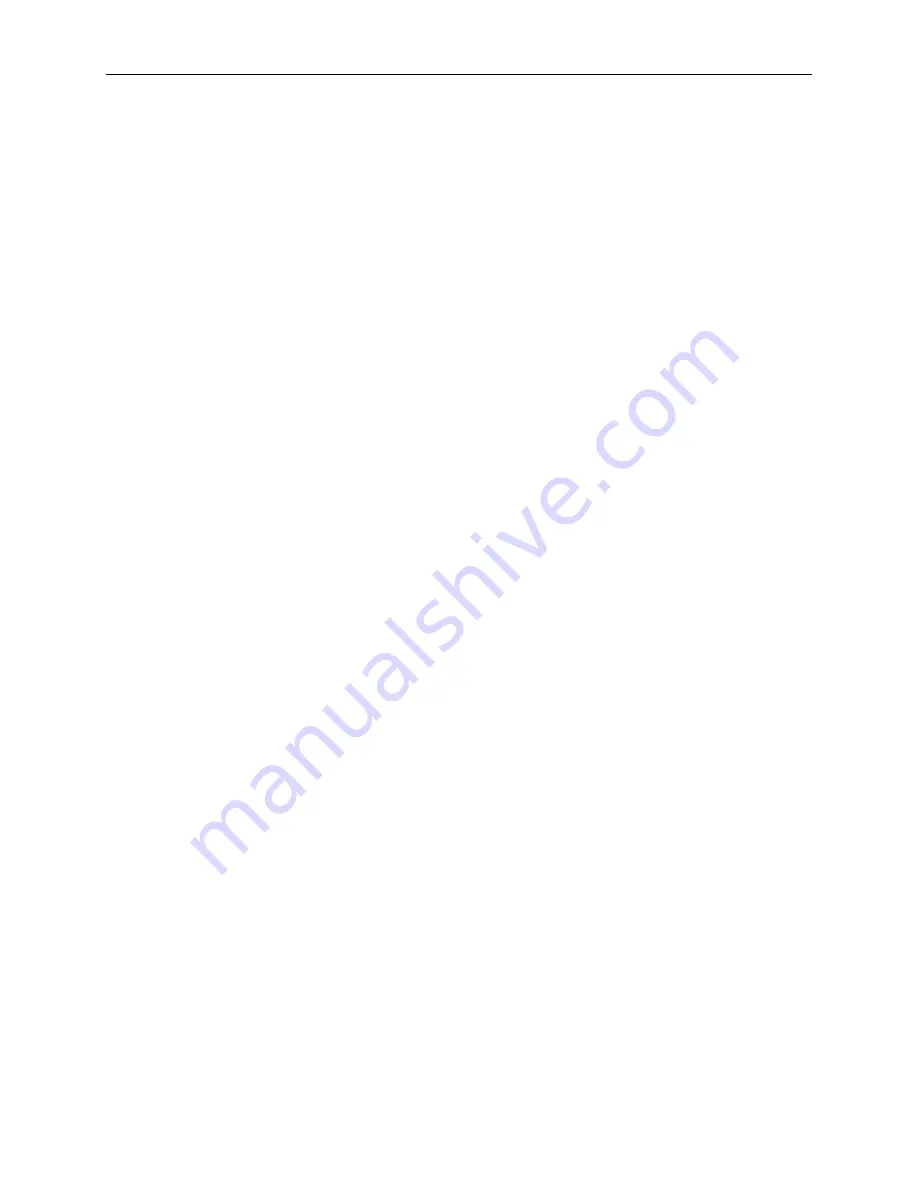
Maintenance 51
Belt Assembly and Disassembly
CAUTION:
Disconnect main power source before performing any
procedure to replace any conveyor component(s).
Whenever possible, for ease of reassembly, try not to remove the conveyor belt
completely from the conveyor frame. Open the conveyor belt only enough to expose
parts that need to be replaced.
Before removing any belt completely, make note of direction of belt lugs so you will
know which direction to face the belt when reinstalling it.
To aid in reinstalling the belt, take note of sprocket locations before disassembly.
Belt Assembly
1. Align the ends of the belt to be connected.
2. Insert the new rod.
3. Use a small, plastic tipped hammer to tap the rod while supporting the outer
knuckle until the head of the rod is flush with the belt.
4. Trim off the excess rod opposite the head flush with the side of the belt.
Belt Disassembly
Before disassembling the belt, follow instructions outlined in the Conveyor Tension
Adjustment section on page 46 of the Adjustments chapter to loosen the belt tension.
Whenever possible, for ease of reassembly, try not to remove the conveyor belt
completely from the conveyor frame. Open the conveyor belt only enough to expose
parts that need to be replaced.
1. Use a small flat-blade screwdriver to gently bend open the belt just enough so
that the rod end will be exposed when the screwdriver is released.
Summary of Contents for EA Professional Series
Page 2: ......
Page 4: ......
Page 64: ...64 Appendix B Temperature Setting Specifications Appendix A Electrical Schematics...
Page 70: ......