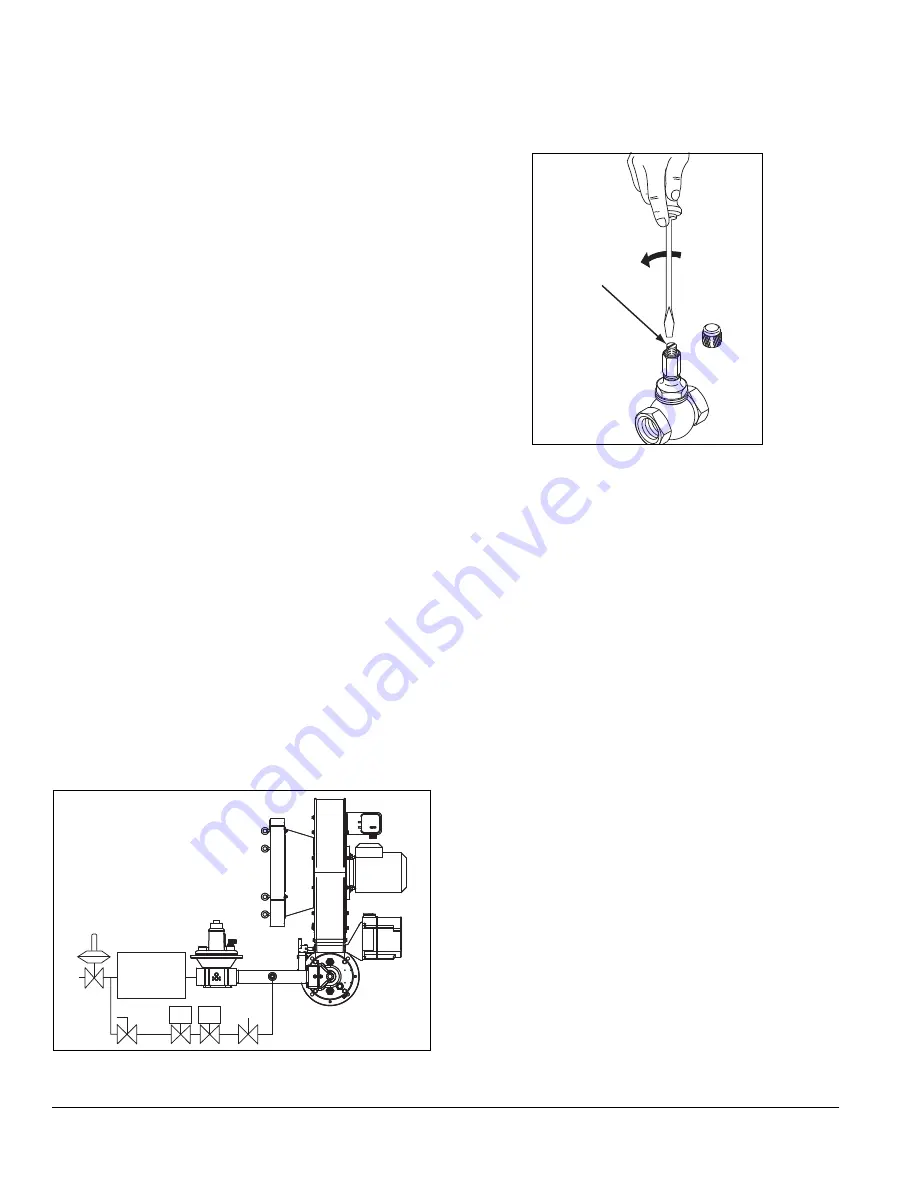
16
Eclipse RatioMatic Burners, RM Series, V5, Installation Guide 110, 12/3/2014
5. Close internal bypass adjusting screw
by turning it
clockwise to closed position.
6. Set system control to stay at low fire during and after
ignition sequence.
7. Attempt to ignite burner.
8. If burner does not ignite:
a. Attempt to ignite burner again to purge air from the
gas piping.
b. If burner still does not ignite, turn bias adjusting
screw
a half turn clockwise to increase gas flow.
c. Attempt to ignite burner.
d. Repeat steps
b
and
c
until burner ignites. If
necessary, refer to Chapter 5 for troubleshooting
tips.
9. After burner ignites, slowly decrease gas flow with
bias adjusting screw
. Decrease gas flow until the
flame signal becomes erratic. (Refer to flame
monitoring relay literature for a description of an
erratic flame signal.)
10. If burner has gone out: Repeat ignition sequence.
Turn internal bypass adjusting screw
a half turn
counterclockwise to increase gas flow at each attempt
until burner lights.
11. Flame signal strength: Adjust gas flow with internal
bypass adjusting screw
for lowest gas flow that
maintains a stable flame signal:
• clockwise, for more fuel
• counterclockwise, for less fuel
12. Verify low fire flame:
a. Shut off gas. When chamber temperature is below
250°F (121°C), shut off combustion air blower.
b. Restart combustion air blower and ignite burner.
c. Verify repeatability of ignition and low fire flame
signal.
Procedure C: Bypass start gas
without
fuel orifice
meter
Figure 4.11. Procedure C
1. Drive control motor to low fire.
2. Be sure combustion air blower is running.
3. Be sure main gas manual shut off valves are closed.
4. Open main gas manual shut off valve
in the bypass.
Figure 4.12. Adjusting Limiting Orifice (ALO)
5. Set the system to operate on bypass gas only.
6. Attempt to ignite burner by energizing spark and
bypass gas solenoid valves
.
7. If burner does not ignite:
a. Attempt to ignite burner again to purge air from the
gas piping.
b. If burner still does not ignite, turn ALO adjusting
screw
a half turn counterclockwise to increase
gas flow.
c. Attempt to ignite burner.
d. Repeat steps
b
and
c
until burner ignites. If
necessary, refer to Chapter 5 for troubleshooting
tips.
8. Flame signal strength: Adjust gas flow ALO adjusting
screw
for lowest gas flow that maintains a stable
flame signal:
• counterclockwise, for more fuel
• clockwise, for less fuel
9. Verify low fire flame:
a. Shut off gas. When chamber temperature is below
250°F (121°C), shut off combustion air blower.
b. Restart combustion air blower and ignite burner.
c. Verify repeatability of ignition and low fire flame
signal.
Main gas
shut-off
valve train
NC
NC
CCW for
more gas
Cap
ALO
Adjusting
Screw