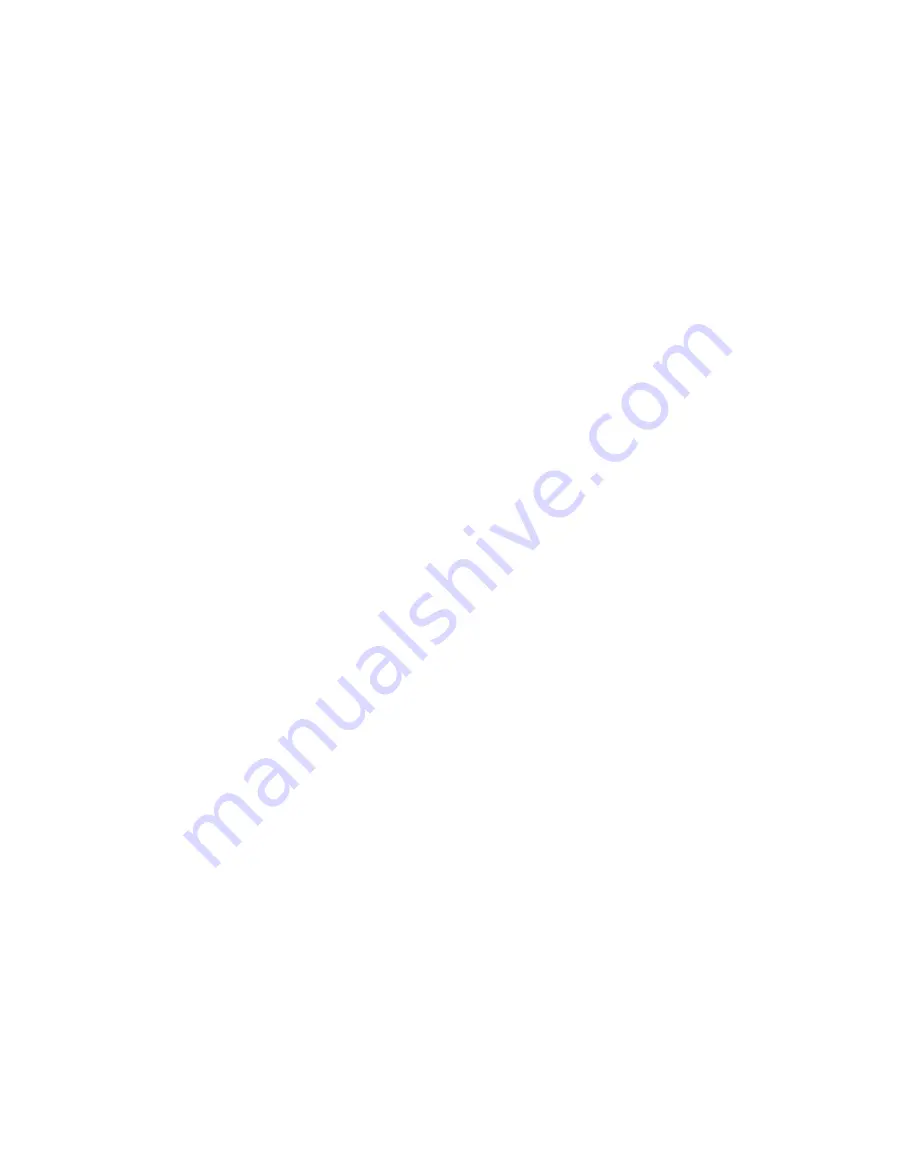
21
X70 PLUG-IN MOTOR REPAIR MANUAL
E-MOPI-RR009-E—March 2019 www.eaton.com
Start-Up Procedure
When initially starting a new or a rebuilt transmission
system, it is extremely important that the start-up procedure
be followed. It prevents the chance of damaging the unit
which might occur if the system was not properly purged of
air before start-up.
1. After the transmission components have been properly
installed, fill the motor housing at least half with filtered
system oil. Connect all hydraulic lines and check to be
sure they are tight.
2. Install and adjust all control linkage.
3. Fill the reservoir with approved oil that has been filtered
through a 10 micron filter. Refer to Eaton Hydraulics
Technical Data sheet number 3-401 titled Hydraulic Fluid
Recommendations.
4. Gasoline or L.P. engines: remove the coil wire and turn
the engine over for 15 seconds. Diesel engines: shut off
the fuel flow to the injectors and turn the engine over for
15 seconds.
5. Replace the coil wire or return the fuel flow to the
injectors. Place the transmission unit in the neutral
position, start the engine and run it at a low idle. The
charge pump should immediately pick up oil and fill the
system. If there is no indication of fill in 30 seconds, stop
engine and determine the cause.
6. After the system starts to show signs of fill, slowly
move pump Swashplate to a slight cam angle. Continue
to operate system slowly with no load on motors until
system responds fully.
7. Give supply to the control port of the motor to see if the
motor responds to the signal.
8. Remove the control port pressure and observe if the
motor comes to original speed/displacements.
9. If not, troubleshoot the motor as per Eaton repair manual
10. Check fluid level in the reservoir and refill if necessary to
the proper level with approved filtered oil.
11. Check all line connections for leaks and tighten if
necessary.
12. The machine is now ready to be put into operation.
13. Frequent filter changes are recommended for the
first two changes after placing the machine back into
operation. Change the first filter in 3-5 hours and the
second at approximately 50 hours approx. hours.
Routinely scheduled filter changes are recommended for
maximum life of the hydraulic system.
Testing
Perform functional test on motor according to Eaton test
procedure.