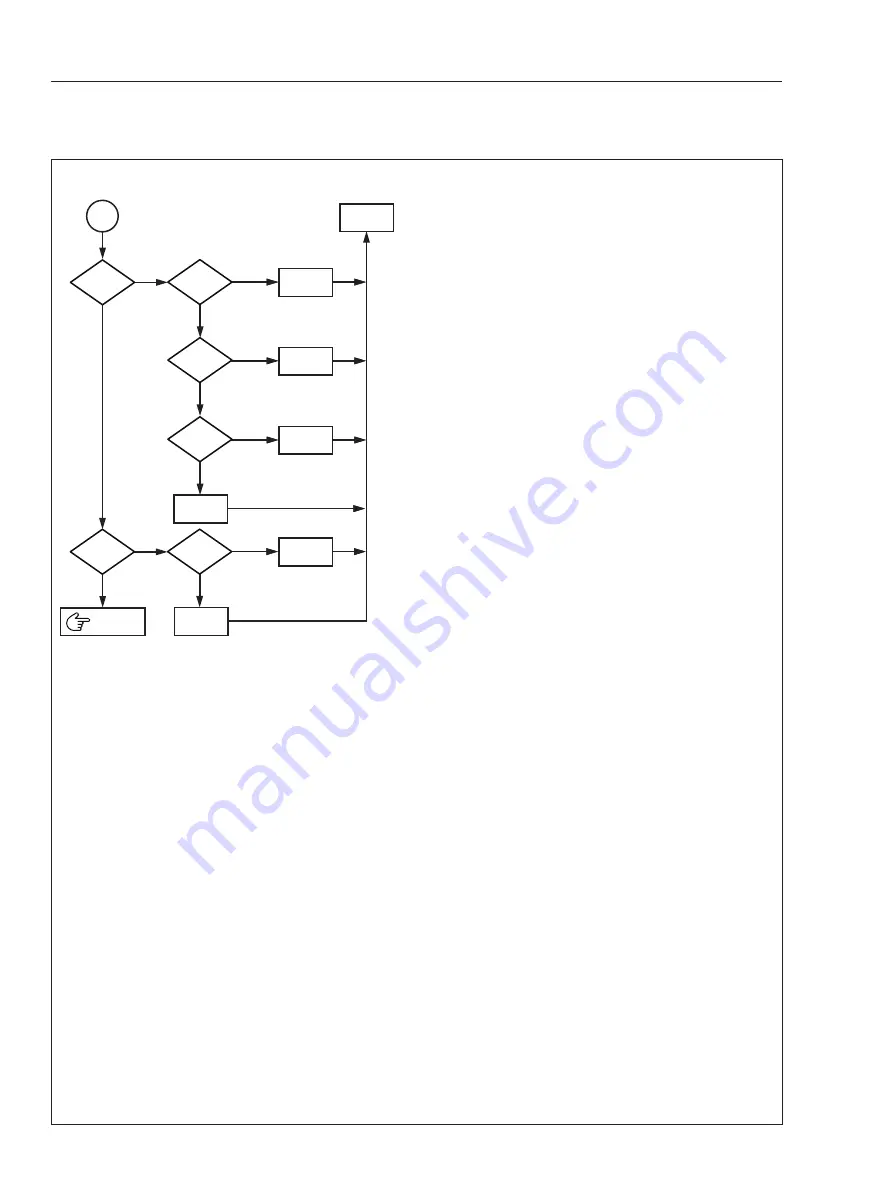
TROUBLESHOOTING
16
DCS-1600
2-2 Troubleshooting chart (Continued)
Troubleshooting "STEP7" ~Checking other failure (Continued)~
(10)
Yes
A
No
No
Yes
B
C
E
Yes
No
D
C
Yes
No
F
G
No
Yes
H
No
Yes
B
C
J
Step0
K
From page 15
A:
Motor speed can not be increased or is not stable.
B:
Inspect the unit as follows:
1) Sprocket is clogged with saw dust or something.
2) Unsuitable saw chain or guide bar is used.
3) Saw chain tension is too tight.
4) There is trouble in drive system.
C:
Clean, repair or replace the object(s) as needed.
D:
Can variable speed switch be pushed to the end?
Check the position and the part itself. (Refer to
Section 5-2)
E:
Repair or replace the variable speed switch as
needed.(Refer to Section 5-2)
F:
Inspect the unit as follows:
1) Each connection between terminals is secure.
2) Each connection of terminal housing and lead is
secure.
3) Electrical current can flow through each lead.
4) There are
no
short curcuits.
G:
Control board or motor may be defective. Prepare
control board and motor and then cross-check.Re-
place the defective one with new one.
H:
Abnormal noise occurs when runnning.
J:
Replace motor with new one.(Refer to Section 6-2)
K:
Go to page 15 (11).