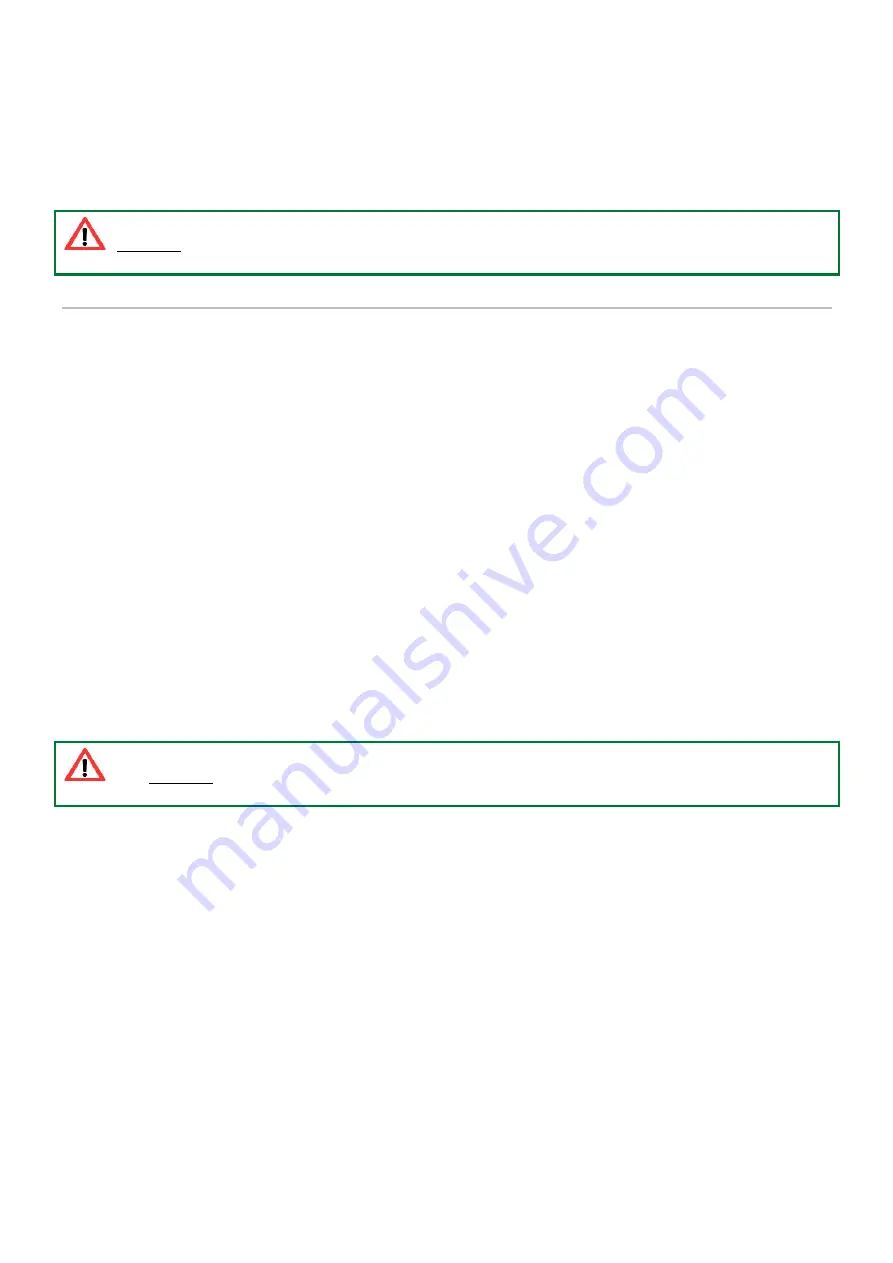
9
6.5.
INSTALLATION OF PUMPING UNITS / PLUGS
The pumping units are not included in the pump and must be selected and purchased separately. The plugs are included in
the pump and already mounted in the pumping holes.
To mount the pumping units, proceed as indicated below:
Identify the most correct position, distributing them evenly on the holes.
Remove the plugs from the holes using a 16-mm fixed wrench or a 6 mm Allen wrench for Multi-line systems and 12
mm Allen wrench for progressive systems.
Screw in the pumping units and tighten to a torque of 12Nm (Multi-line) and 20 Nm (Progressive) using a 16 mm
(Multi-line) and 27 mm (Progressive) fixed wrench.
WARNING: Introduce the pumping unit into the pre-established output, taking particular care for correct
engagement in the threading.
7.
INSTRUCTIONS FOR USE
7.1.
OPERATIONS TO CARRY OUT BEFORE START-UP
The unit can be started up only by specialized personnel.
Using the pump submerged in fluids or in particularly aggressive or explosive/flammable elements is prohibited unless it
has been prepared ahead of time by the supplier for this purpose.
Use gloves and eye protection as required by the lubricant safety data sheet.
DO NOT use lubricants that are aggressive to NBR gaskets. If you are unsure, contact the Dropsa S.p.A. technical office
for a detailed list of recommended lubricants.
Never ignore health hazards and follow sanitary regulations.
Always use suitable piping for the operating pressure.
Check the integrity of the pump.
Check the lubricant level in the tank (min/max indication on the tank). If the level is low, proceed as described in section
7.2.1. Filling the tank.
Ensure that the pump operates at the operating temperature and that the piping is free of any air bubbles.
Check for proper connection of the electrical devices.
To determine the maximum operating pressure, you must know the pressure drop for the piping connected to the pumping
units based on the length, operating temperature and type of lubricant.
Based on these variables for correct distribution to the point, you must always ensure that the piping pressure loss, summed
with the pressure required on the point to be lubricated, is not higher than the maximum potential pressure at the pump
delivery.
7.2.
LOADING LUBRICANT
Ensure that all the pumping unit / plug lodging holes have been occupied.
WARNING: In order to prevent any malfunctions and voiding of the warranty, we recommend topping up the
lubricant without impurities exclusively from the dedicated loading system.
7.2.1.
FILLING THE TANK (FOLLOWER PLATE VERSION)
The feeder is filled using a dedicated device complete with a filter. In case it is necessary to perform the initial filling (with the
pump completely empty and no remaining grease from the previous load), the pump must be positioned vertically to remove
the air in the tank until the vent point corresponding to the red maximum level indicator is reached (the lubricant is supplied
from the base). To speed up the air bleeding operation, we recommend pressing the indicator until all the air is evacuated,
releasing it at the same time as interrupting the filling of the tank. Subsequently, filling can be performed based on different
guidelines, checking that the maximum level line is not exceeded. If the line is exceeded, lifting of the maximum level will be
indicated
up to a maximum of 10mm (0.39”). After that, if filling is not interrupted, a leakage of lubricant will be noticed from
the central part of the follower plate (air vent). This will not cause a problem or malfunctioning, but grease may leak from the
drain hole of the tank if there is an excessive amount.