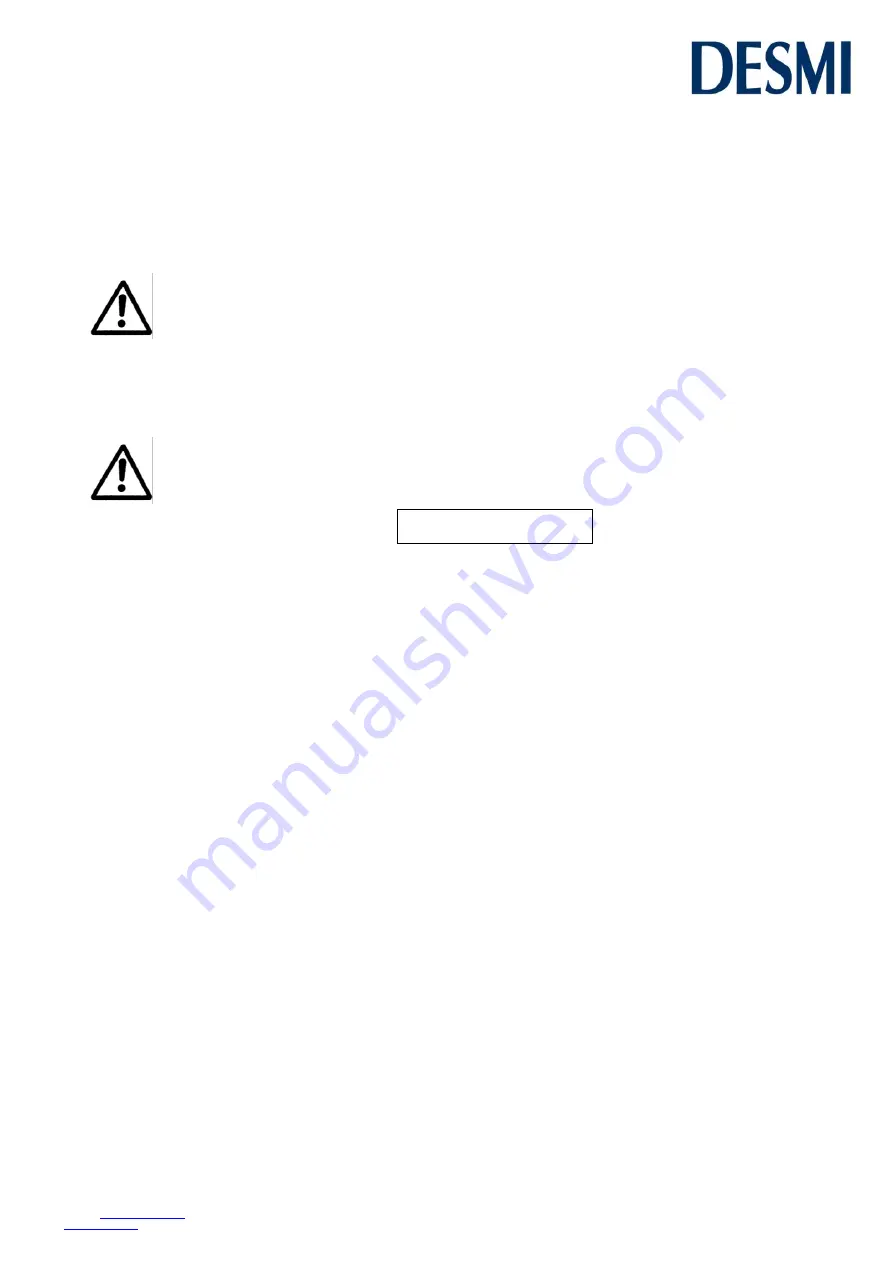
____________________________________________________________________________________
DESMI Pumping Technology A/S
10
Tagholm 1
9400 Nørresundby
–
Denmark
Tel: +45 96 32 81 11 Fax: +45 98 17 54 99
E-mail:
7. FROST PROTECTION
Pumps that are not in operation during frost periods are to be drained to avoid frost damage. Remove the
plug (3) at the bottom to empty the pump. Alternatively, it is possible to use anti-freeze liquids in normal
constructions.
8. DISMANTLING
Before dismantling the pump make sure that it has stopped. Empty the pump of liquid before
it is dismantled from the piping system. If the pump has been pumping dangerous
liquids you are to be aware of this and take the necessary safety measures.
If the pump has been pumping hot liquids, take great care that it is drained before it is
removed from the piping system.
9. START-UP
A centrifugal pump will not function until it has been filled with liquid between the foot valve
and somewhat above the impeller of the pump.
The liquid also serves as coolant for the shaft seal. In order to protect the shaft seal the
pump must not run dry.
ATTENTION
For safety reasons the pump is only allowed to operate against closed discharge valve for a short time
(max. 5 minutes and at a max. temperature of 80°C for standard pumps). Otherwise there is a risk of
damage to the pump and, at worst, of a steam explosion. If the pump is not monitored, the installation of
a safety device is recommended.
9.1 STARTING
Before starting the pump check that:
- the shaft rotates freely without jarring sounds.
- the pump casing and the suction line are filled with liquid.
Start the pump for a moment to check the direction of rotation. If the direction is correct (i.e. in the direction
of the arrow) the pump may be started.
10. SYSTEM BALANCING
It is often difficult to calculate a manometric delivery head in advance. It is, however, decisively important
to the quantity of liquid delivered.
A considerably smaller delivery head than expected will increase the quantity of liquid delivered, causing
increased power consumption and perhaps cavitation in pump and piping. In the pump the impeller may
show signs of heavy erosion caused by cavitation (corrosion) which may at times render an impeller unfit
for use in a very short time. Not unusually do similar erosions occur in pipe bends and valves elsewhere
in the piping system.
Therefore, after start-up, it is necessary to check either the quantity of liquid delivered or the power
consumption of the pump e.g. by measuring the current intensity of the connected motor. Together with a
reading of the differential pressure the quantity of water delivered can be determined against the
characteristics of the pump.