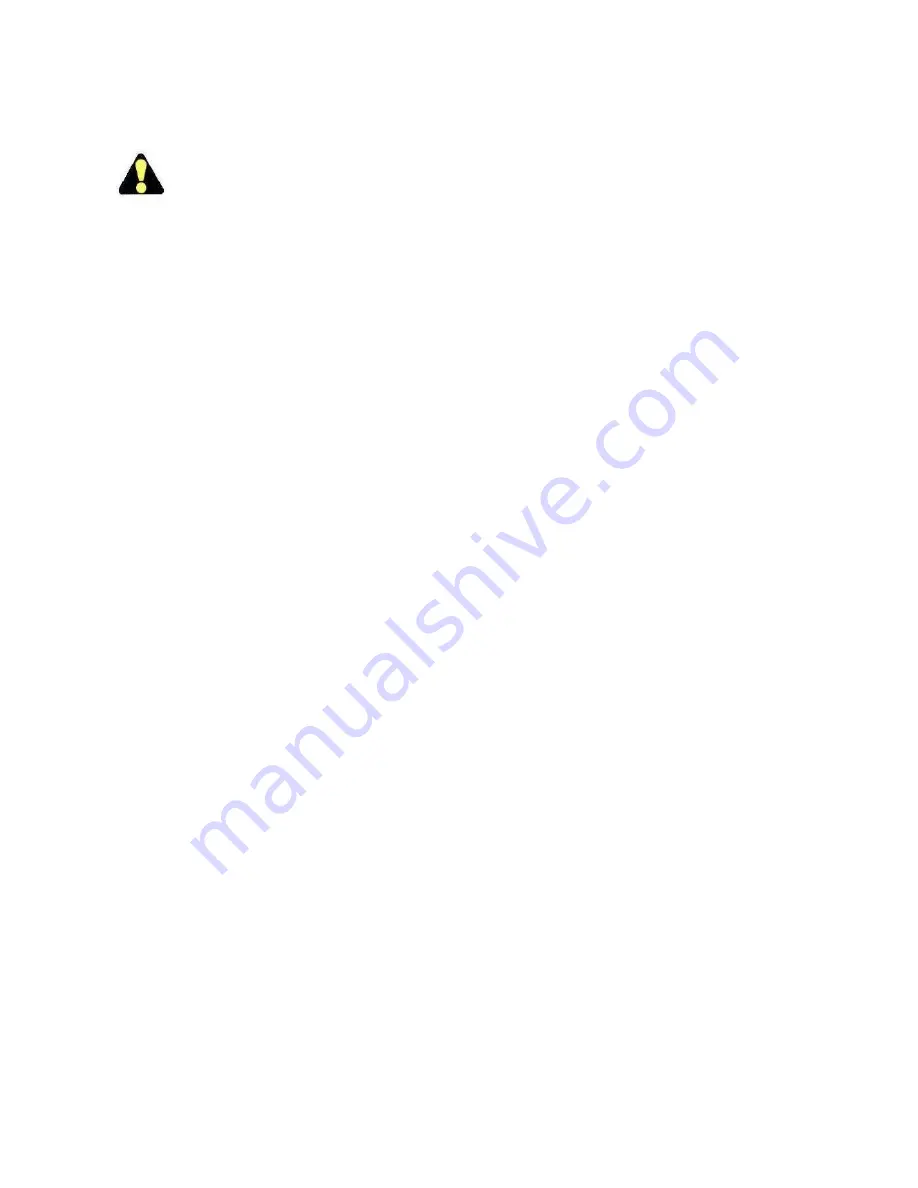
38
TROUBLE SHOOTING
Repair and adjustment procedures should
be made only by experienced maintenance
personnel, or by a DoALL service
representative. Reference to the machine’s electrical
and hydraulic schematics will be helpful.
ERROR MESSAGES
Follow the prompts when an error message appears.
MACHINE WILL NOT START
1.
