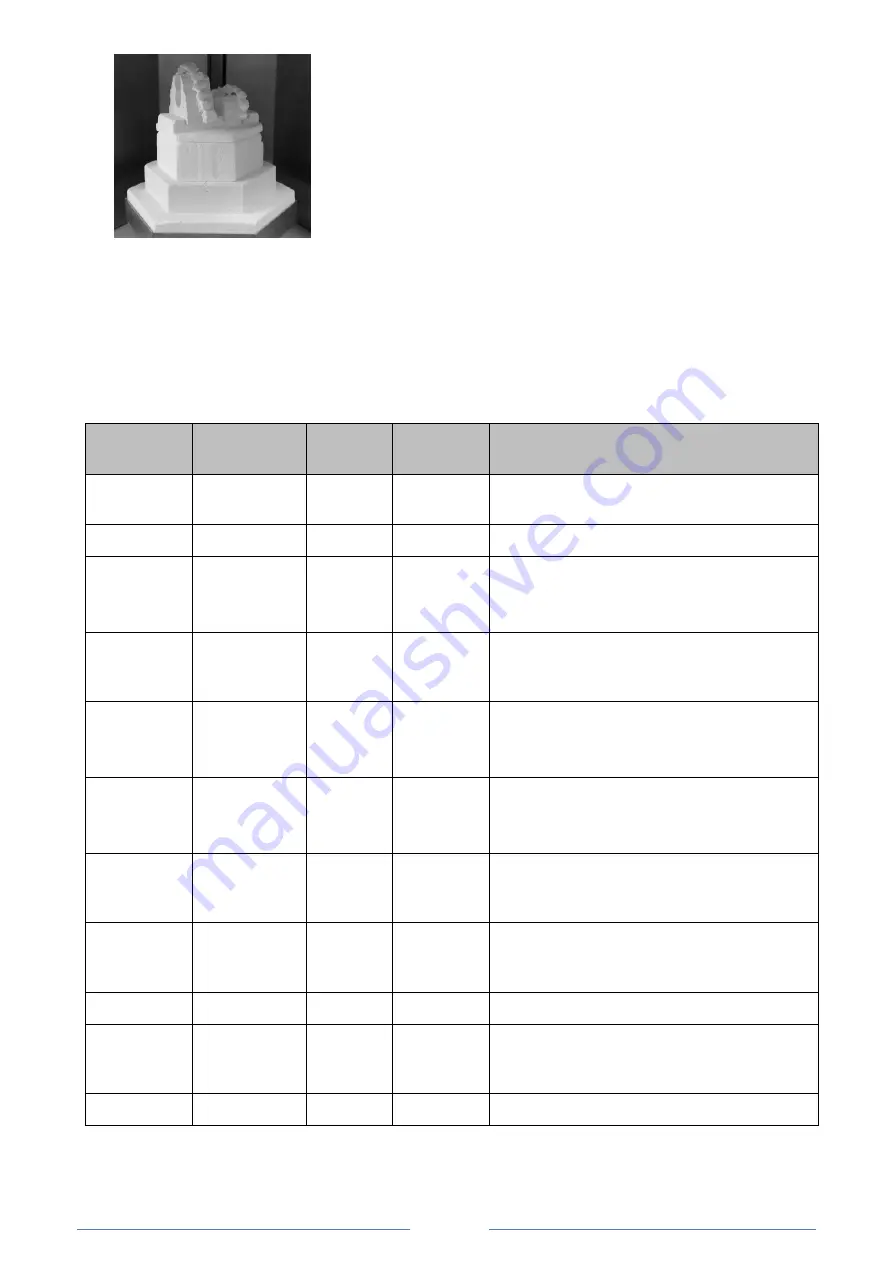
Page 29
Fig. 26:
Placement of bridges with
sintering bar (more than 8 units).
Bridges of more than 8 units are placed on the heating table
using a special sintering bar for large-span bridges.
Up to 2 large-span bridges can be sintered in the same
sintering cycle.
7.7
Programming
The following sintering programs for Crypton, Cercon base and Cercon ht are pre-programmed:
Program no.
Material
Duration
Final
temperature
Application
1 Crypton
Crypton
approx.
4.5 h
1280°C
Sintering of Crypton crowns and bridges with
sintering guard.
2 - - -
free
free
free
free
3 Cercon
base speed
≤ 6 Units
Cercon base,
colored, light,
medium
approx.
2.5 h
1465°C
Speed sintering bowl with cover up to
6-unit bridges
4 Cercon
base
Cercon base,
colored, light,
medium
approx. 5
h
1470°C
Speed sintering bowl with cover, up to
8-unit bridges
5 Cercon
base
≥ 9 Units
Cercon base,
colored, light,
medium
approx.
14 h
1470°C
Large-span bridges (more than 8 units) with
adapter plate. Maximum 2 large-span bridges.
6 Cercon ht
speed
≤ 6 Units
Cercon ht
white, light,
medium
approx. 3
h
1520°C
Speed sintering bowl with cover, up to
6-unit bridges
7 Cercon ht
Cercon ht
white, light,
medium
approx.
5.5 h
1520°C
Speed sintering bowl with cover, up to
8-unit bridges.
8 Cercon ht
≥ 9 Units
Cercon ht
white, light,
medium
approx.
14 h
1520°C
Large-span bridges (more than 8 units) with
adapter plate. Maximum 2 large-span bridges.
9 - - -
free
free
free
free
10 Service
heating
Service
heating
approx.
14.5 h
1540°C
Cleaning of the oven chamber and
reconstruction of the silica layer of the heating
elements.
11
–30
free
free
free
free