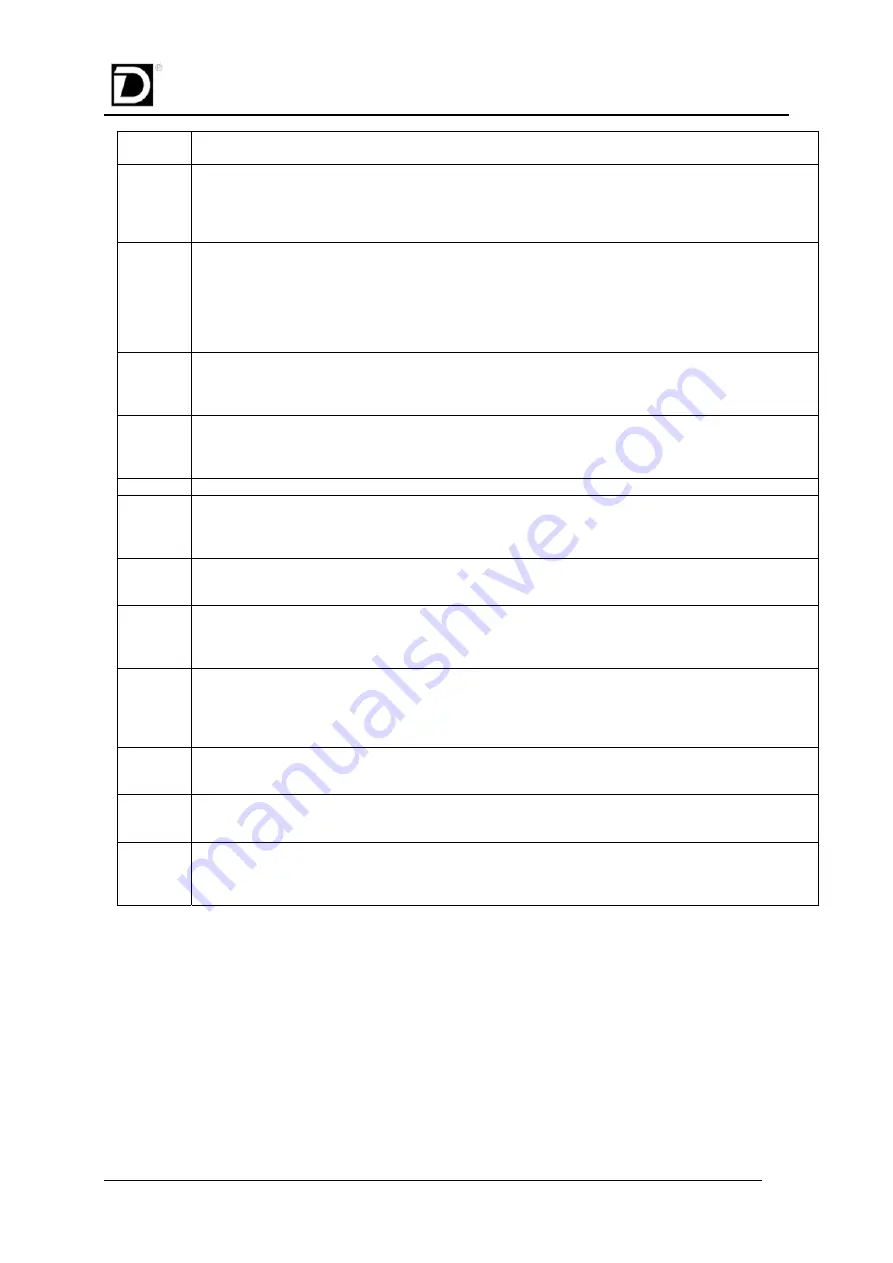
DUPLOMATIC
E.M.6427 RELEASE 7.1 05-03
6427071-230-en 17
ALARM
CODE
Description
50
The signal of the unlocking switch stays on during the locking phase:
-locking pressure too low (only hydraulic);
-bad position of unlocking switch;
-bad switch connection/wiring (remote application mainly);
-the unlocking switch is defective.
51
The signal of the locking switch stays off during the locking phase:
-locking pressure too low (only hydraulic);
-bad position of locking switch;
-bad switch connection/wiring (remote application mainly);
-wrong control unit code (card for a different size);
-wrong reference cam regulation (turret lock over teeth);
-the locking switch is defective.
52
The signal of the locking switch goes off while the turret is locked:
-problems of pressure (only hydraulic);
-bad switch connection/wiring (remote application mainly);
-the locking switch is defective.
53
The signal of the unlocking switch goes on while the turret is locked:
-problems of pressure (only hydraulic);
-bad switch connection/wiring (remote application mainly);
-the unlocking switch is defective.
55
The two pressure inlet or the LOCKED and UNLOCKED switches are reversed. (only SW rel I)
61
Time-out in fine reference search:
-the zero switch is defective (always off);
-bad switch connection/wiring (remote application mainly);
-the disc cannot rotate.
70
A tool is called before executing the zero cycle:
-error in programming logic of CNC;
-the operator did not call the reference cycle.
71
Parity Error in position code:
-error in programming logic of CNC;
-problems on wiring (PBIT** and PARITY)
-slow outputs of CNC/PLC (the output value van be incorrect when the PSTART signal is given)
72
A tool non existing has been called:
-error in CNC programming;
-turret not correctly configured (check the number of positions set by PTAB01 and PTAB02 signals - LK1 and
LK2 in connection box);
-wiring problems.
73
A variation in position code has been detected but the PSTART signal is not arrived in within 2 seconds:
-error in CNC programming;
-wiring problems (PSTART signal not connected).
74
The time limit of continuos rotation of disc has been reached:
-the turret has been activate in maintenance mode or service for long time;
-the indexing frequency is too high.
78 or 77
The configuration input signals PTAB01 and PTAB02 are not configured (number of positions):
-error in PTAB01 and PTAB02 setting (LK1 and LK2 in connection box);
-the 24 V DC supply is delayed for more than 500 ms in respect of the 230 V AC auxiliary supply (the
configuration has not been loaded correctly).
Note:
the code number is memorised by the control unit and can be read with a Duplomatic
diagnostic software installed on a PC with the RS232 interface.