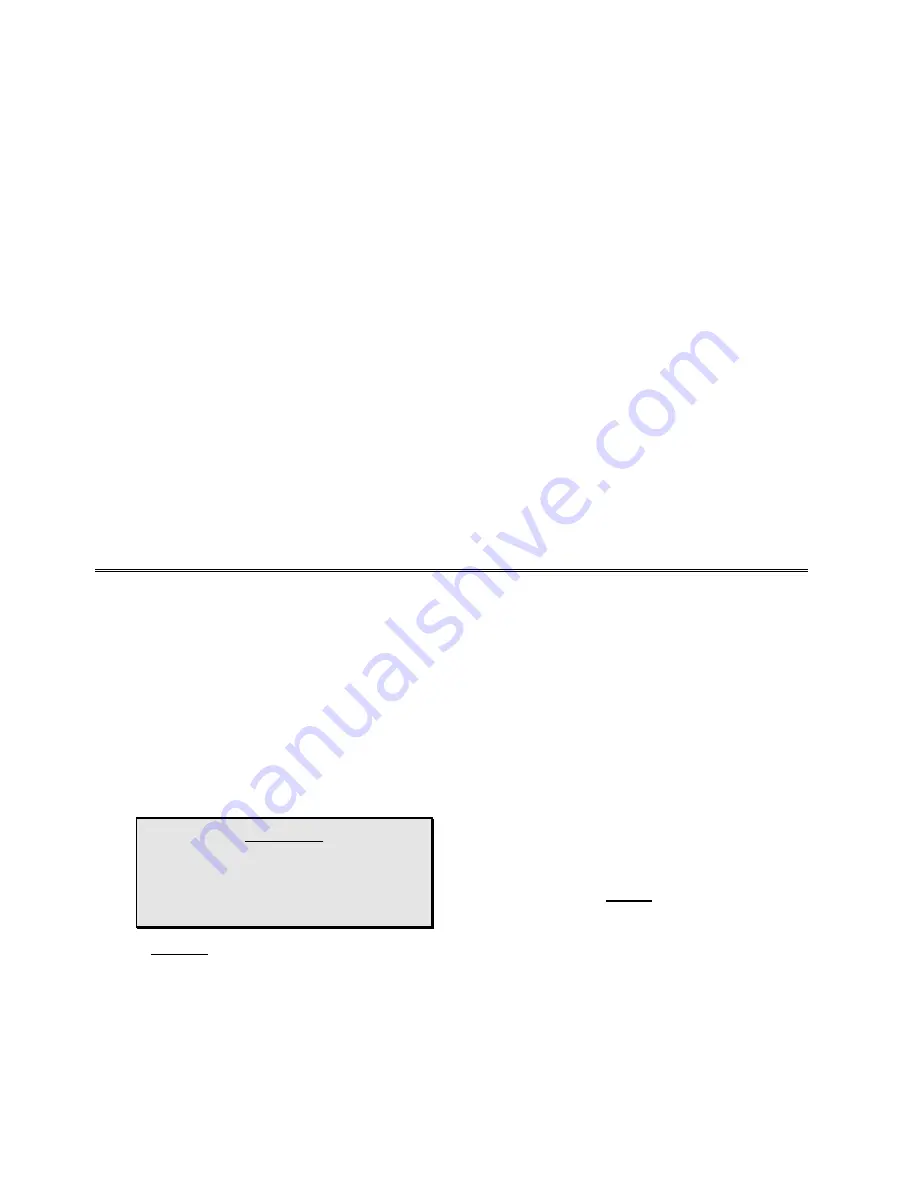
SM64200
February
2007
10
exceeding 15% of local wall thickness.
Use alodine 1200 to touch up bared
aluminum. Precisely measure the
following items. Replace any part that
exceeds the identified maximum or
minimum wear limits:
•
Both holes in item 28 Link - .196 inch
(4.98 mm) diameter max. & .318 inch
(8.08 mm) diameter max.
• Hole in item 32 Shaft – .198 inch
(5.03 mm) diameter max.
•
Bearing diameter of item 31 Pin - .186
inch (4.70 mm) diameter min.
•
Shaft of the Shaft Assembly (33) – No
part of it shall be less than .621 inch
(15.77 mm).
•
Interlock Plate (10) – Visually check
for wear on the corners of the tabs
protruding from the outer diameter. If the
corners are rounded off, replace this part.
•
Wear Ring (42) – If the diameter of
the wire is less than 0.075 inches (1.905
mm) at any place around the major
diameter or there are obvious worn or flat
spots replace it.
• Retainer (9) – Carefully inspect for
any cracks in the part. Replace as
needed.
•
Inspect Bracket (100), (85) or (93) if
present for wear that will cause the item to
be non-fuctionable.
•
Measure the larger diameter of item
29 Pin next to the head in at least two
opposing directions. The larger diameter
should not be less than 0.298” (7.60 mm).
If it is at this diameter or less, it has to be
replaced. Characteristic wear on the older,
softer pin results in an elliptical shape rather
than a diameter. This tends to make the
nozzle more difficult to close and results in
possible leakage when it is closed.
•
If present inspect Drag Ring (72) and
the adjacent HECV. If the ring is worn to
a point where the HECV body is being
dragged, replace the ring.
• If present inspect Gage (89) for
damage and replace if needed.
8.0 REASSEMBLY
8.1
Reassemble in reverse order of
disassembly (Refer to Figure 2),
observing the following:
8.1.1 Make certain all components
are clean and free from oil, grease, or
any other corrosion resistant compound
on all interior or exterior surfaces.
Wash all parts with cleaning solvent,
and dry thoroughly with a clean, lint-
free cloth or compressed air.
WARNING:
Use cleaning solvent in a well-
ventilated area. Avoid breathing of
fumes and excessive solvent contact
with skin. Keep away from open flame.
DO NOT use any form of grease on Balls
(3) and be certain to install proper
number of balls in each hole of Body (6)
and collar assembly. Count the number
of Balls (3) to be sure that a total of 39
are to be replaced. Also make sure that
Clip (4) is installed properly to maintain
continuity through the unit. Refer to
Figure 5 for installation information.
NOTE: A light coat of petroleum jelly
can be applied to all O-rings, springs,
and non-locking screws for ease of
installation.
8.1.2 When installing Pin (31) in
place it can be inserted into the Link
(28) and Shaft (32) outside of the body
and held in place by a small piece of
tape while assembling into the unit. Be
sure to remove the tape afterwards.
One can also hold the pin in place with
one finger while inserting.
Reinstall the Plug (5) after completing
assembly of the internal parts of the
nozzle. NOTE: The Plug (5) has a
sealant already in place and can be
reused for several times. If Teflon tape
is used on reinstallation, do not utilize
more than 1 1/2 wraps of tape.
Excessive use of tape could lead to the
cracking of the Body (6).
8.1.3 If the Poppet Assembly (13)
was disassembled a coating of
petroleum jelly and the use of tweezers
to install the small Balls (16) will make
Summary of Contents for Carter 64200
Page 15: ...SM64200 February 2007 15 FIGURE 1 64200 PARTS BREAKDOWN ...
Page 16: ...SM64200 February 2007 16 FIGURE 2 64200 OPTIONS ...
Page 17: ...SM64200 February 2007 17 FIGURE 3 Holding Bracket Circular and Stirrup Handle Installations ...
Page 18: ...SM64200 February 2007 18 CONTINUITY CLIP INSTALLATION FIGURE 5 POPPET COTTER PIN INSTALLATION ...
Page 21: ...SM64200 February 2007 21 ...