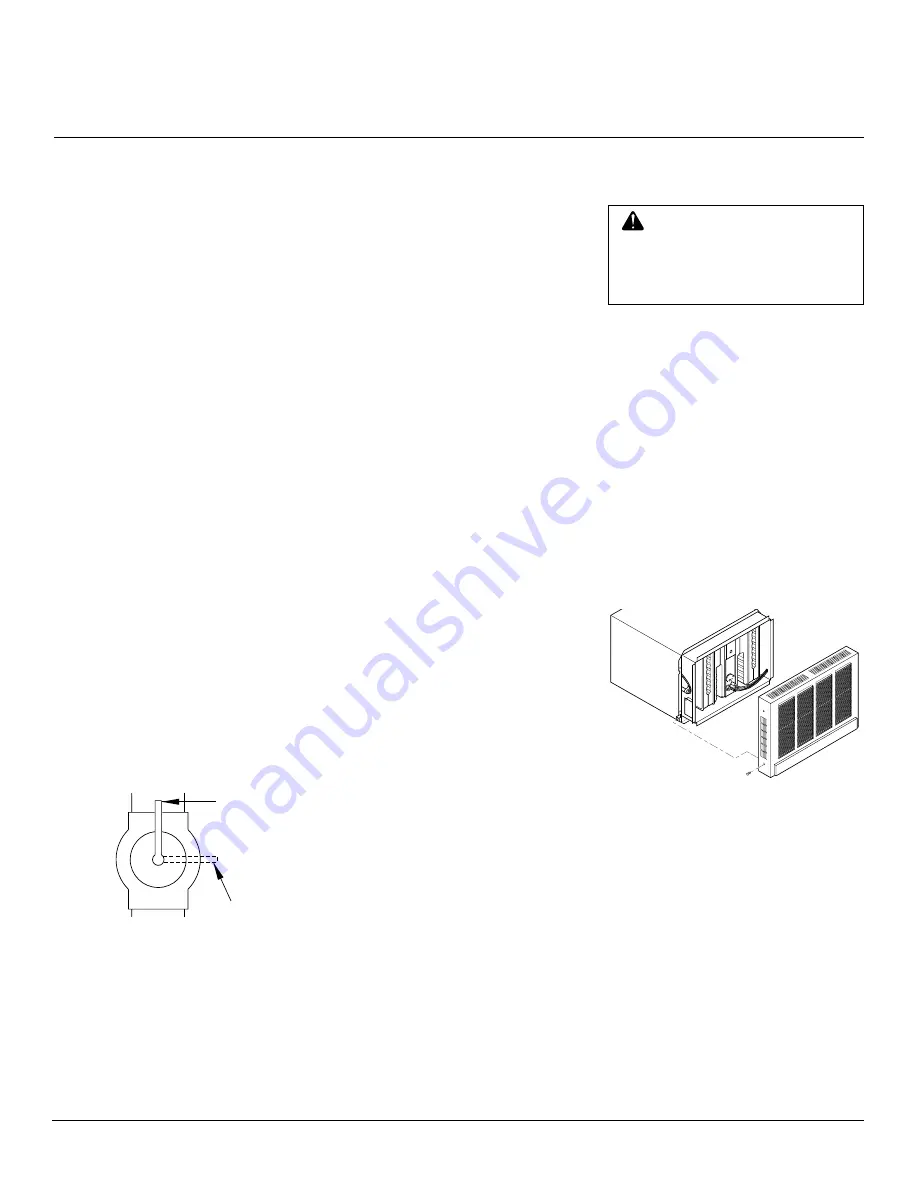
11
201839
OWNER’S MANUAL
Test Pressures Equal To or Less Than
1/2 PSIG (3.5 kPa)
1.
Close equipment shutoff valve (see Fig-
ure 16).
2.
Pressurize supply piping system by either
using compressed air or opening main gas
valve located on or near gas meter.
3.
Check all joints from gas meter to
equipment shutoff valve. Apply mix-
ture of liquid soap and water to gas
joints. Bubbles forming show a leak.
4.
Correct all leaks at once.
Pressure Testing Furnace Gas
Connections
1.
Open equipment shutoff valve (see Fig-
ure 16).
2.
Open main gas valve located on or near
gas meter.
3.
Make sure control knob of furnace is
in the OFF position.
4.
Check all joints from equipment shutoff
valve to gas inlet pipe. Apply mixture
of liquid soap and water to gas joints.
Bubbles forming show a leak.
5.
Correct all leaks at once.
6.
Turn on furnace (see Operating Fur-
nace, pages 12 and 13). Check the rest
of the internal joints for leaks.
7.
Turn off furnace (see To Turn Off Gas
to Furnace, page 13).
O
POSI
PO
Off Position
On Position
Figure 16 - Equipment Shutoff Valve
INSTALLATION
(Continued)
CONNECTING TO
ELECTRICAL SUPPLY
IMPORTANT:
Follow all local codes when
connecting electricity to furnace. In the ab-
sence of local codes, refer to the latest edi-
tion of the National Electrical Code ANS/
NFPA No. 70. If you are not familiar with
wiring codes, have a qualified electrician do
the wiring.
It is best to plug furnace into a separate and
permanent electrical line circuit.
1.
Supply a 120-volt, 60-cycle, grounded
outlet at furnace location.
2.
The furnace has a three-pronged
(grounded) plug. Use only a grounded,
three-prong outlet.
IMPORTANT:
Some local codes require
rigid or semi-rigid conduit or metallic
sheathe cable. When using a semi-rigid or
metallic sheathe cable, the installer must
terminate the supply wire in the terminal
box opening.
Performance Check
Plug furnace into three-pronged outlet. If
ignitor remains on after main burner igni-
tion or if the valve chatters, you may have
reversed polarity.
1.
Unplug furnace.
2.
Turn off electricity to outlet.
3.
Reverse 120-volt connections inside
outlet.
4.
Turn on electricity to outlet.
5.
Plug in furnace. Ignitor should turn off
after main burner ignites. If ignitor does
not turn off, or if valve continues to
chatter, turn off furnace and unplug.
Call a qualified service person.
ATTACHING CABINET
FRONT COVER
CAUTION: Do not operate fur-
nace with front cover removed or
mounted wrong. If front cover is
mounted wrong, you cannot se-
cure it to cabinet with screws.
1.
Hook top of front cover over top cabi-
net flange.
2.
Secure the sides of front cover to lower
sides of furnace cabinet with two
screws provided (see Figure 17).
IMPORTANT:
You may have removed fur-
nace from furnace cabinet during installa-
tion. You must correctly install furnace
within cabinet. If not, front cover will not
properly attach to cabinet. Make sure gas-
kets for intake and exhaust tubes are in
place. Make sure intake and exhaust tubes
extend into vent caps on cabinet back and
are secured with screws. Make sure you
secured flange on bottom of furnace to flange
on bottom front of cabinet.
Figure 17 - Attaching Front Cover to
Cabinet