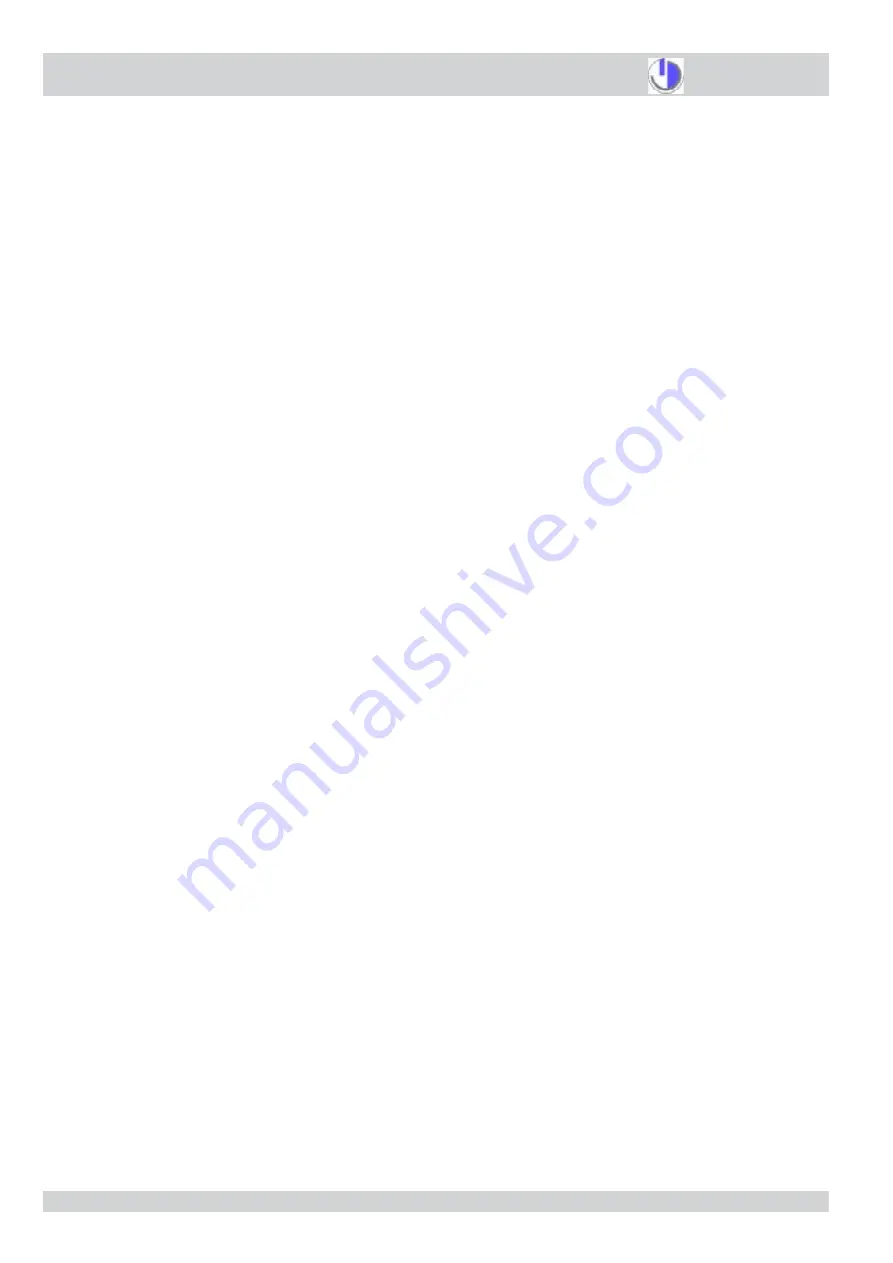
40
ECOTHERM
Heat transfer solutions
®
Operating Instructions High Capacity Water Heaters Models EHRE/EHPE & EDRE - ELC 11
in order to switch the system into
standby it has to be setted on
automatic. (see chapter 7)
9.1 NormAL load operating mode
requirement: norMal has to be
setted at the sevice menue (7.3.2.2)
STANDBY state:
Display: Mode norMal stanDBY
the outputs are set to:
Primary pump* = off
secondary pump = off
Burner demand = off
(Boiler prior circuit)
Control valve = CloseD
if the temperature at t1 and t2
falls below the setted shall value
with respective 2° C, the charging
process is started; which means
the system goes into the operating
condition "HeatinG".
hEATING state:
Display: HeatinG
the outputs are set to:
Primary pump* = on
secondary pump = off
Burner demand = on
(Boiler prior circuit)
Control valve = oPen
The hot water pump (only modell
type EH) runs and the control
valve opens. if the temperature at
t4 exceeds the setted shall value
(primary circuit flow temperature
of the boiler), the actual charging
starts and the operating condition
switches into "charging".
ChArGING state:
Display: "Charging"
the outputs are set to:
Primary pump* = on
secondary pump = on
Burner demand = on
(Boiler prior circuit)
Control valve = OPEN, ---,
CLOSED (3-points)
the industrial water pump runs
and the control valve regulates
the loading temperature at t3
at the following value: Hot water
shall tempe 2° C. if the
temperature at t1 and t2 reaches
the setted to-be value, the charging
ends and the system is shut into the
operating condition "Cooling".
Cooling state:
(Residual heat)
Display: Cooling
the outputs are set to:
Primary pump* = on
secondary pump = on
Burner demand = off
(Boiler prior circuit)
Control valve = oPen
It is only active if a follow-up time
is entered. the primary pump and
the secondary pump are running
and the valve is opened in order to
cool down the primary circuit and
the boiler. after expiration of the
setted follow-up time the system is
switched again into the operating
condition "STAND-BY". The burner
prior circuit (boiler prior circuit) has
to be absolutely connected!
9.2 Loading process at normal
operation with remote control
remote control inputs X17 + 24V
(instead of wire strap - connection
scheme chapter 5.3) are connected
with external release, for instance
with a time switch, a guidance
system or a safety thermostat.
STAND-BY state:
same as at normal operating
condition, however with the
following changes:
if the temperature at t1 and
t2 deceeds the setted shall
temperature at each 2° K and if
the remote control input is closed,
the charging process is started,
which means the system is switched
into the operating connection
"HeatinG". if the remote control
input is opened while heating or
charging process, the system turnes
immediately into the state "flushing"
or "STAND-BY".
9.3. PEAK load operating mode
requirement: "Great" is setted
at the parameter input. More
information see 7.3.2.2
STAND-BY state
:
same as at normal operating
condition, however with the
following changes:
t1 is not in operating mode. if
the temperature at t2 deceeds
the setted shall value at 2° C, the
charging process is started, which
means the system is switched into
the state "HeatinG".
CHarGinG state:
same as at normal operating
condition, however with the
following changes:
if the temperature at t1 and t2
reaches the setted shall value, the
charging process ends and the
system is switched into the state
"Cooling"
*) Hot water pump is only available
at the models eH, not et eD
steam.
Peak load operating condition
and return flow limitation
respectively peak load operating
condition and sliding operating
are not possible at the same time.
9. operating modes
tank Charging