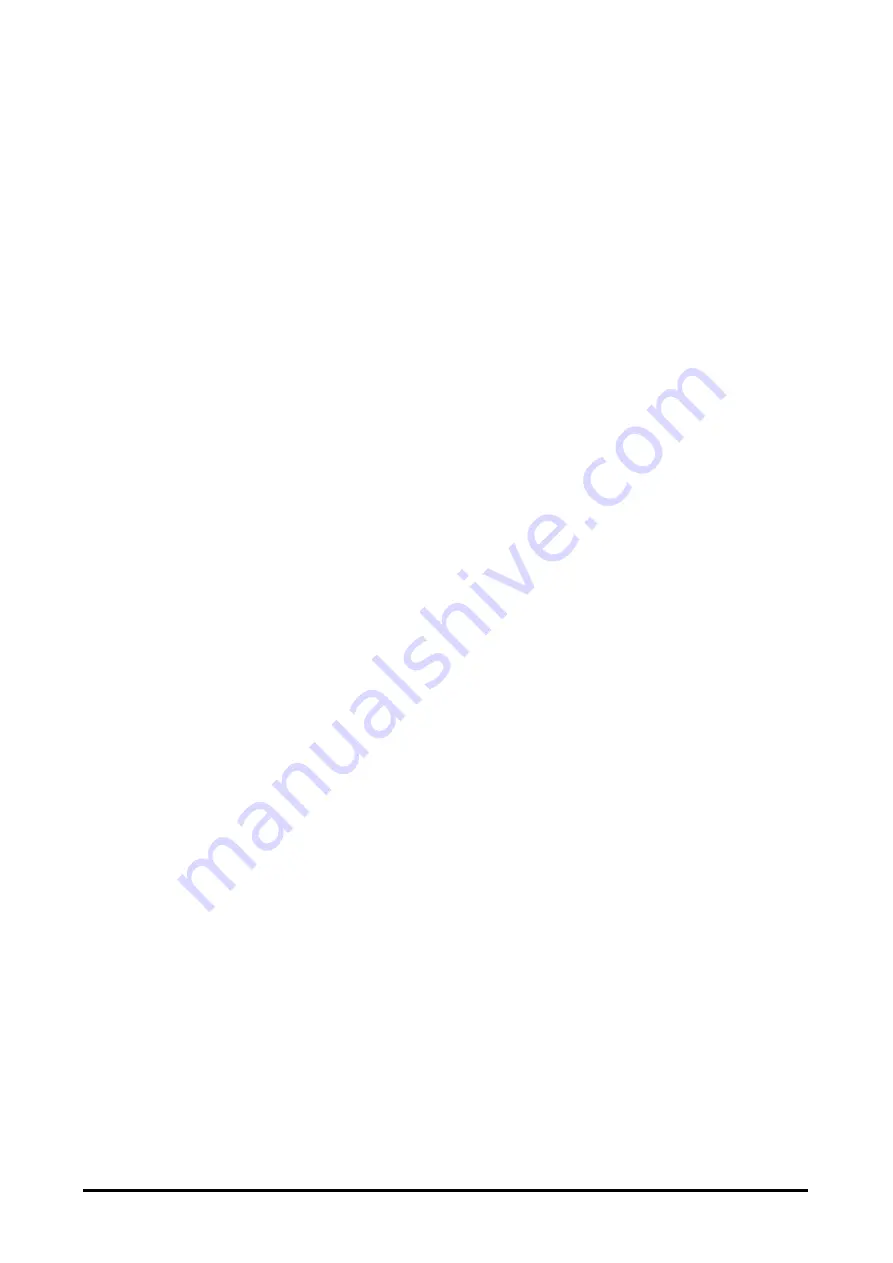
43
MicroController Control System
Testing And Adjusting
3.
Charge the battery correctly. A battery should be
discharged to 80% of its capacity then fully
recharged. It should cool four to eight hours to
allow the voltage to stabilize before being put
back in use. The battery should have an equalizing
charge (an extra three or four hour charge at a low
finish rate) once a month to make sure all cells are
in a fully charged condition. Properly charged
batteries should be identified to prevent low
batteries from being installed in trucks.
4.
Operation with a low battery must be prevented.
Low battery operation may damage the battery
and will cause higher than normal current in the
electrical system. High current draw due to a low
battery will damage contactor tips and shorten
motor brush life.
5.
The battery's maximum temperature is critical.
The electrolyte temperature should never exceed
43°C (110˚F) either while operating or charging.
Overcharging a battery will cause over heating
and warp the battery plates. Maximum battery life
will result from maintaining 25˚C (77˚F) electrolyte
temperature. Most of the charging equipment is
fully automatic but should be checked periodically
to assure proper working order.
6.
Keep accurate battery records. Regular battery
readings should be taken with a battery tester or
voltmeter and a written record kept. Specific
gravity and voltage of each cell should be
checked and recorded at least once each month.
This inspection should be made after an equalizing
charge. Readings should never be taken directly
after water has been added. Records of all battery
maintenance should be made and filed so it will be
known which batteries are being abused or
wearing out.
Repairs should be made immediately otherwise
the battery may become damaged. Batteries
stored in a discharged condition may be difficult to
recharge due to sulfate formation.
Visual Checks
1.
Verify all components and wires are in their proper
place. Check fuses, components, contactor tips,
wires and connections. Verify that they are not
burned, broken or loose.
2.
Verify there is no mechanical binding or
interference in the contactor.
3.
Visually check the parking brake switch, the
hydraulic switches and accelerator linkage for
adjustment or interference problems.
Resistance to Chassis Checks
Resistance between any point in the truck wiring
and the chassis should be a minimum of 10,000
ohms or more.
Many malfunctions are caused by shorts to chassis.
Usually, two shorts must exist before a malfunction
will occur. But, since batteries can have chassis
leakage, only one short to chassis in the truck wiring
can cause problems. To prevent problems because of
shorts, do the following:
1.
Disconnect the battery and discharge the HEAD
CAP.
2.
Randomly measure any component connection or
wiring connection in respect to the lift truck chassis
for a minimum resistance of 10,000 ohms. Any test
point with low resistance must have the short to
chassis removed.
3.
Always keep batteries clean to minimize current
leakage to the chassis.
4.
Routinely clean the brush dust from the motors.
5.
Be sure that all attachments, such as horns and
lights are designed for no chassis connection (a
two wire system).
Removal of Shorts to Chassis
When a short is found, it must be cleared even if the
machine has normal operation. It is necessary to
narrow the field of possible problem areas before
inspection of individual wires and components.
When a low resistance circuit is located, it should be
opened at various points. This will permit the
shorted wire or component to be pin-pointed for
repair or replacement.
Summary of Contents for B20S-3
Page 3: ......