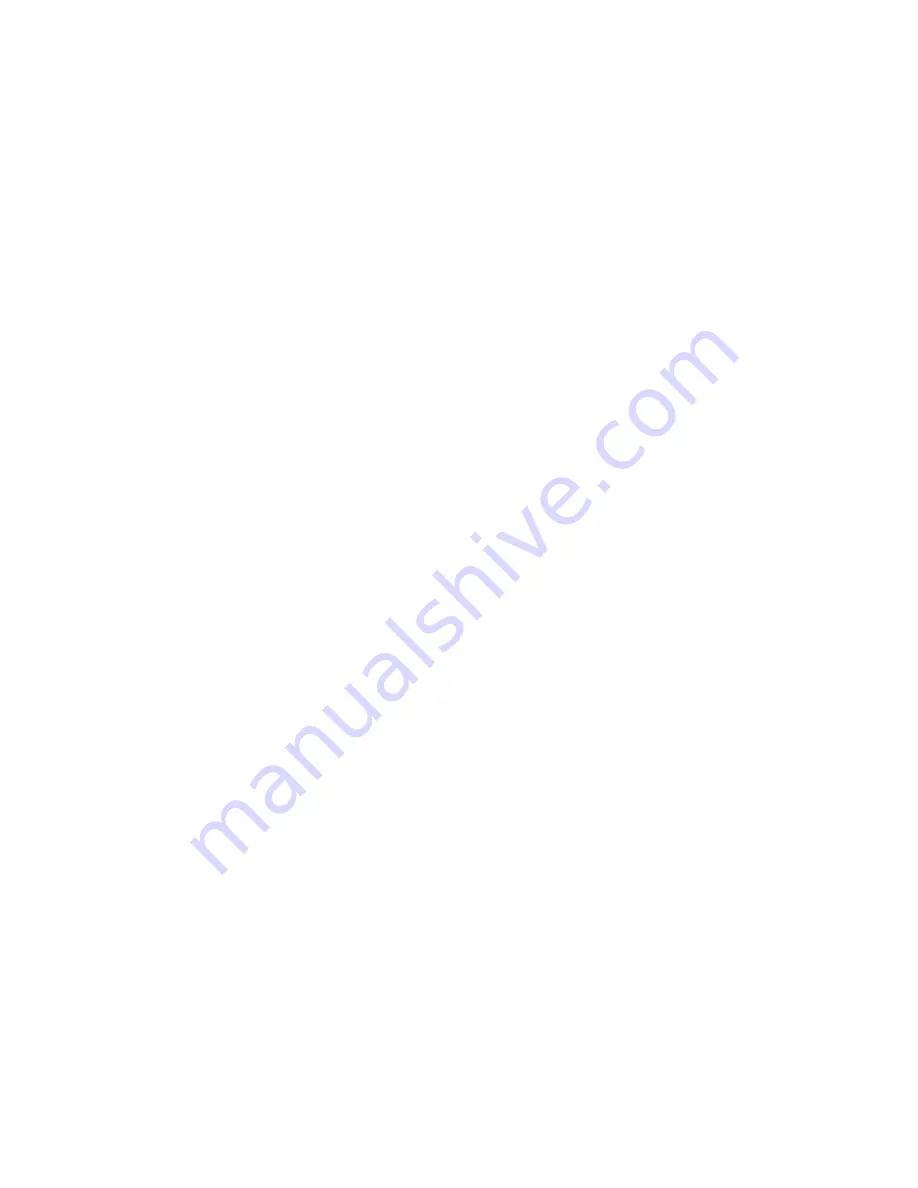
31
NESTING FIXTURE (Continued…)
Controls
1.
Go to the
MODE SELECT
screen.
2.
Under
ESCAPE
, choose how the index vise responds
after one cut is completed.
DO
allow the index vise to move back 2mm
(standard setting) to avoid the saw band from
touching the material as the saw band is raised.
It is designed for bundle cutting.
NONE
keeps the index vise stationary while the
saw band is raised. It is designed for single
cutting.
For best nesting cutting results
1.
