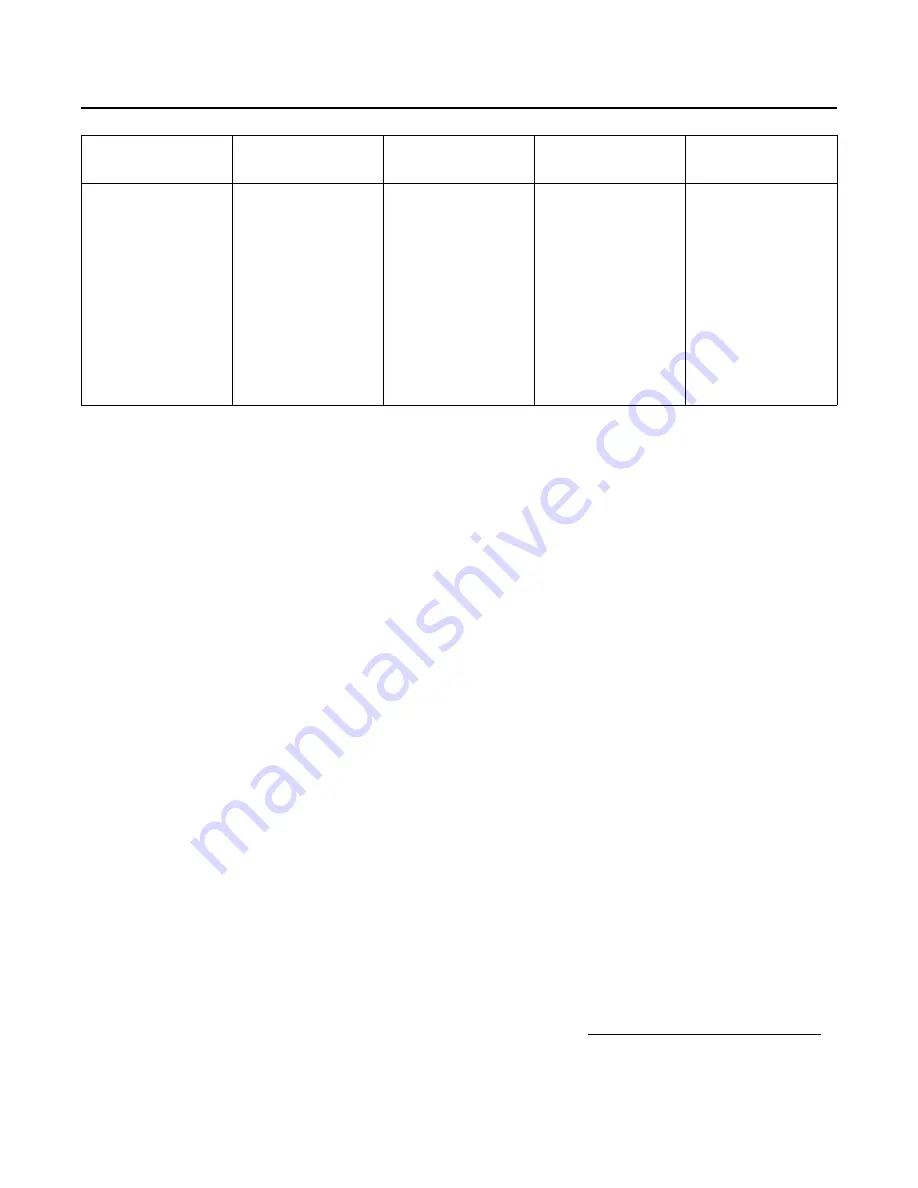
SCALE FACTORS
31
each successive part grows longer by 0.004
inches. Eventually, this cumulative error will cause
the part to be out of tolerance.
Typically, those applications which require Func-
tion 83 to have a value of “1” are cut-to-length
applications. When the application is performing a
repetitive process such as punching equally
spaced holes in a single part, the scaler should
retain partial counts for the next measurement. In
these cases, Function 83 should be set to “0”.
Whenever the Reset key is pressed or the Reset
Input is energized, the scaler is always reset, elim-
inating any remaining partial counts. This is
regardless of the value entered in Function 83.
CALCULATING THE SCALE FACTOR
There are four general categories of applications
which require scaling. The method of calculating
the scale factor differs for each. The categories
are:
1. Allowances for wear of measurement devices
and material stretch applications.
2. Unit conversions (typically when the measure-
ment system is set up for measuring one unit
and the part must be made in another; i.e.,
inches versus millimeters.)
3. Scaling of pulses received from flowmeters or
other sensors which produce a non-standard
number of pulses per unit of measure.
4. Allowing multiple parts to be made for each
operation of a machine.
A discussion of the means of calculating the scale
factor for each category and special problems
involved follows.
Allowances for Wear or Stretch
Over a period of time a measuring wheel will begin
to wear. The wheel allows accurate measurement
only when its circumference is a known, fixed
value. Thus, as the wheel wears, the error in the
measurement increases because the circumfer-
ence of the wheel becomes less and less. Scaling
provides a means to compensate for the decreas-
ing wheel circumference. This allows the useful life
of the measuring wheel to be extended, decreas-
ing cost.
In applications where the material stretches or
shrinks by a fixed amount, scaling allows compen-
sation for gained or lost material. These applica-
tions required that the amount of stretch or
shrinkage be known, measurable or calculable
and that it be consistent from machine cycle to
machine cycle.
In either case, the scale factor is calculated by
using the formula:
Measured or Calculated Distance
Scale Factor =
Theoretical Distance
PULSES
RECEIVED
RESULT
CALCULATED
DISPLAY
VALUE
SECOND CYCLE
RESULT
SECOND CYCLE
DISPLAY
1
2
3
4
5
6
7
8
9
10
11
12
1.3000
2.6000
3.9000
5.2000
6.5000
7.8000
9.1000
10.4000
11.7000
13.0000
14.3000
15.6000
1
2
3
5
6
7
9
10
11
13
14
15
1.9000
3.2000
4.5000
5.8000
7.1000
8.4000
9.7000
11.0000
12.3000
13.6000
14.9000
16.2000
1
3
4
5
7
8
9
11
12
13
14
16
Figure 25.
Pulses Received versus Display Value Using Scale Factor of 1.3000