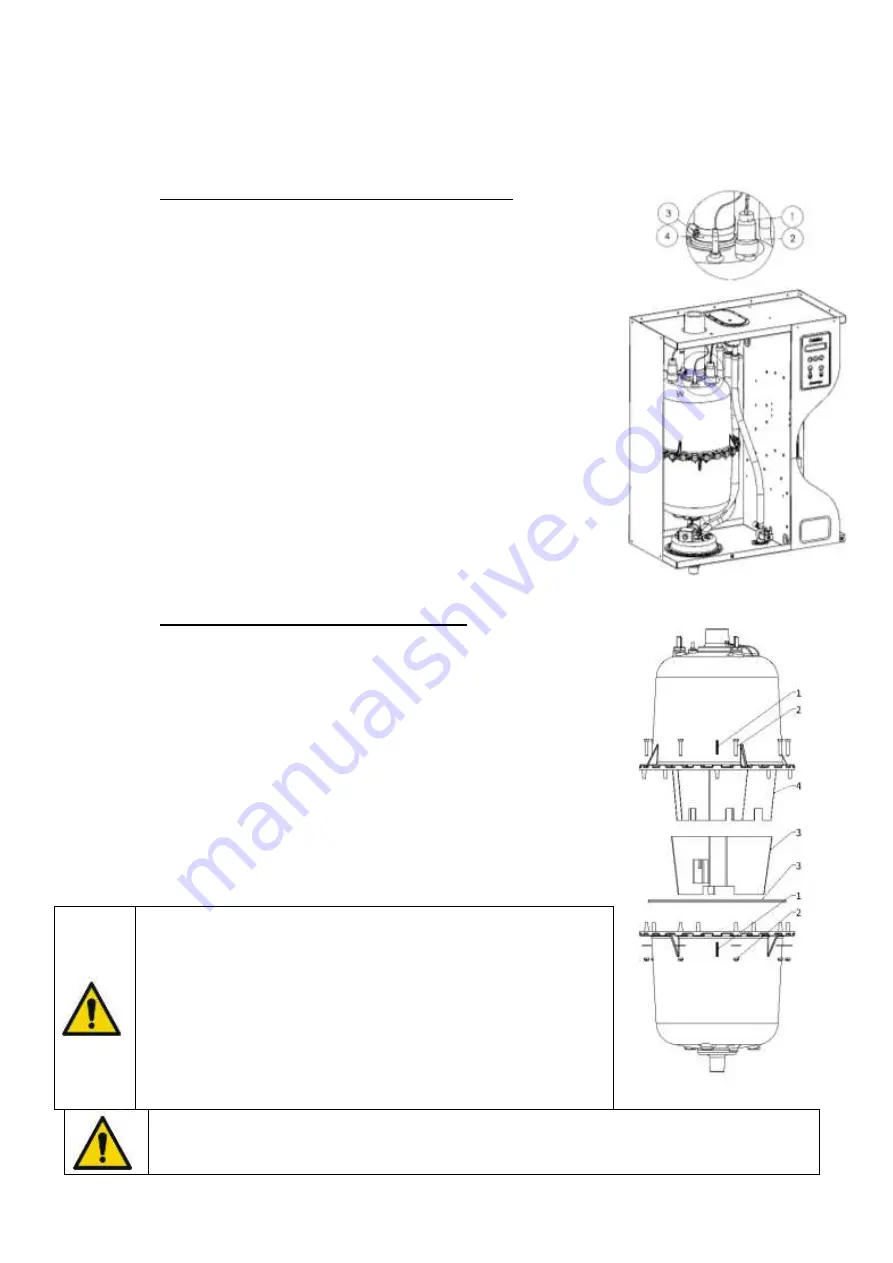
ElectroVap®
ELMC-SB
43
6.3
CYLINDER REPLACEMENT METHOD
•
Drain the cylinder
by pressing the drain button and wait until the cylinder is
completely empty. The message "DRAINING CYCLE OVER" appears.
•
Turn off power
of the power circuits (in the general electrical cabinet) and
control system located on the front of the device.
•
Remove the door from the hydraulic compartment
,
remove the power cable
connectors
and water
level sensor
(
1 and 2).
Then loosen the clamp to
disconnect the steam outlet hose (
3 and 4).
•
WARNING! Risk of burns
. If the drain is recent, the steam cylinder is still
burning. Therefore, wait for it to cool down.
•
Lift the cylinder up
by pressing down on its base to release it from the foot of
the drain valve.
•
Remove the top of the cylinder from the retaining clip
and remove it from the
hydraulic compartment.
•
Please tighten the steam hose slightly on the cylinder,
only when the cylinder
is cold, to avoid deformation.
6.4
CYLINDER CLEANING METHOD
•
After removing the cylinder, mark the two half-cylinders
(1)
at once.
•
Remove the nuts and screws holding with two keys of 8
(2
), open the cylinder.
Remove the strainer and seal, then clean them (
3).
•
Clean the electrodes, the brace, and the inside of the cylinder's bodies by
scraping the limestone (it is possible to use passed acid for power electrodes) (
4).
•
Rinse the electrodes, the bodies of the cylinder, the brace. Do not forget to clean
the strainer in the cylinder foot.
WARNING!
Never shake the edge of the cylinder shells to remove
limescale. It is imperative to systematically replace the cylinder seal
and reposition it in its housing. Always replace the sealing ring and
insert it into the profile of the lower barrel of the cylinder. Then insert
the upper part (electrodes).
Make sure to align the two shells, reposition the nuts and screws.
Tighten by screwing the screws opposite each other so that the seal
is not deformed.
If the power cables change, be sure to run them through the steam generator according to the
wiring diagram explained previously.
Summary of Contents for ElectroVap ELMC 20-30 SB
Page 1: ...STEAM GENERATOR FOR STEAM ROOM ElectroVap ELMC SB Series Instruction Operation Manual ...
Page 25: ...ElectroVap ELMC SB 25 3 8 6 Wiring diagrams ELMC 5 to 10 Up V 1x200 240V 50 60Hz ...
Page 26: ...ElectroVap ELMC SB 26 ELMC 5 to 30 Up V 3x200 690V 50 60Hz ...
Page 27: ...ElectroVap ELMC SB 27 ELMC 40 to 60 Up V 3x200 690V 50 60Hz ...
Page 28: ...ElectroVap ELMC SB 28 ELMC 90 Up V 3x200 690V 50 60Hz ...
Page 29: ...ElectroVap ELMC SB 29 3 9 OPTION Transformer connection ...
Page 51: ...ElectroVap ELMC SB 51 ...