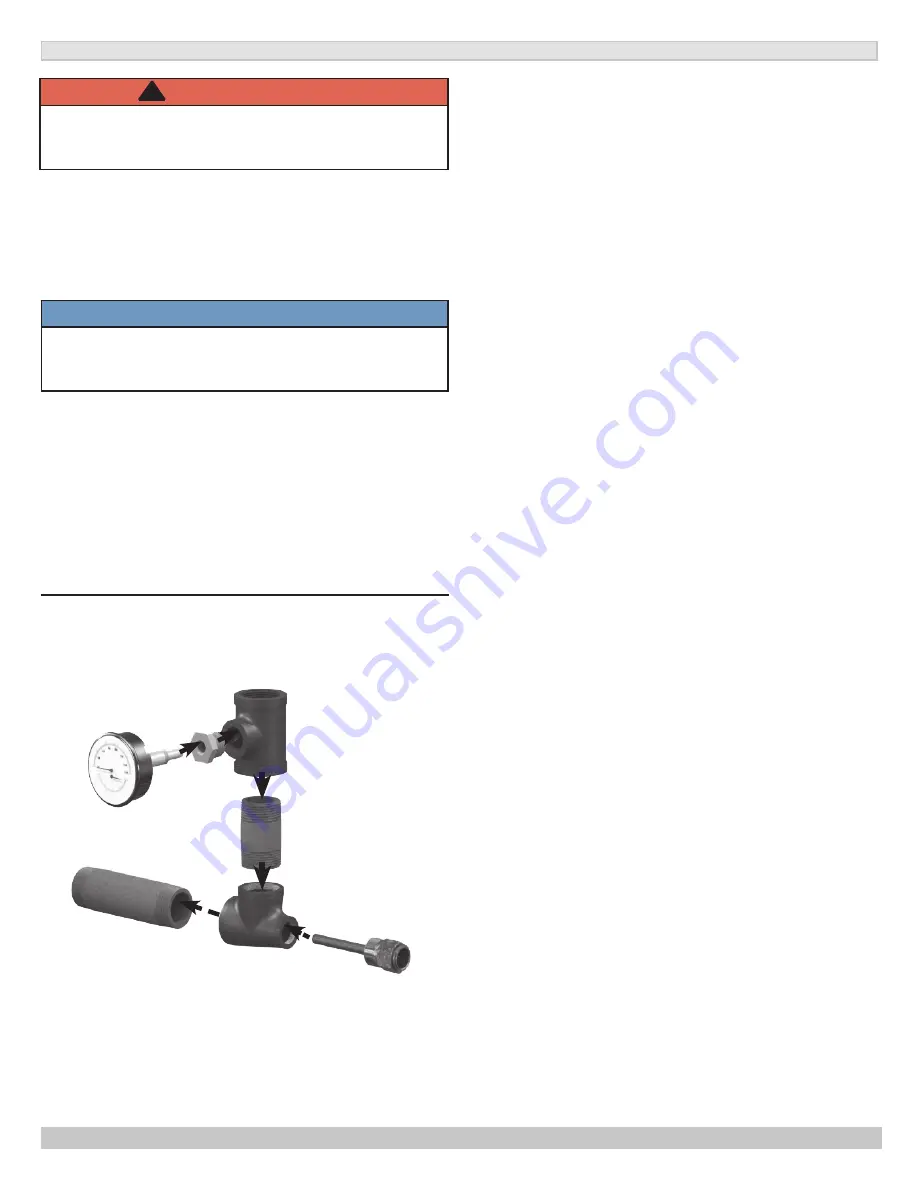
8
CONNECTING SUPPLY AND RETURN PIPING
WARNING
Burn and scald hazard. Safety relief valve could
discharge steam or hot water during operation.
Install discharge piping per these instructions.
!
Figure 2 - Temperature Pressure Gauge
1.
Install discharge piping from safety relief valve. See
Warning, Page 7.
2.
Install temperature pressure gauge.
• Apply pipe sealant to threads on shaft of gauge.
• Thread gauge into supply water tee. See Figure 2.
NOTICE
Do not tighten gauge by hand. Gauge should be
tightened using crescent wrench or 9/16” open end
wrench. See Figure 2.
3.
Connect supply and return lines to boiler. Connections
may require additional fittings and parts, as shown on
diagrams.
4.
Boiler is equipped with 1
1/4” supply and return
connections on both left and right sides of boiler.
Verify clean water supply is available to water inlet valve.
Install sand strainer when water supply is from a well or
pump.
Install hot water boiler above radiation level or as
required by Authority having jurisdiction install low water
cutoff device at time of installation. Periodic inspection
is necessary, as is flushing of float type devices, per
manufacturers specific instruction.
FOR USE WITH COOLING UNITS
A. Boiler used in connection with refrigeration system,
must be installed so that chilled medium is piped in
parallel with heating boiler. Appropriate valves must be
used to prevent chilled medium from entering heating
boiler. See Figure 4 page 9.
B. Boiler connected to heating coils located in air handling
units where they may be exposed to refrigerated air
circulation, piping system shall be equipped with flow
control valves or other automatic means to prevent
gravity circulation of boiler water during cooling cycle.
LOW WATER TEMPERATURE AND LARGE WATER
CONTENT SYSTEM (
See Figures 5 and 6, Page 10.)
Significant condensation may form in boiler and/or
venting system if boiler is operated for long period of
time with return temperatures of less than 120
° F.
Condensate is corrosive and can cause severe
damage to boiler and venting system. Minimum
design return water temperature to prevent
condensation in boiler and venting is 120°F.
Minimum high limit setting is 140°F.
1.
Boiler used in heating system where design water
temperatures below 140°F are desired (e.g. radiant
floor heating), 4-way mixing valve or suitable
alternative is required to prevent low temperature low
return water from entering boiler. Follow mixing valve
manufacturer’s instructions.
2.
Boiler connected to system having large water content
(such as former gravity system), install system bypass.
See Figures 5 and 6, page 10.
3.
Boiler water reset control is used to operate boiler,
minimum reset supply water temperature setpoint
must be at least 140°F, unless mixing valve is used as
in (1) above.
Summary of Contents for WPSB SERIES II
Page 27: ...NOTES...