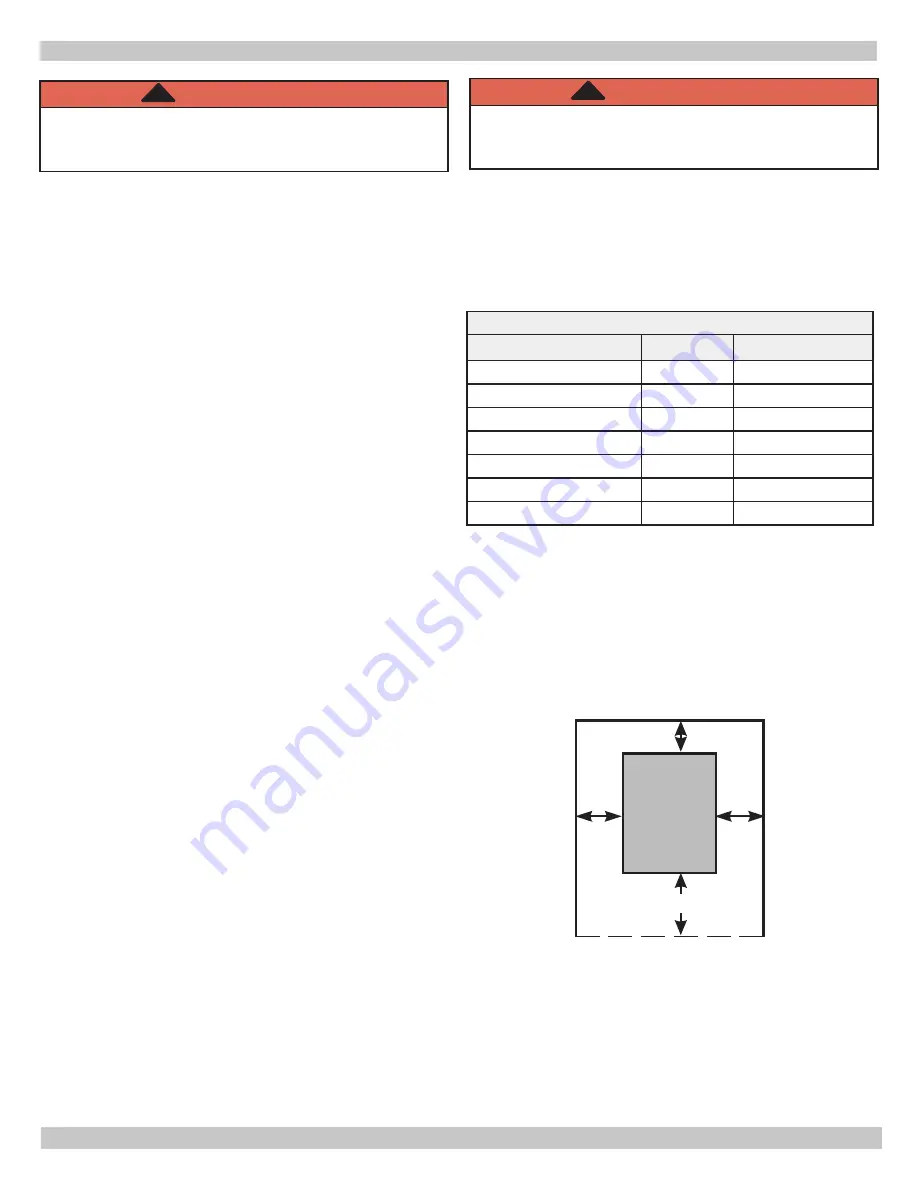
5
LOCATING THE BOILER
Minimum Clearance Dimensions
Table 2 - Minimum Clearances
Alcove
Top
6”
(152mm)
Rear
6”
(152mm)
Control Side
7”
(178mm)
Opposite Side
6”
(152mm)
Front
18”
(457mm)
Flue/Vent Connector
6”
(152mm)
Near Boiler Piping
2”
(51mm)
1.
Installation must conform to requirements of authority
having jurisdiction or, in absence of such requirements,
to the National Fuel Gas Code, ANSI Z223.1/NFPA 54.
2.
Where required by authority having jurisdiction,
installation must conform to the Standard for Controls
and Safety Devices for Automatically fired Boilers,
ANSI/ASME CSD-1.
3.
Boiler series is classified as Category I. Vent
installation shall be in accordance with "Venting of
Equipment ," of the National Fuel Gas Code, ANSI
Z223.1/NFPA 54, or applicable provisions of local
building codes.
4.
Boiler installed in building under construction; take
care to insure clean combustion air supply during
construction process. Airborne particulates from drywall
dust and fiberglass insulation can clog burner ports and
cause incomplete combustion and sooting.
5.
Boiler shall be installed such that gas ignition system
components are protected from water (dripping,
spraying, rain, etc.) during appliance operation and
service, (circulator replacement, condensate trap,
control replacement, etc.).
6.
Locate boiler on level, solid base as near chimney as
possible and centrally located with respect to heat
distribution system as practical.
7.
When installed in utility room, door should be wide
enough to allow largest boiler part to enter, or to
permit replacement of another appliance such as water
heater.
8.
Accessibility clearances take precedence over fire
protection clearances. An 18-inch clearance should be
maintained on any side where passage is required to
access another side for cleaning, servicing, inspection
or replacement of any part that may need attention. An
18-inch clearance is recommended on the control side
for servicing.
9.
Locate equipment which allows the facilities for
ventilation satisfactory combustion of gas, proper
venting, and maintenance of ambient temperature at
safe limits under normal conditions of use. Equipment
shall be located so as not to interfere with proper
circulation of air. When normal infiltration does
not provide the necessary air, outside air shall be
introduced (See “Fresh Air for Combustion”).
10.
Keep air passages free of obstructions. Ventilation
and combustion air must enter boiler room without
restrictions.
WARNING
Fire hazard. Shall not install boiler on combustible
flooring or carpeting. Failure to follow these
instructions could result in death or serious injury.
!
11.
FOR INSTALLATION ON NON-COMBUSTIBLE
FLOORS ONLY -
For installation on combustible
flooring special base must be used. (See Replacement
Parts Section.)
Do Not install Boiler on carpeting.
NOTE: Greater clearances for access should supersede fire
protection clearances.
* Definition of Alcove is three sided space with no wall in
front of boiler. ANSI standard for alcove is 18 inches from
front of appliance to leading edge of side walls as shown
below.
Minimum Clearances to Combustible
Construction
(as seen from above)
7"
6"
BOILER
18"
6"
Front
Control
Side
WARNING
Improper installation, adjustment, alteration, service
or maintenance could result in death or serious
injury.
!
Summary of Contents for WPSB SERIES II
Page 27: ...NOTES...