Stack the same number of stock pieces in each row.
2.
The stack should always be higher than it is wide.
3.
Increasing the nesting vise clamping pressure will
increase the holding load per piece.
4.
Apply as much coolant as possible while cutting.
5.
Replace wear plates on the movable vise jaw when
they become worn.
6.
Adjust the index table’s vertical guide rollers to
keep the stock from collapsing when the vises are
unclamped.
7.
Generally, reduced band speed and feed force are
necessary when sawing stacked material. This
results in a lower cutting rate than possible when
sawing solid stock.
8.
In some instances, increased production and blade
life may be obtained by nesting fewer pieces than
the maximum capacity permits.
TYPICAL OPERATING PROCEDURES
Preparation
1.
These operation procedures assume that the
machine is prepared as follows: (a) the band drive
motor is OFF; (b) the saw band is properly installed
and tensioned; (c) both band wheel doors are
closed; (d) all guards are in place and/or secured; (e)
the coolant reservoir is full and all lubrication points
are properly serviced and if necessary press the
COOLANT key with the desired delivery mode; (f)
the band brush is properly positioned.
Manual operation
1.
Turn the hydraulics on, rise the saw head and open
both the front and rear vise to accommodate the
material to be cut.
2.
Adjust the vise location pins per the size of the
material to be cut.
3.
Remove or add the fixed vise filler plates per the
size of the material to be cut.
4.
Verify or adjust vise pressure for the type of
material to be cut.
5.
Place material on the index vise bed.
6.
Loosen the saw guide adjustment screws and adjust
left moveable saw guide arm to the size of the
material to be cut. Tighten the saw guide arm and
then tighten the saw guide adjustment screws.
7.
Clamp both front and rear vises.
8.
Check the band brush for correct positioning, verify
that the chip conveyor is operating and choice of
coolant flow has been selected.
9.
Press the BAND CYCLE START button.
10.
Saw head will lower, and cut through the material,
energize head down limit switch, saw head rises
above the material and the blade will shut off.
11.
The operator may adjust band speed, coolant flow,
feed rate and feed force at any time during the
sawing process.
Automatic operation
1.
Start the operation by following steps 1 through 8
from above Manual operation.
2.
If necessary, HOME the indexing vise. After homing,
make sure the index vise is not at the HOME
position. This is done in Manual mode and only
when the front vise is clamped and the rear vise is
opened.
3.
Press the MODE SET on the View screen and enter
data for the JOB, LENGTH, QTY and set blade speed
for the jobs. Double check your data. Make any
changes before starting.
4.
Press F1 to go to the View screen. Select AUTO,
COOLANT AUTO or “I” and choose between CUT
NOT COUNTED or CUT COUNTED.
5.
Press the
green
Band Drive button on the control
panel or the Band “I“ on the Run screen of the
workstation.
6.
The saw head will lower and cut through the
material, energize the head down limit switch, saw
head rises above the material, vise will transfer
material for the next cut, vises will clamp and saw
head will make the next cut.
7.
When all jobs entered have been completed, the
saw band shuts off.
Summary of Contents for C-3028NC Boxed
Page 2: ......
Page 3: ......
Page 11: ...6 MACHINE DIMENSIONS Continued C 3028NC DIMENSIONS...
Page 12: ...7 MACHINE DIMENSIONS Continued C 3028NC Boxed DIMENSIONS...
Page 13: ...8 MACHINE DIMENSIONS Continued C 4033NC DIMENSIONS...
Page 14: ...9 MACHINE DIMENSIONS Continued C 420NC DIMENSIONS...
Page 15: ...10 MACHINE DIMENSIONS Continued C 420NC BOXED DIMENSIONS...
Page 16: ...11 MACHINE DIMENSIONS Continued C 5650NC DIMENSIONS...
Page 17: ...12 MACHINE DIMENSIONS Continued C 560NC DIMENSIONS...
Page 18: ...13 MACHINE DIMENSIONS Continued C 6260NC DIMENSIONS...
Page 19: ...14 MACHINE FEATURES...
Page 39: ...34 LUBRICATION DIAGRAM...