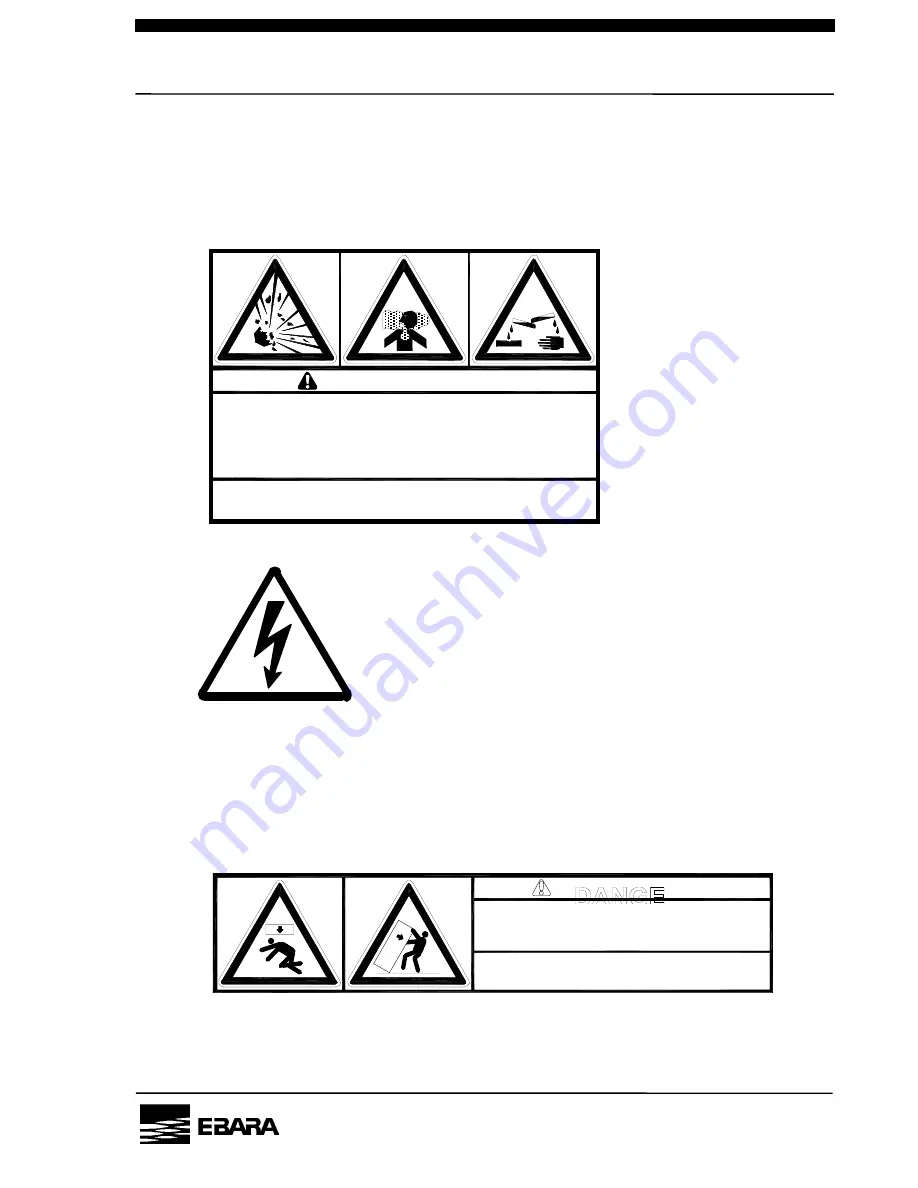
(
vii
)
PM10U
EBARA
CORPORATION
3. Hazardous materials warning
In case of hazardous materials are handled. Run the pump only with
N2 gas purge before servicing. Take adequate measures against
dangerous reaction and contact with human body.
4. Electric charge mark
5. Hazardous weight danger
Heavy weight may cause severe injury or death due to overturning
or falling pump. Keep out from under the lifted pump.
Raise all adjuster-feet fully when moving.
WARNIN
警
告
Hazardous Materials
Exposure to air may cause spontaneous fire or explosion.
Inhalation or skin absorption will cause severe injury or
death by poisoning.
Purge thoroughly with nitrogen for at least 30 minutes
before servicing. Use personal protective equipment
appropriate to the materials to prevent exposure.
危険物質あり。
危険反応・人体への接触により重傷または死亡の危険があります。N2パージのみで30分以上
空運転を行なってから、危険物質のMSDSに従ってメンテナンスをして下さい。
C-7110-314-0001
危
険
Heavy Object
Can cause impact injury through falling or tipping.
Use appropriate, properly rigged lifting equipment and keep from
under suspended pump. Raise all adjuster feet fully when moving.
重量物。落下及び転倒により重傷または死亡の危険があります。
吊り上げたポンプの下に入らないで下さい。
移動時は全アジャスタフットを上限まであげて下さい。
C-7110-316-0001