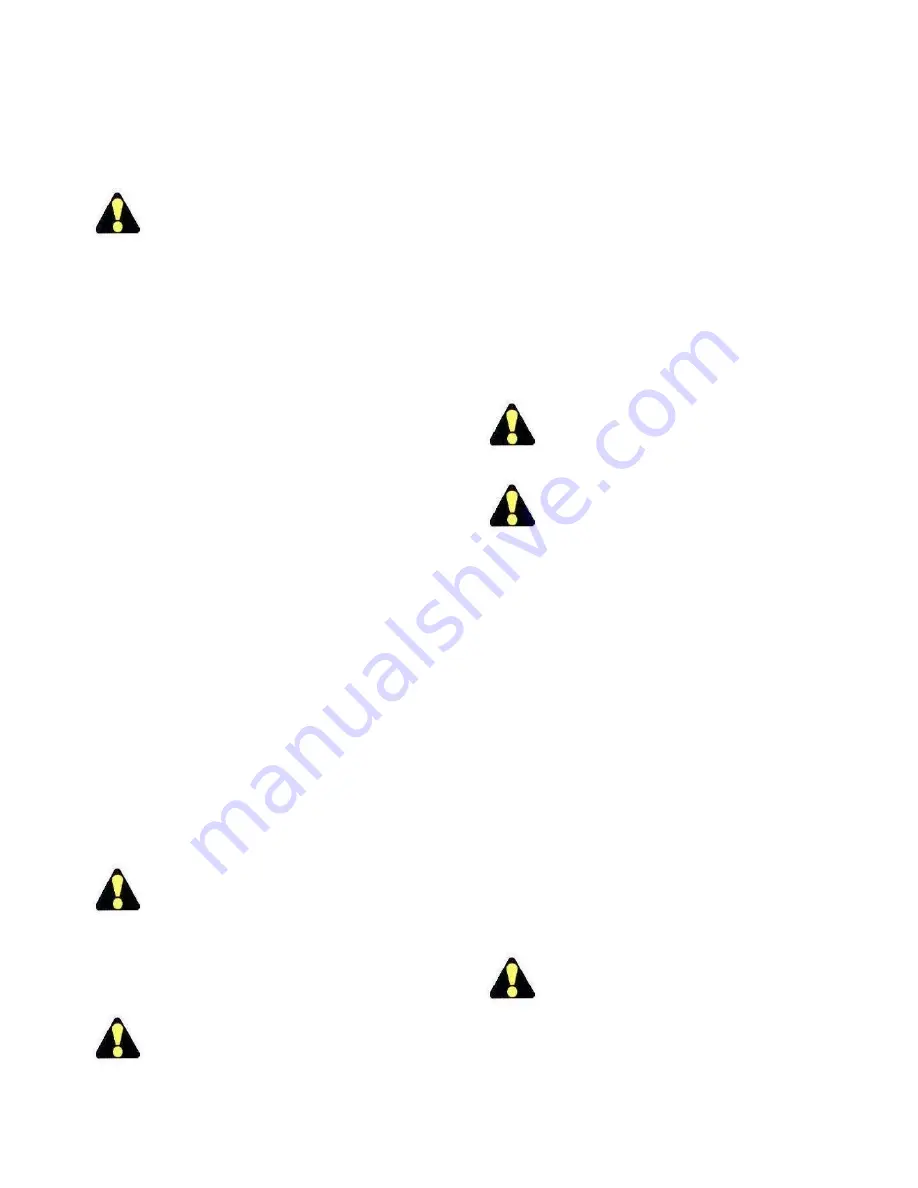
16
CLEANING
1. If necessary, use a mild cleanser to remove
rust preventive coating applied to exposed
bare metal surfaces.
Do not use volatile solvents such as
gasoline or benzene.
FLOOR INSTALLATION
1. Before placing the machine down, install one
leveling screw and nut into each base foot pad.
Then: (a) adjust the leveling screws to extend
approximately 13 mm through the mounting pad;
(b) tighten the jam nuts; (c) just before lowering
to the floor, place a foot pad under each leveling
screw. Now lower the machine in the desired
location.
2. Place a machinist’s level on the bracket in the
front of the vise. Adjust the leveling screws until
the machine is level and weight bears evenly on
all mounting pads.
3. Place the level front to back on the fixed vise
bed and adjust. Again, weight must bear evenly
on all foot pads.
4. Now adjust the leveling screws to make the
front of the machine 0,4 mm lower than the rear.
5. Install anchoring bolts through the base pad
holes (those who have a hole) next to the
leveling screws.
6. Remove the protective shipping bracket
installed between the saw head and the base
frame. Keep this bracket in case machine
needs to move later.
7. Install roller stock conveyor at the rear of the
machine, approximately 1 meter from the
machine. Anchor the conveyor to prevent
moving.
Conveyors are not attached to the
machine and should be anchored
separately.
ELECTRICAL INSTALLATION
Electrical installation must be made by
authorized electrical personnel only.
1. Refer to the machine specification plate on the
saw base to verify that the electrical supply
circuit meets the voltage, phase, frequency and
amperage requirements listed. The basic data
is reproduced on the manual’s introductory
page.
2. The electrical supply to this machine must be a
dedicated circuit.
Electrical Enclosure
1. The main enclosure is combined with the
operator’s control panel on the front of the
machine. Power is connected to this enclosure.
2. The following are important disconnect
precautions:
The disconnect switch must be in the “ON”
position before the machine will operate.
Turning “OFF” the disconnect switch will
shut down the machine.
The enclosure must be closed and the
appropriate securing screws must be in
place before starting the machine
operation.
3. Turn the disconnect switch on the enclosure to
“OFF”. Then: (a) use the keys found in the
toolbox and unlock the enclosure at the left door
edge and open the door; (b) familiarize yourself
with the operation of the disconnect switch
operating handle, door interlock, and switch
drive dog operations.
4. Find the hole for the cable connector under the
transformer. Then: (a) bring the power wiring L1,
L2, L3 and Ground through the connector into
the enclosure.
5. Bring the power cable leads to the terminal strip
at the bottom of the panel. Then: (a) connect L1,
L2 and L3 to their respective terminals; (b)
connect the ground wire to the ground strip.
6. Make sure to place the operating shaft and
operating handle of the disconnect switch in the
“OFF” position. Then: (a) close the door of the
enclosure with the keys; (b) now turn “ON” the
electrical supply and the disconnect switch (no
action will occur until the
Hydraulic Start
button on the control panel has been pushed.
DO NOT start the machine hydraulics until
the following “Preparations for use”
procedures have been performed.
Summary of Contents for C-3028NC Boxed
Page 2: ......
Page 3: ......
Page 11: ...6 MACHINE DIMENSIONS Continued C 3028NC DIMENSIONS...
Page 12: ...7 MACHINE DIMENSIONS Continued C 3028NC Boxed DIMENSIONS...
Page 13: ...8 MACHINE DIMENSIONS Continued C 4033NC DIMENSIONS...
Page 14: ...9 MACHINE DIMENSIONS Continued C 420NC DIMENSIONS...
Page 15: ...10 MACHINE DIMENSIONS Continued C 420NC BOXED DIMENSIONS...
Page 16: ...11 MACHINE DIMENSIONS Continued C 5650NC DIMENSIONS...
Page 17: ...12 MACHINE DIMENSIONS Continued C 560NC DIMENSIONS...
Page 18: ...13 MACHINE DIMENSIONS Continued C 6260NC DIMENSIONS...
Page 19: ...14 MACHINE FEATURES...
Page 39: ...34 LUBRICATION DIAGRAM...