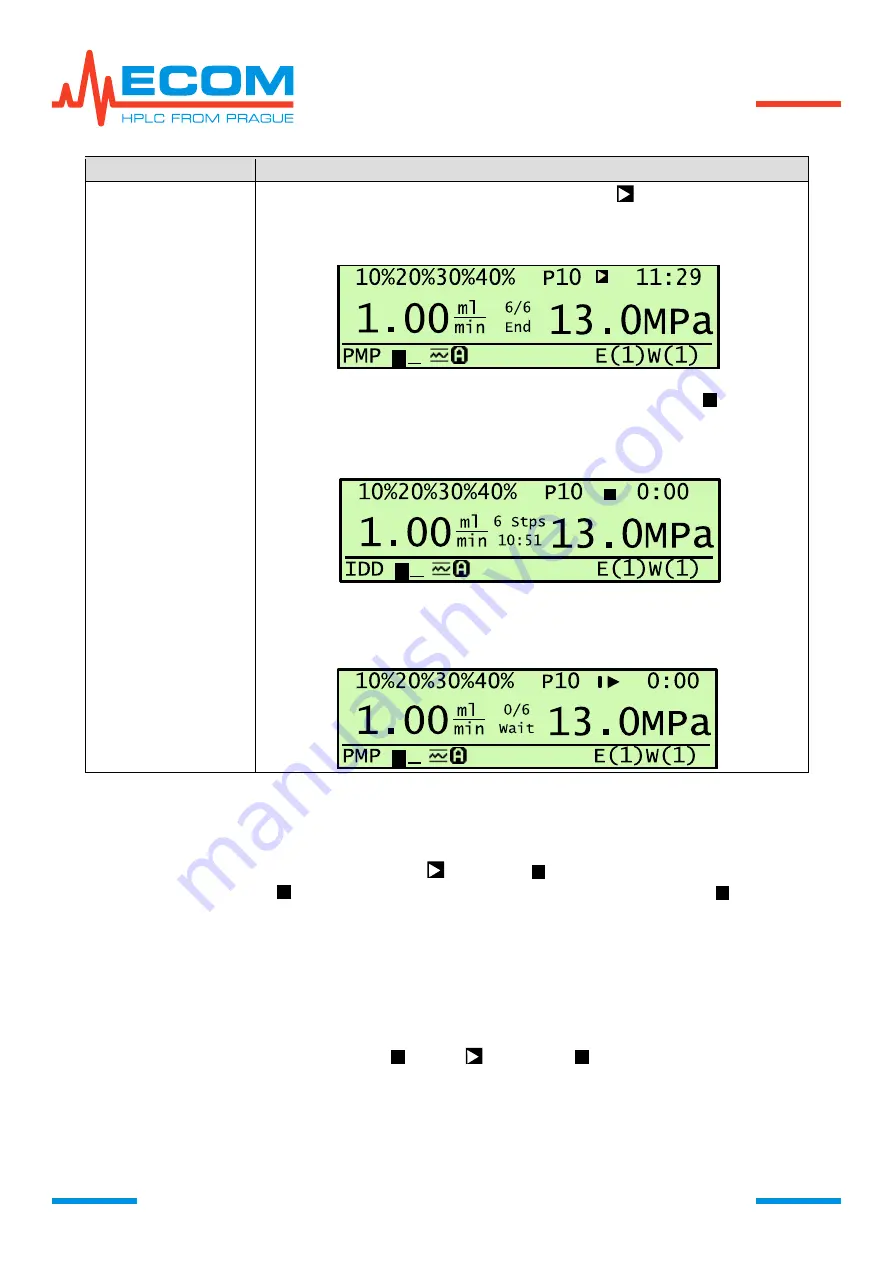
ECP2050
31 / 64
Action
Description
Program termination
RUN
– program tops, pump runs, ► changes to , total time is counting
up and step time changes to
End
. Pump keeps setting from last program
step.
STOP
– program terminates, pump stops, ► changes to , total time
zeroizess, step time changes to time of entire program and shows total
number of steps
.
Pump keeps setting from last program step.
REPEAT
– program ends and prepares for restart, ► changes to
I
►.
Initialization phase proceeds.
Accelerated Option of Program Initialization by Pressing
PUMP
In case that the program has been terminated by
END STEP
(
RUN, STOP
), it is possible to
use the accelerated option of program initialization by pressing key
PUMP
for 3 s. For
RUN
at first
press
PUMP
shortly in order to stop pumping (
change to ) and then after pressing key
PUMP
for 3 s program initiates ( changes to
I
►).
For
STOP
press
PUMP
again longer (
change to
I
►).
Status after Unit Turning Off and On
If
the unit is turned off during running program
(e.g. due to power cut), then after unit
restart program sets to status of held program (see chart above) (
► changes to
II)
. Continue the
same way as after holding running program.
If the unit is turned off after program termination
END STEP
(
RUN, STOP
), then after
unit restart program sets to status
STOP
(
RUN
-
changes to ). Continue the same way as
above. If
END STEP
(
REPEAT
), then after unit restart program sets to status of held program (
I
►
changes to
II
). Continue the same way as above.