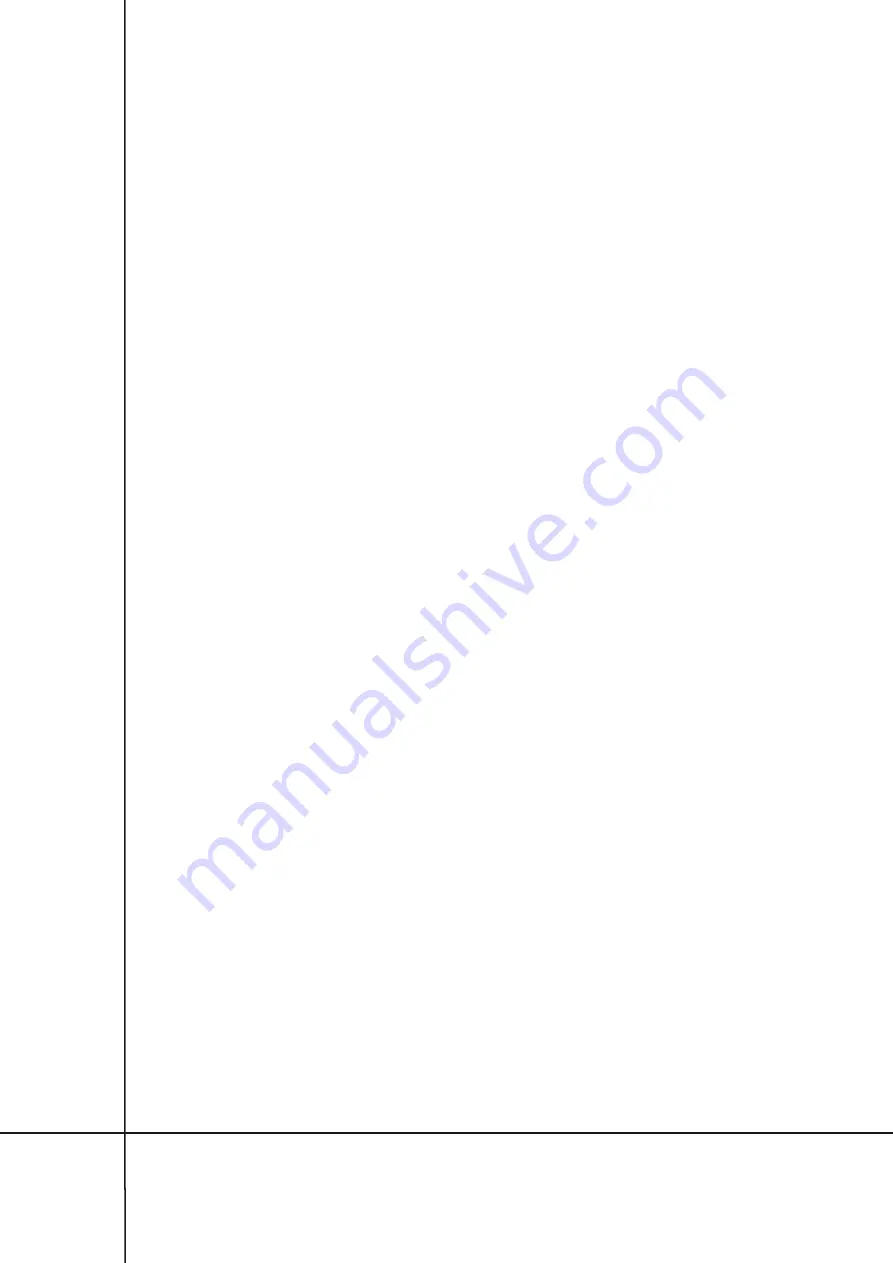
6. Acceptance tests
6.1. General remarks
After installing the controller and all cooperating devices, especially the safety devices, final tests
should be made to check the entire automation. These tests should be performed by competent personnel who
are aware of the risks involved! Final tests are the most important phase in the implementation of automation.
Individual components such as motors, photocells, etc. may require specific checks and therefore it is
recommended to follow the checking procedures in the manuals for the relevant components.
- if the actuators contain internal limit switches which interrupt the circuit, make sure that at this stage they will
not disconnect the actuator at unexpected moment.
- in case of resignation from the installation of manual control buttons, remember to bridge the
'STOP'
terminals. The lack of a bridge will prevent any movement of the actuators.
6.2. Final tests include the following steps
6.2.1. Direction control
Check whether the automation is physically moving in the opening direction when the OPENING
function is activated. In a situation when the movement is in the direction of closing, or there is no
movement, disconnect the controller power supply and check the connection of the appropriate actuator
cables to the appropriate terminals. Check again. Once the controller is powered up, the first move will be
to open.
6.2.2. Programming the controller
Set all the required parameters of the controller operation, such as closing and opening times of
the actuators, possible slowing down phases, and pulling forces of the actuators.
6.2.3. Safety devices control
If photocells are installed, the OP photocells must be manually violated, the OP LED should go
out on the control board. Do the same for the CL photocell and OP / CL, if fitted. In the rest state, when the
optical barriers are not violated, the OP, CL, OP / CL diodes should be on. If it is not, it means an error in
the operation of the photocells (incorrect connection, not synchronizing the transmitter with the receiver
or photocell failure).
6.2.4. Checking the functions controlling the movement of the actuator
Check the A, B, C and STOP functions by using the button on the remote control or the manual
button. After successive impulses from the button, the actuators movement sequence should be
performed in accordance with the settings.
6.2.5. Force setting
Usually, it is not necessary to operate the actuators with the rated power, it should be adjusted
individually to the installation conditions, e.g. by means of the autolearning function (taking into account
the weight and structure of the gate leaves, resistance, exposure to strong wind, etc.). Particular attention
should be paid to the stresses arising after closing or opening the gate leaves, and to anticipate the
consequences of accidental jamming of an obstacle between the gate leaves. It should be remembered
that the lower the parameter value, the smaller the forces will be on any obstacle appearing in the gate's
path. When setting the operating power of the actuators, one should be aware of the resistance of the
gate leaves, as well as their instability in time (the influence of weather conditions, wear of the mechanical
elements, etc.), therefore the set operating power cannot be too low, it must ensure safe guiding of the
leaf throughout the entire range of movement of the gate. If necessary, the force increase function can be
used, adjustable from 0-50% of the value set for the actuators.
14