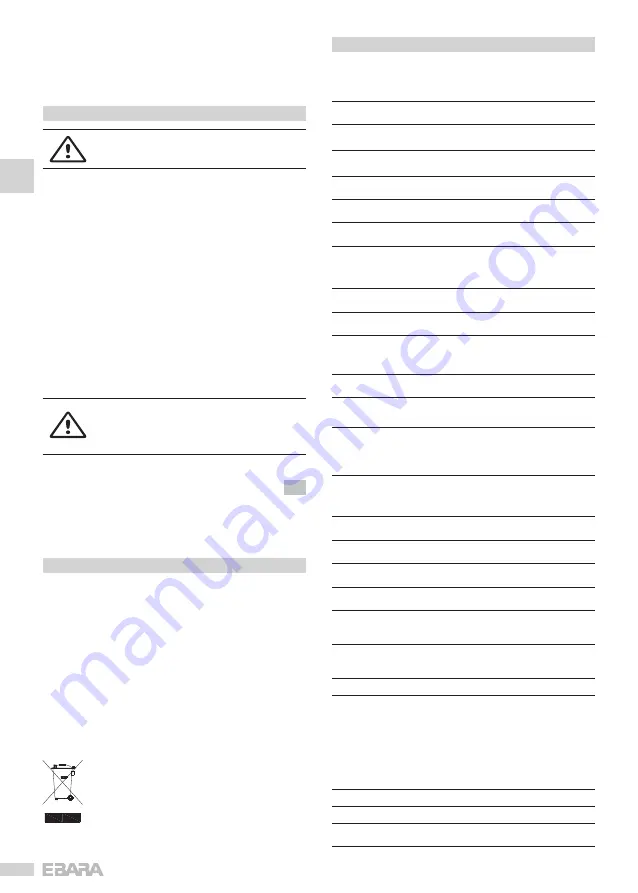
18
EN
overpressure in the piping and pump caused by water hammering;
b) Cut off the power supply.
12. MAINTENANCE AND REPAIRS
Before commencing any maintenance work on the
motor-driven pump, turn off the power.
The electric pump has no need of scheduled maintenance; however, you should
periodically check that it is running properly depending on the fluid being pumped
and the operating conditions; check in particular for abnormal running noise and
vibration.
Said checks may give you a rough idea of what preventive repairs are required, if
any, instead of having to perform repairs following sudden problems.
The main and most common special maintenance operations are generally as
follows:
− replacement of mechanical seals
− replacement of grommets
− replacement of bearings
− replacement of capacitors. (where present)
Nonetheless, even these parts typically subject to wear may last a very long time
if the pump is used correctly.
When the pump remains inactive for a long period, it should be emptied
completely, removing the discharge and filling caps, washed carefully with clean
water then emptied. Do not leave water deposits inside. This operation must
always be carried out whenever there is a chance of frost in order to avoid the
breakdown of the pump components.
When performing repair work, order original spare parts
from our sales and customer support network.
Non-original spare parts can damage the product and are a
hazard for persons and property.
12.1 REPLACEMENT OF SHAFT SEAL
[-E-]
In case of explanations, contact our assistance centre.
13. DISPOSAL
This product falls within the scope of Directive 2012/19/EU regarding the
management of electrical and electronic equipment waste (WEEE).
Electronic-electrical equipment must not be disposed of with domestic waste as
it is made of various materials that can be recycled at the appropriate facilities.
Inquiries should be made through the municipal authorities regarding the
location of the ecological platforms that receive products for disposal and their
subsequent correct recycling.
Furthermore, it is worth remembering that, upon purchase of an equivalent
appliance, shops are obliged to collect the product for disposal free of charge.
This product is not potentially dangerous for human health and the environment,
since it does not contain harmful substances as per Directive 2011/65/EU
(RoHS), yet if abandoned in the environment it has a negative impact on the
ecosystem.
Read the instructions carefully before using the appliance for the first time. It is
recommended that you do not use this product for any purpose other than that
for which it was intended; there is danger of electric shock if used improperly.
The crossed-out bin symbol found on the appliance label indicates
the compliance of this product with the regulations regarding
electrical and electronic equipment waste.
Abandoning the appliance in the environment or its illegal disposal
is punishable by law.
14. TROUBLESHOOTING
14.1 THE PUMP DOES NOT WORK
the motor does not turn
No electricity
Check the electrical supply meter
Plug not inserted
Check the connection to the power supply
Incorrect electrical connection Check the terminal board and the electrical
panel
Automatic switch triggered or
fuses blown (*)
Reset the switch or replace the fuses and
verify the cause
Float sticking
Check that the float reaches the level ON
Thermal protection activated
(single phase)
It reactivates automatically
(single phase only)
Built-in thermal overload
protection device (if fitted) or
thermal cutout in control panel
tripped (*)
Wait for built-in thermal overload protection
device to reset or reset thermal cutout in
control panel
Device protecting against dry
running tripped (*)
Check water level and/or correct connection
of system devices
Hydraulics blocked
Check the hydraulic part. Remove the
foreign bodies, blocking the impeller.
Overload protection tripped or
not properly calibrated.
Check whether the calibration of the
amperometric protection has been properly
calibrated (maximum line current value of
the motor).
Undersized or damaged
capacitor (motor 1 ~).
Verify proper functioning of the capacitor. If
necessary, provide for a larger capacitor.
Motor burned down due to
insulation fault, overheating or
overload (unsuitable liquid).
Measure the insulation resistance of the
winding towards the grounding and make
sure it is greater than 10MΏ
Powered by 2 phases
(motor 3~)
.
Check how many stages have been
connected in the terminal box of the motor
and check the actual presence of voltage
on the 3 stages using a voltmeter, during
pump operation.
the motor turns
Decrease in the line voltage
Wait for voltage to return to normal
Suction filter / hole blocked
Clean the filter / hole
Foot valve blocked (**)
Release or clean the valve and check that it
works properly
Pump has not been filled (**)
Fill (sect. 10)
Water level low (if no
protection system is fitted) (**) Restore water level
Pump not primed
Prime the pump
Check any delivery non-return valves
Check the liquid level
Pressure too low
Restrict the delivery gate
(*) If you encounter the same trouble again, call our Servicing Department
(**) Caution: mechanical seal could be damaged
14.2 THE PUMP WORKS
with a reduced flow rate
System undersized
Reviewing the system
System dirty
Clean the piping, valves, filters
Water level too low
Switch off the pump or immerse the foot
valve
Summary of Contents for EVMS 1
Page 85: ...85 12 13 14 9 8 10 11 A EVMS 1 3 5 10 15 20 3 Nm...
Page 87: ...87 A EVMS 32 45 64 90 without ball bearing 9 10 11 12 13 14 15 5 Nm 2 min...
Page 88: ...88 A EVMS 32 45 64 90 with ball bearing 2 min 1 2 3 4 5 7 6 M8 20 Nm M12 40 Nm M16 70 Nm...
Page 91: ...91 E EVMS 1 3 5 10 15 20 4 kW 1 2 3 4 5 6 7 8 9 10 3 Nm M6 10 Nm 11 12...
Page 92: ...92 E EVMS 1 3 5 10 15 20 5 5 kW 1 2 3 4 5 6 7 8 9 10 11 12 3 Nm M8 18 Nm M10 50 Nm...
Page 97: ...97...
Page 98: ...98...
Page 99: ...99...