Check that the disconnect switch is in the ON
position.
2.
The Emergency Stop button needs to be reset
(rotate the button head clockwise).
3.
See if the main fuses and/or circuit breakers have
tripped or burned out.
4.
Make sure both band wheel doors are closed and
the interlock switches are engaged.
5.
Check the splash screen in front of the machine to
be in position and the interlock switch is engaged.
6.
Push the motor start overload reset buttons in the
electrical cabinet. If overload tripping occurs,
locate and correct the problem.
7.
Check the control transformer for power.
8.
Check the hydraulic motor and wiring.
9.
Check the starter, relay coils and contacts for
faulty operation.
10.
Have an electrical service person check the
continuity of the starting circuit.
MACHINE STARTS, BUT WON’T CONTINUE RUNNING
1.
The saw band is broken or too long and is
activating the band break proximity switch.
2.
Check the splash screen in front of the machine to
be in position.
3.
Check to see if the band wheel doors are closed
(the band drive motor will not start unless both
wheel doors are closed).
4.
The saw head has not cleared the head down limit
switch. Push the saw head up button and start the
hydraulic pump.
5.
The out‐of‐stock sensor has been activated.
SAW BAND STALLS DURING A CUT
1.
Decrease saw head feeding pressure.
2.
Check to see if drive belt tension is adequate to
resist “cogging” underload.
3.
Use a Tensigage to check for proper saw band
tension.
4.
Check for proper operation of the band tension
selector.
BLADE TOOTH GULLETS ARE LOADING
1.
Use a coarser pitch saw band.
2.
Increase the band speed setting, or decrease the
feed pressure setting.
3.
Check for improper coolant application.
4.
Check the positioning of the band brush. Replace
the wire brush of necessary.
SAW BAND SQUEAL
1.
The lead‐in/exit rollers are: not contacting the saw
band; (b) positioned too tight against the saw
band.
2.
Check for defective lead‐in/exit roller bearings.
SAW BAND VIBRATION
1.
Check for a dull or damaged saw band.
2.
Incorrect band speed or feed pressure setting is
used.
3.
Check for incorrect saw band pitch
4.
Coolant mixture is weak, or incorrect coolant is
being used.
5.
Stock piece is not being firmly clamped by the vise
jaws.
6.
Check for worn or improper adjusted saw guide
inserts.
7.
Check for a worn saw guide back‐up bearing or
carbide, or lead‐in/exit roller bearing.
8.
Check for incorrect saw band tension.
PREMATURE BLADE TEETH DULLING
1.
Band speed and/or feed rate too high.
2.
Check for faulty stock: heavy scale, inclusions, hard
spots, etc.
3.
Stock analysis is wrong. This can result in incorrect
cutting recommendation.
4.
Coolant is not covering the saw blade properly.
5.
Check for saw band vibration.
6.
Check for chip welding, or a chipped blade tooth
lodged in the cut.
Summary of Contents for C-3028NC Boxed
Page 2: ......
Page 3: ......
Page 11: ...6 MACHINE DIMENSIONS Continued C 3028NC DIMENSIONS...
Page 12: ...7 MACHINE DIMENSIONS Continued C 3028NC Boxed DIMENSIONS...
Page 13: ...8 MACHINE DIMENSIONS Continued C 4033NC DIMENSIONS...
Page 14: ...9 MACHINE DIMENSIONS Continued C 420NC DIMENSIONS...
Page 15: ...10 MACHINE DIMENSIONS Continued C 420NC BOXED DIMENSIONS...
Page 16: ...11 MACHINE DIMENSIONS Continued C 5650NC DIMENSIONS...
Page 17: ...12 MACHINE DIMENSIONS Continued C 560NC DIMENSIONS...
Page 18: ...13 MACHINE DIMENSIONS Continued C 6260NC DIMENSIONS...
Page 19: ...14 MACHINE FEATURES...
Page 39: ...34 LUBRICATION DIAGRAM...