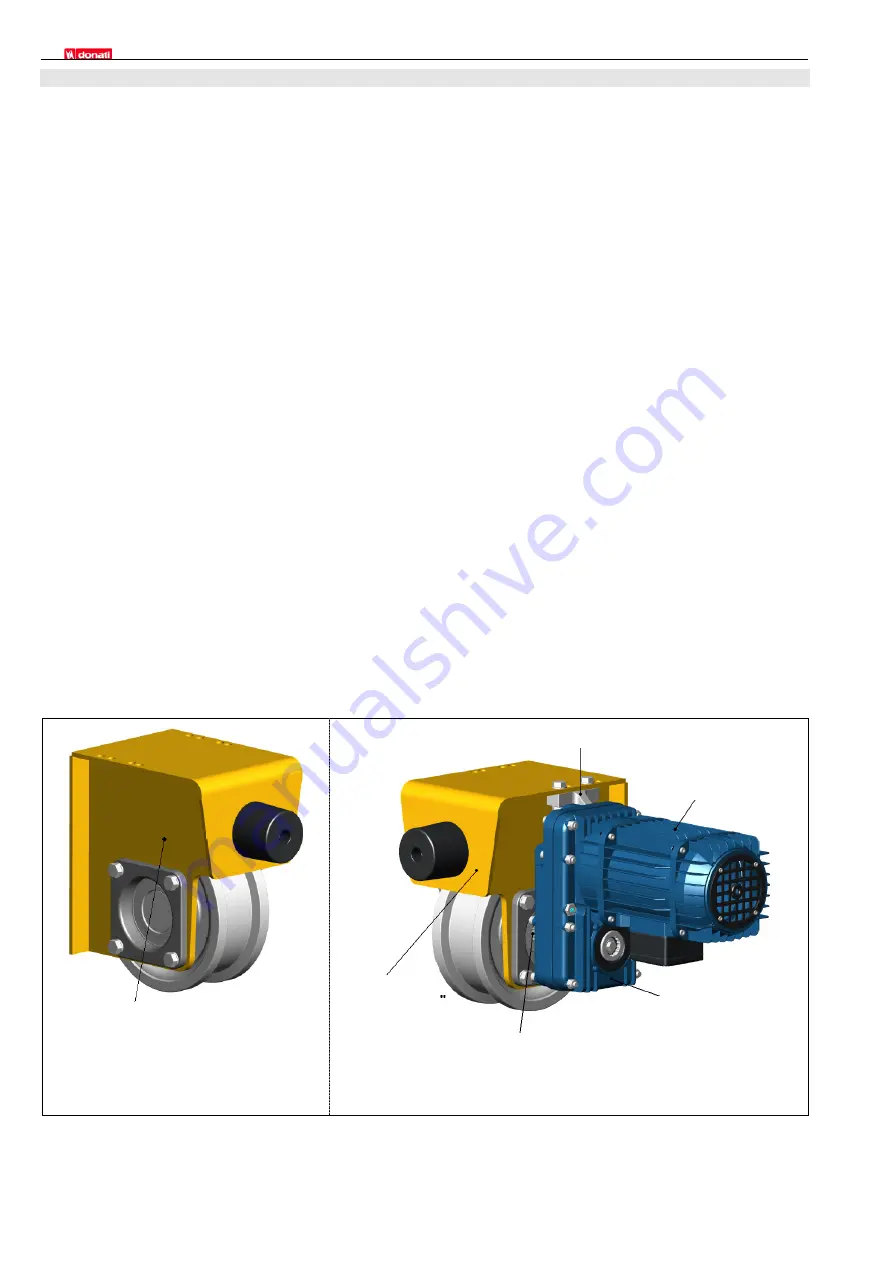
DONATI SOLLEVAMENTI S.r.l. - Via Quasimodo,17 - 20025 Legnano (MI) - Tel. 0331 14811 - E: [email protected]
8
2.1.3 Components on Drive Units
•
“DGT” series wheel groups:
The drive wheels
Ø 125, Ø 160, Ø 200, Ø 250 and Ø 315 are carbon steel moulded. The wheels Ø 400 and Ø 400
R are cast-iron.
•
All wheels revolve on radial bearings, permanently lubricated, with the exception of the larger capacity Ø
400 R wheel, which is fitted with roller bearings.
•
They are available in either neutral (idle) operation or ready to be set up as drive units in combination with a
offset geared motors.
•
In drive operation, the direct coaxial connection between the oscillating reducer’s exit shaft and the slotted
hub on the drive wheel ensures high safety standards and operating reliability.
•
Wheels are available in a standard version with a double flange, and can be supplied, on request, in various
sliding band widths in relation to the type of traversing rail they are intended to slide on.
•
Whether in idle or drive operation, the wheels are supported and contained within an electro-welded plated
frame which acts as a support box for the entire group, and as an joining element between the operating
head frame or trolley with which the wheel group is to be assembled.
•
“DGP” series offset geared motors:
Reducers
are designed as a “offset” type with a concave shaft, featuring parallel axes with two or three stages of
reduction, and permanent oil-bath lubrication.
•
Engineered with cylindrical high resistance steel gears, featuring spiral toothing, thermically treated, entirely
supported on ball bearings.
•
Sized to resist a lifetime of stress and wear, in accordance to the pertinent ISO service group.
•
The connection between the reducer and sliding wheel is guaranteed by a slotted shaft connecting the holes
on both parts, while the reducer fastened to the wheel group makes use of a system comprising a reaction
arm fastened to the wheel group, and an elastic counter bearing with rubber buffers and a setscrew. The
entire reducer-wheel connection system guarantees both high quality sliding operation and maximum
duration over time with low maintenance, thanks to the elimination of rigid connections.
The electric motors
are asynchronous, featuring a progressive start-up, with standard ventilation, self-braking with
axial shifting of the rotor guaranteeing a fast, reliable mechanical braking over time.
•
Conical brakes are fitted with asbestos-free braking gaskets, featuring an extended braking surface.
•
The brake block comprises a fan which ensures proper cooling for the brake and motor, shifting axially with
the motor shaft; the brake function is activated automatically in the case of a power outage.
•
The connection between the motor and swinging reducer features a slotted joint contained within a coupling
housing, which also comprises, where required, a flywheel transferring progressive start-up and braking
drive motion.
Idle Drive Unit
fig. 1a
Powered Drive Unit
fig. 1b
“DGT” idle wheel group
Reaction arm
Self-braking motor
“DGT” drive
wheel group
“DGT” oscillating reducer
Wheel gear motor connecting slotted shaft