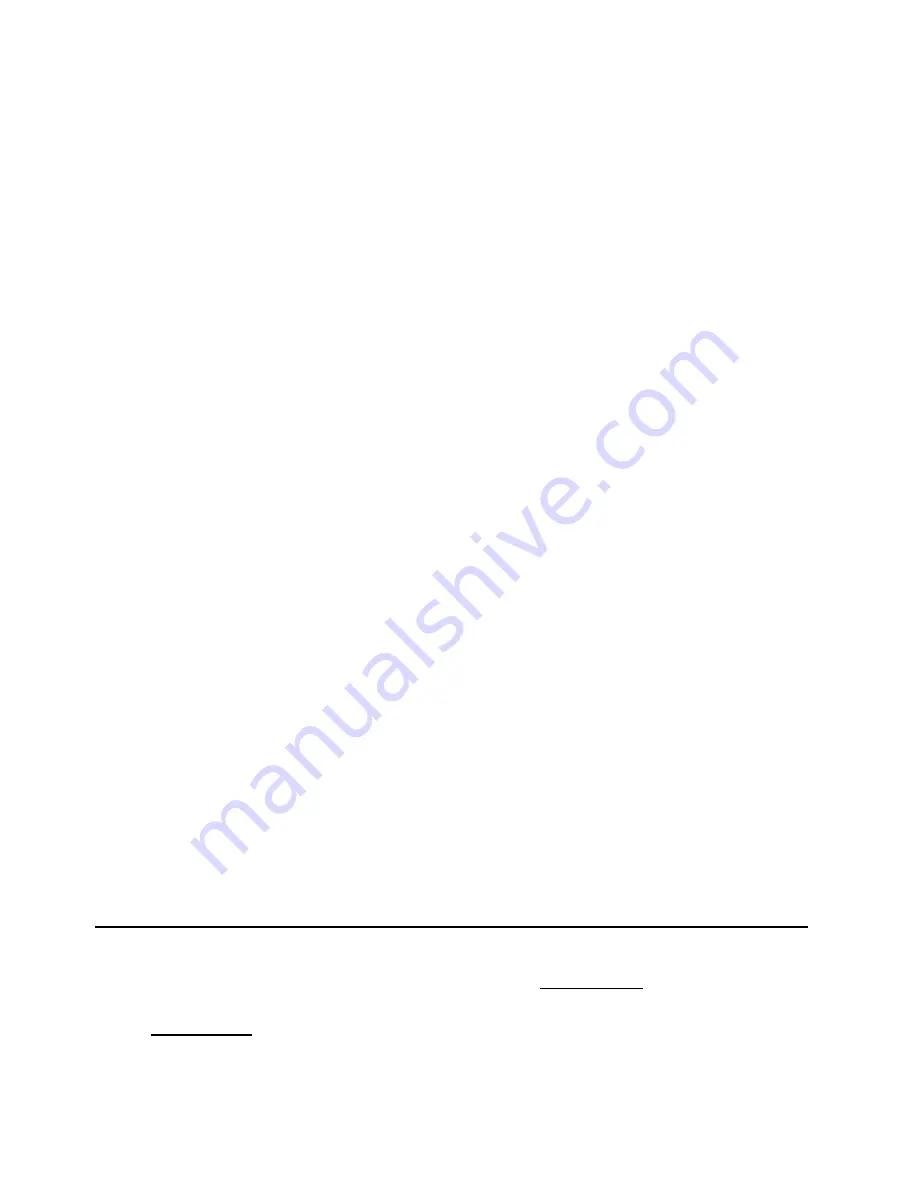
SM64200
February
2007
11
the job easier. There are 22 of the
balls.
8.1.4 When reinstalling the Nose
Seal (21) care should be taken to
position it with two lugs placed within
the large grooves in the Body (6) and
the flat part of the tongue of the nose
seal up against the Link (28) when the
operating Arm (27A or B) is in the
nozzle open position. Seat the Nose
Seal (21) into the Body (6).
8.1.5 The
standard
poppet
adjustment tool used on previous
Carter nozzles will not work on the
64200. A good starting point in
adjusting the poppet is to bottom the
poppet onto the Shaft (32) with the
nozzle open, then back it out
approximately 1.75 turns. Once the
adjustment is made, rotate the Poppet
toward the tightening direction until the
next slot in the Poppet (19) is in line
with the hole in the Shaft (32). Insert
the Cotter Pin (12) but do not bend the
ends at this time. Close the nozzle and
check the adjustment with the poppet
adjustment tool. If the adjustment is not
within the “go-no-go” range, remove the
cotter pin and re-adjust until the correct
dimension is achieved. Then bend over
the ends of the Cotter Pin (12) to retain
in place in accordance with Figure 5.
Note it is important that the correct
length of Cotter Pin (12) is utilized for
the assembly
8.1.6 Use the adapter to rotate the
nose seal counter-clockwise to the
nozzle-closed position.
8.1.7 Install Plate (10) and Springs
(11) noting that the four indentations on
the plate must fit into each of the four
springs.
8.1.8
Hold the Plate (10) in position
and install the Retainer (9) with the six
Screws (8). These screws should be
torqued to 50 in-lbs. (0.58 m-kg).
8.1.9
Reinstall the Bumper (7).
8.1.10 If the Grip (45C), (48), (50) or
Handle Assembly (52) or (94) requires
replacing due to wear or the
replacement of the Cover (51), the new
Grips (45C), (48), (50) or Handle
Assembly (52) or (94) shall be
reinstalled using the appropriate screws
and washers.
8.1.11 Note that Bearing (36A) must
be installed into the handle shaft hole in
the Body (6) from the inside and must
be seated in place prior to installing the
Crank Shaft Assembly (33).
8.2
CRITICAL ASSEMBLY NOTE:
Where
applicable on assembly of an accessory
to this nozzle, the following torquing
sequence and values for the mating to
the nozzle should be used:
8.2.1 The six screws accompanying
the accessory should be torqued to 75-
79 in-lbs. (8.5-9 N-m). Tighten all
screws to bottom the heads against the
flange without over tightening.
8.2.2 Then start with one screw,
mentally numbered “1” working in
a clock-wise pattern, tightening
approximately to half of the end torque
values above. Skip across to screw “4”
followed by “6:, “2”, “5” and finally “3”.
8.2.3 Repeat the tightening at the final
torque value above in the same pattern.
8.3
If Gage (89) is to be replaced use a
maximum of 1 ½ wraps of Teflon tape
on the Bushing (90) when installing into
Body (6) to prevent cracking the boss
wall. The Gage (89) can be installed in
either port.
9.0 TEST
9.1
The following test procedures will be
accomplished after overhaul:
9.2 Test
conditions
Test media shall be JP-4, Jet A or
odorless kerosene, commercial solvent
140.
9.3 Functional
Test
9.3.1 The nozzle shall be inserted
and locked into a test adapter, Carter
6958CG or CH or equivalent and the
nozzle valve actuated by use of the
crank Arm (27A or B) from the fully
closed to fully open position a minimum
Summary of Contents for Carter 64200
Page 15: ...SM64200 February 2007 15 FIGURE 1 64200 PARTS BREAKDOWN ...
Page 16: ...SM64200 February 2007 16 FIGURE 2 64200 OPTIONS ...
Page 17: ...SM64200 February 2007 17 FIGURE 3 Holding Bracket Circular and Stirrup Handle Installations ...
Page 18: ...SM64200 February 2007 18 CONTINUITY CLIP INSTALLATION FIGURE 5 POPPET COTTER PIN INSTALLATION ...
Page 21: ...SM64200 February 2007 21 ...