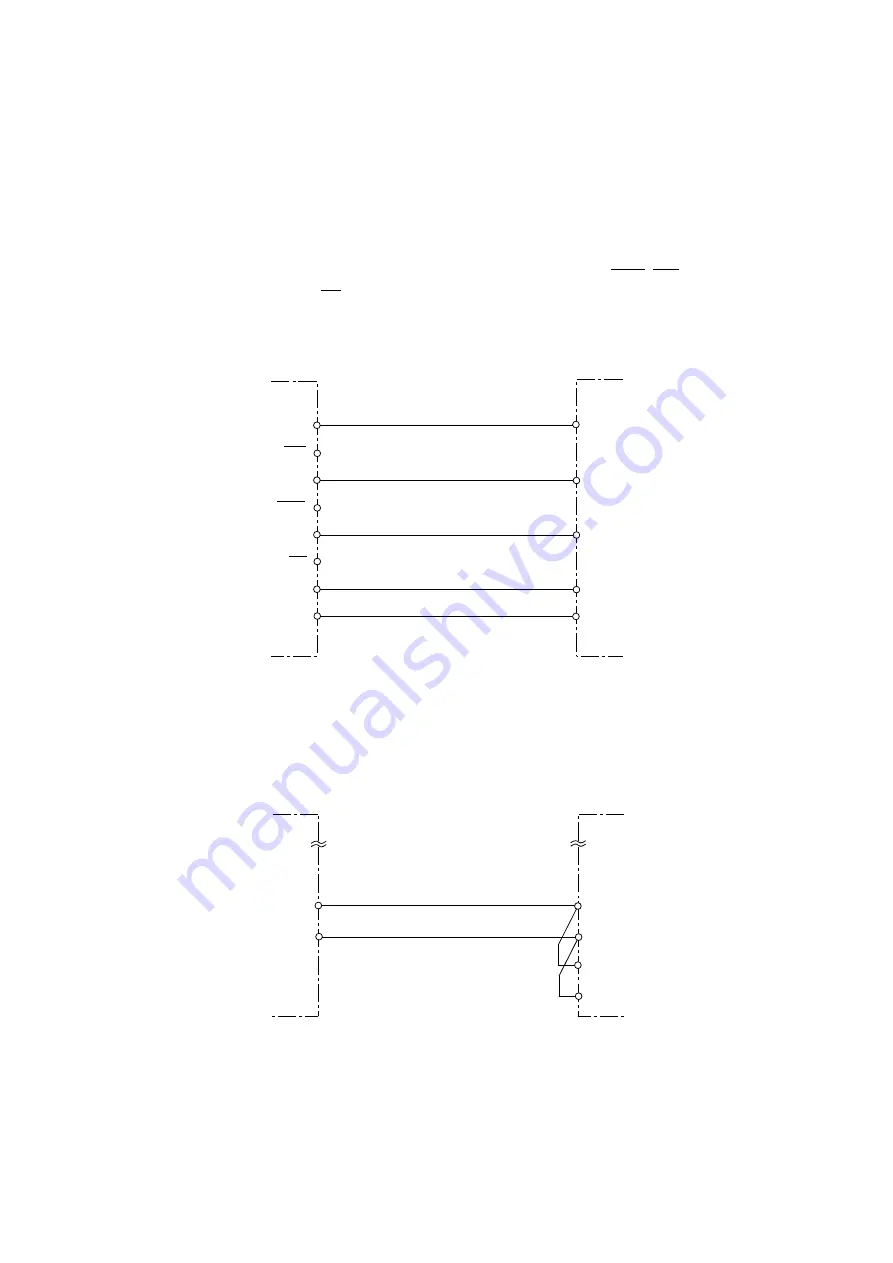
Signal Connection to External Devices
▲
■■■■■■■■■■■■■■■■■■■■■■■■■■■■■■■■■■■■■■■■■■■■■■■■■■■■■■■■■■■■■■■■■■■■■■■■■■■■
DS1104 Hardware Installation and Configuration March 2004
I
■■■■■■■■■■■■■
▼
134
■■■■■■■■■■■■■■■
▼
Encoder providing
single-ended TTL mode
If the single ended TTL mode is used, the inverted pins PHI90, PHI0
and IDX must be left unconnected (see below).
Encoder providing
SENSE lines
If your encoder has sense lines, connect SENSE+ to Vsupply and
SENSE– to GND. Connect the sense lines directly within the connector
of the encoder (see below).
GND
Incremental encoder
output
DS1104
GND
PHI0
PHI0
PHI90
IDX
IDX
PHI90
VSupply
VCC
PHI0
PHI90
IDX
Incremental encoder
output
DS1104
GND
VSupply
SENSE +
SENSE -
GND
VCC
Summary of Contents for CLP1104
Page 6: ...Contents DS1104 Hardware Installation and Configuration March 2004 I 6 ...
Page 20: ...Safety Precautions DS1104 Hardware Installation and Configuration March 2004 I 20 ...
Page 118: ...Mapping of I O Signals DS1104 Hardware Installation and Configuration March 2004 I 118 ...
Page 162: ...Data Sheets DS1104 Hardware Installation and Configuration March 2004 I 162 ...