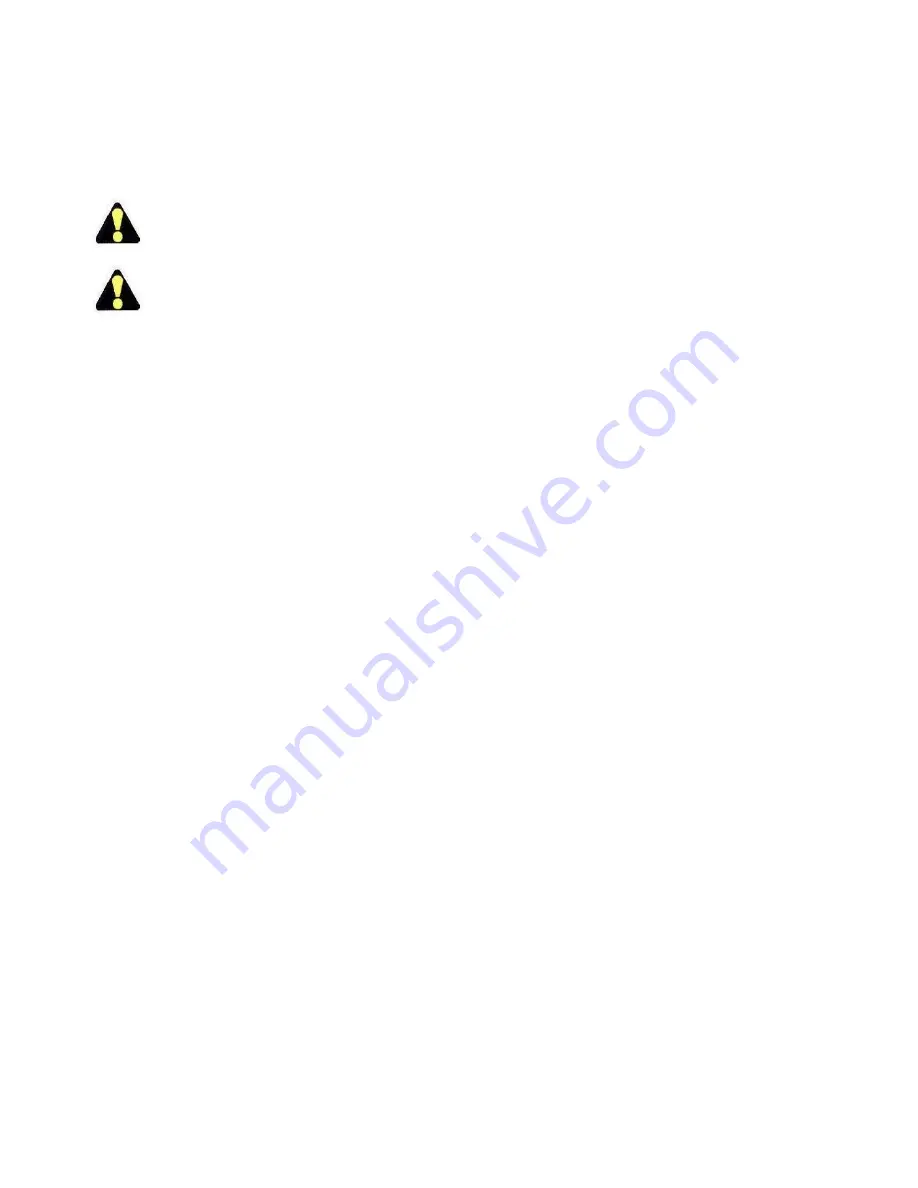
32
TYPICAL OPERATING PROCEDURES (Continued….)
8.
The operator may adjust band speed, coolant flow,
feed rate and feed force at any time during the
sawing process.
DO NOT remove any cut‐off parts until they are
away from the saw band or the saw band must
be stopped completely.
For future reference, keep a record of band
speed, feed rate, feed force, coolant and saw
band application for successful jobs.
Summary of Contents for C-3028NC Boxed
Page 2: ......
Page 3: ......
Page 11: ...6 MACHINE DIMENSIONS Continued C 3028NC DIMENSIONS...
Page 12: ...7 MACHINE DIMENSIONS Continued C 3028NC Boxed DIMENSIONS...
Page 13: ...8 MACHINE DIMENSIONS Continued C 4033NC DIMENSIONS...
Page 14: ...9 MACHINE DIMENSIONS Continued C 420NC DIMENSIONS...
Page 15: ...10 MACHINE DIMENSIONS Continued C 420NC BOXED DIMENSIONS...
Page 16: ...11 MACHINE DIMENSIONS Continued C 5650NC DIMENSIONS...
Page 17: ...12 MACHINE DIMENSIONS Continued C 560NC DIMENSIONS...
Page 18: ...13 MACHINE DIMENSIONS Continued C 6260NC DIMENSIONS...
Page 19: ...14 MACHINE FEATURES...
Page 39: ...34 LUBRICATION DIAGRAM...