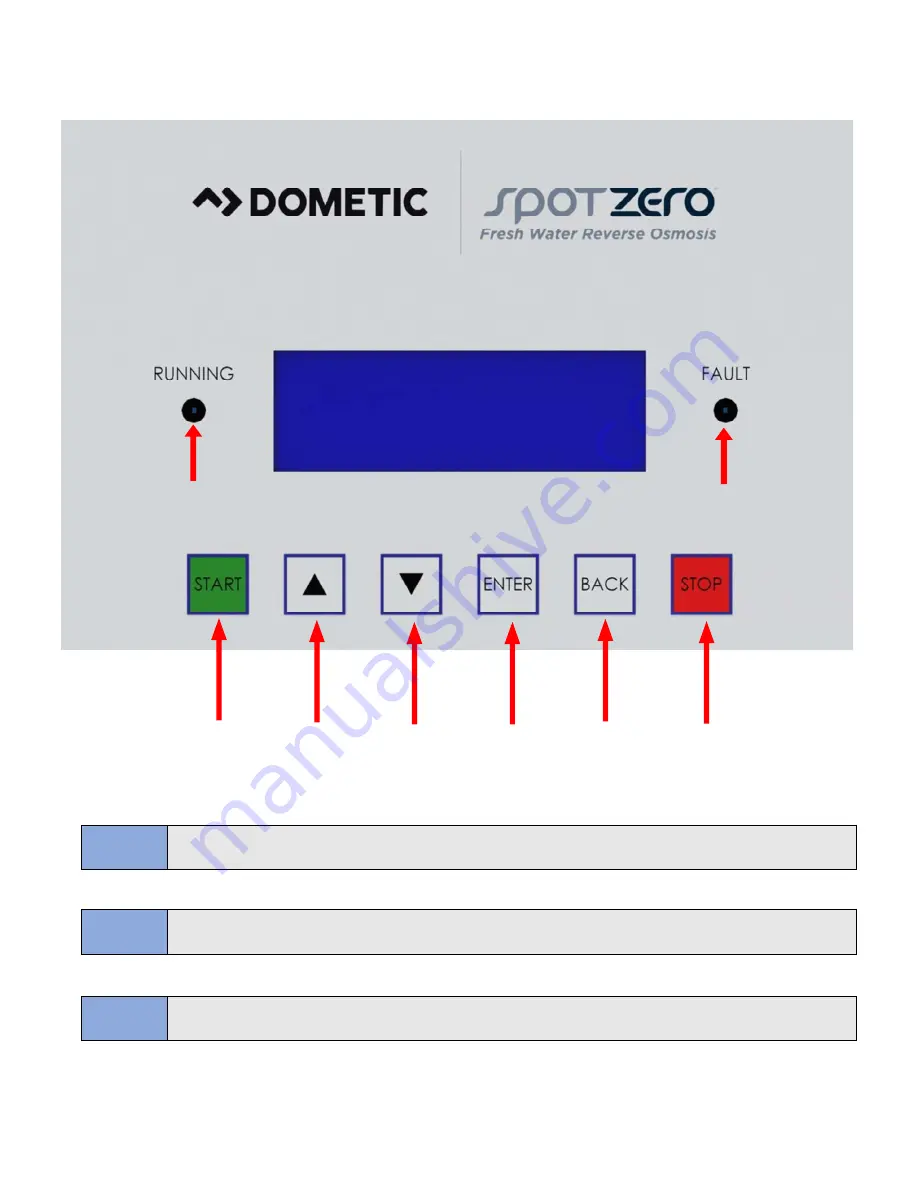
LCD Touchpad Navigation
NOTE
START Button NOT REQUIRED for standard system operation. System will turn on when
sufficient feed flow recognized.
NOTE
Pressing START will resume normal operation of the system if the stop button has been
pressed and there is sufficient feed flow.
NOTE
Pressing STOP button will halt all system operation until power is cycled to the unit or the
START button is pressed when proper feed flow is present.
LED light will illuminate
blue when running
LED light will illuminate
red when there is a
system fault
Move Cursor
or Selection
Up
Move Cursor
or Selection
Down
Confirm
Selection or
Change
Return to
Previous
Screen
Stop System
Operation
Start System
Operation
34
Summary of Contents for SPOTZERO SZIII 2000
Page 1: ...USER MANUAL INSTALLATION GUIDE SZIII 2000 3000 www spotzerowater com ...
Page 4: ... Introduction 4 ...
Page 8: ...Installation and Commissioning 8 ...
Page 13: ...13 ...
Page 17: ...Membrane Return Membrane Product assemblies Membrane Assembly 17 ...
Page 18: ...Operation and Maintenance 18 ...
Page 35: ...35 ...
Page 42: ...Troubleshooting 42 ...
Page 46: ...SZIII System Specification and Parts 46 ...
Page 47: ...47 ...
Page 48: ...48 ...
Page 49: ...49 ...
Page 50: ...50 ...
Page 51: ...51 ...
Page 52: ...52 ...
Page 53: ...53 ...
Page 54: ...54 ...
Page 55: ...Warranty 55 ...