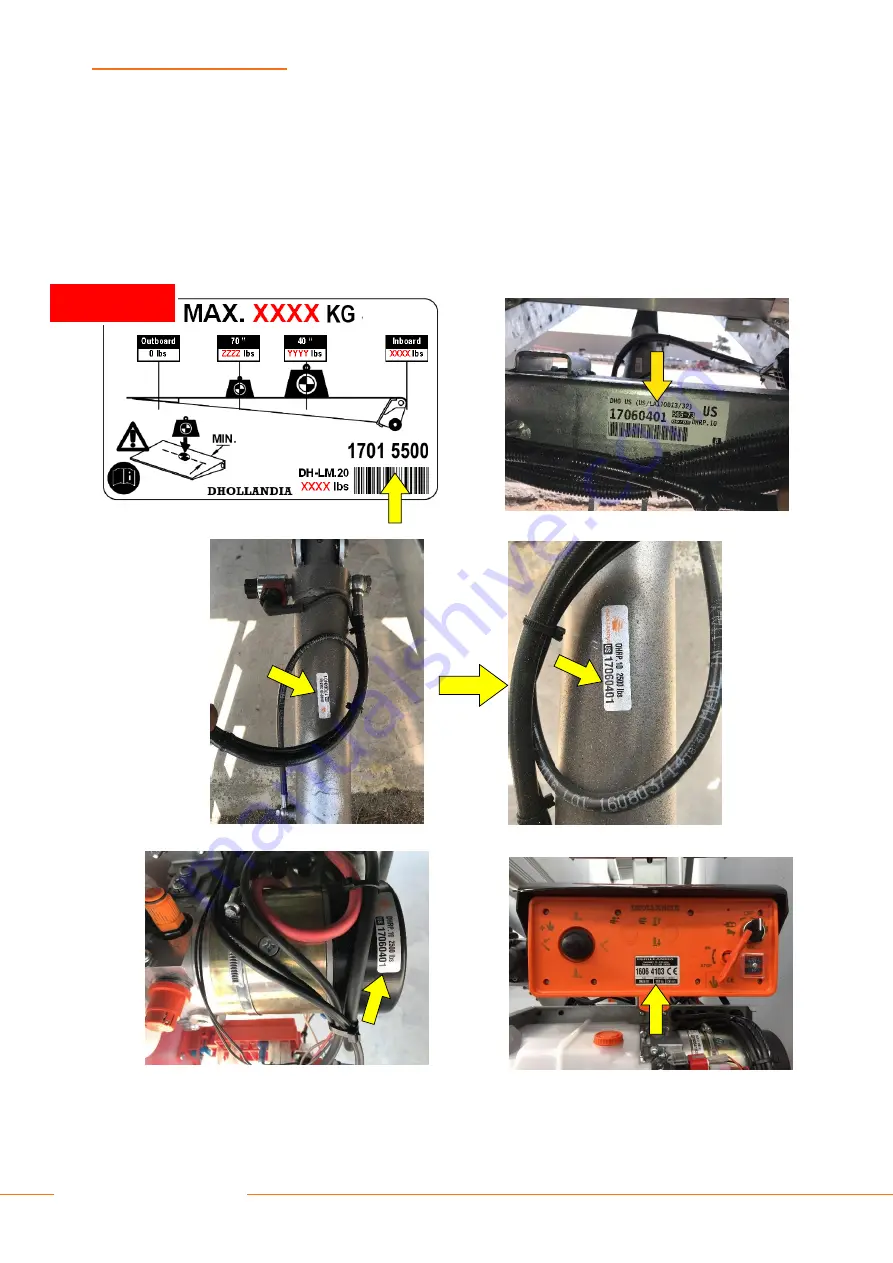
54
DHOLLANDIA
18.2
IDENTIFICATION DECALS
1.
Every DHOLLANDIA tail lift is identified and labelled with a unique 8-digit serial number (with or without a space between the first
and last 4 digits). This number is used for any inquiry on a particular tail lift, or when ordering replacement parts.
2.
In addition to the tail lift type and serial number, the various serial number labels provide additional information such as: the
maximum rated lift capacity and load chart, the bumper certification number, the date of manufacture, etc…
3.
The labels are usually affixed to the vehicle body and various tail lift components and can be found in the locations shown in the
images below.
EXAMPLE
Summary of Contents for DH-RP.10
Page 12: ...11 DHOLLANDIA Figure 6 2 MFT MTG...
Page 34: ...33 DHOLLANDIA Figure 11 5 Figure 11 4...
Page 50: ...49 DHOLLANDIA...
Page 65: ...64 DHOLLANDIA Figure 19 4 Figure 19 5...
Page 75: ...74 DHOLLANDIA...
Page 76: ...75 DHOLLANDIA...