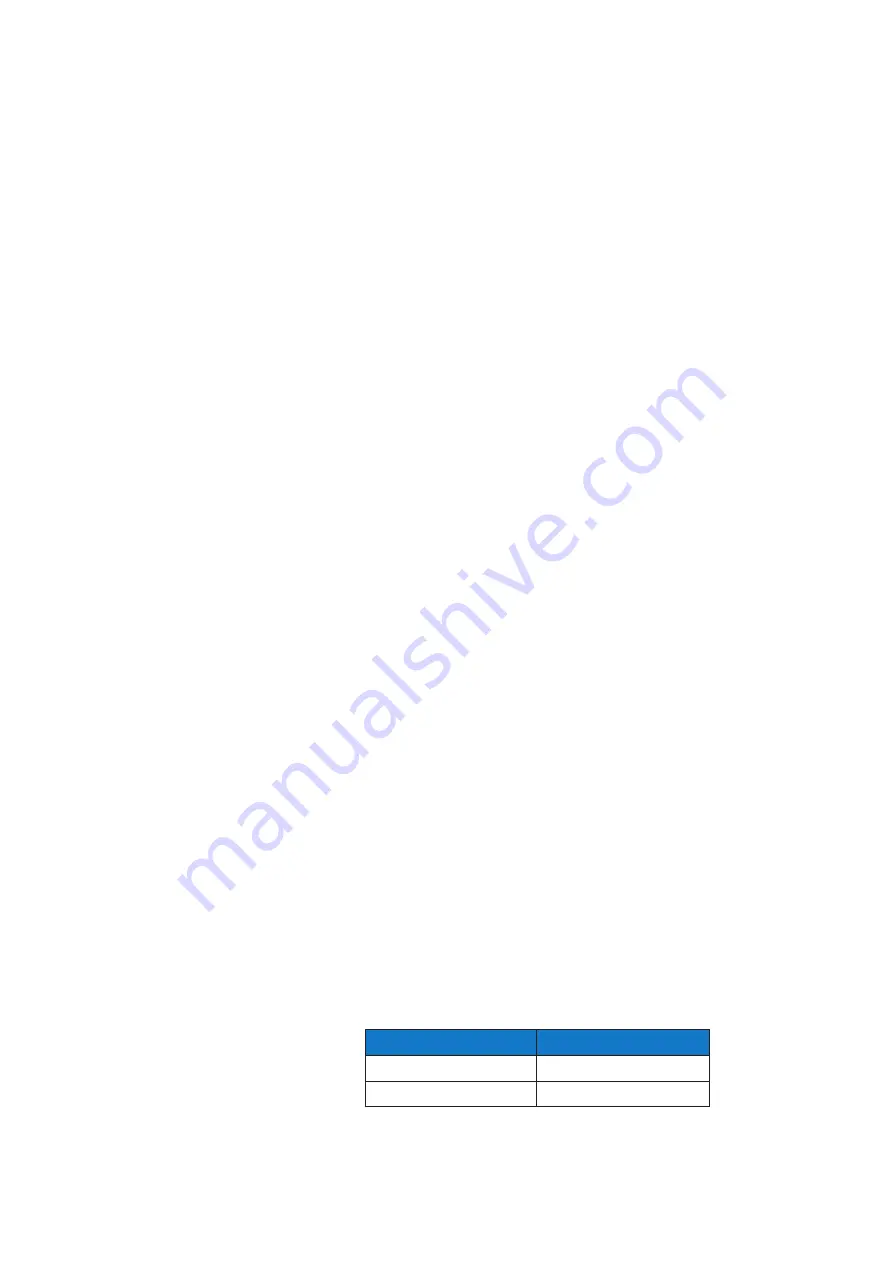
INM MTL 130-0202 Rev 4
23
6.9.2 Removal and replacement
The power supply to the instrument must be completely disconnected.
The stainless steel electronics unit mounts to the backplate of the enclosure on four captive
studs, two each side, and is secured to each with a nut, a locking washer and a plain washer -
see Figure 4 (page 8) for details.
1. Remove the nut on the backplate grounding stud so that the earth wire connected to
the steel casing of the control unit can be detached easily at the end of the next step.
2. Support the control unit while removing the nuts and washers from the studs. The
electronics unit can then be detached from the connectors at the rear together with its
earth wire.
Replacement is the reversal of removal. Before fitting the replacement electronics ensure that
it is configured for the same supply voltage as the one it is replacing, this can be determined
from the label on the side of the electronics unit. If in doubt, contact your local MTL Gas
sales office who will require the serial numbers of both the old and the new units to check
the details.
1. Thread the earth wire behind the lower cover then carefully align the new module into
position on the mounting studs. Carefully press the module into position to fully engage the
rear connectors.
2. While supporting the unit in place, fit a plain washer and a locking washer over one of the
top studs and spin a nut onto it until finger-tight. Do the same on the other top stud to
secure the unit. Fit the lower washers and nuts in a similar manner then tighten all four
nuts to a suitable torque value.
3. Refit the earth wire, with the others, on the backplate grounding stud and replace the
securing washer and nut. Tighten to a suitable torque value.
The instrument will now need to be calibrated and any user configuration settings will need to
be re-entered. See sections 5.3 and 6 for details.
6.10 Restoring factory defaults
This procedure may be used where mis-calibration is producing unacceptable errors and re-
calibration is not possible – e.g. no gas available.
This procedure should be carried out by qualified service personnel only, and only as indicated
by the fault finding requirements set out in the trouble-shooting chart in section 7.3.
6.10.1 Tools required
None
6.10.2 Instructions
Disconnect the instrument from its power supply and leave for 30 seconds. Whilst keeping
the
Cal
button depressed, apply power to the instrument. Continue to hold the
Cal
button
until a ‘Calibration data lost’ message appears on the display.
Connect a dry air source to the instrument and flow air at approx 200 ml /min through the
sensor and check the chlorine and hydrogen zero accuracy against the table below. If the
readings are outside the limits shown, it is likely that the katharometer sensor is contaminated
and will need cleaning. See section 7.6 for the cleaning procedure. Should the cleaning not
restore operation to within limits shown below, the sensor and its KIM should be replaced.
If the results are within the limits shown here, recalibrate the analyser and restore the
customer settings from the noted values above.
6.10.3 Acceptable limits
Reading
Error - %Absolute
Chlorine
± 8%
Hydrogen
± 1%
These limits refer to the zero reading accuracy at room temperature after restoring factory
settings but before performing a gas calibration.