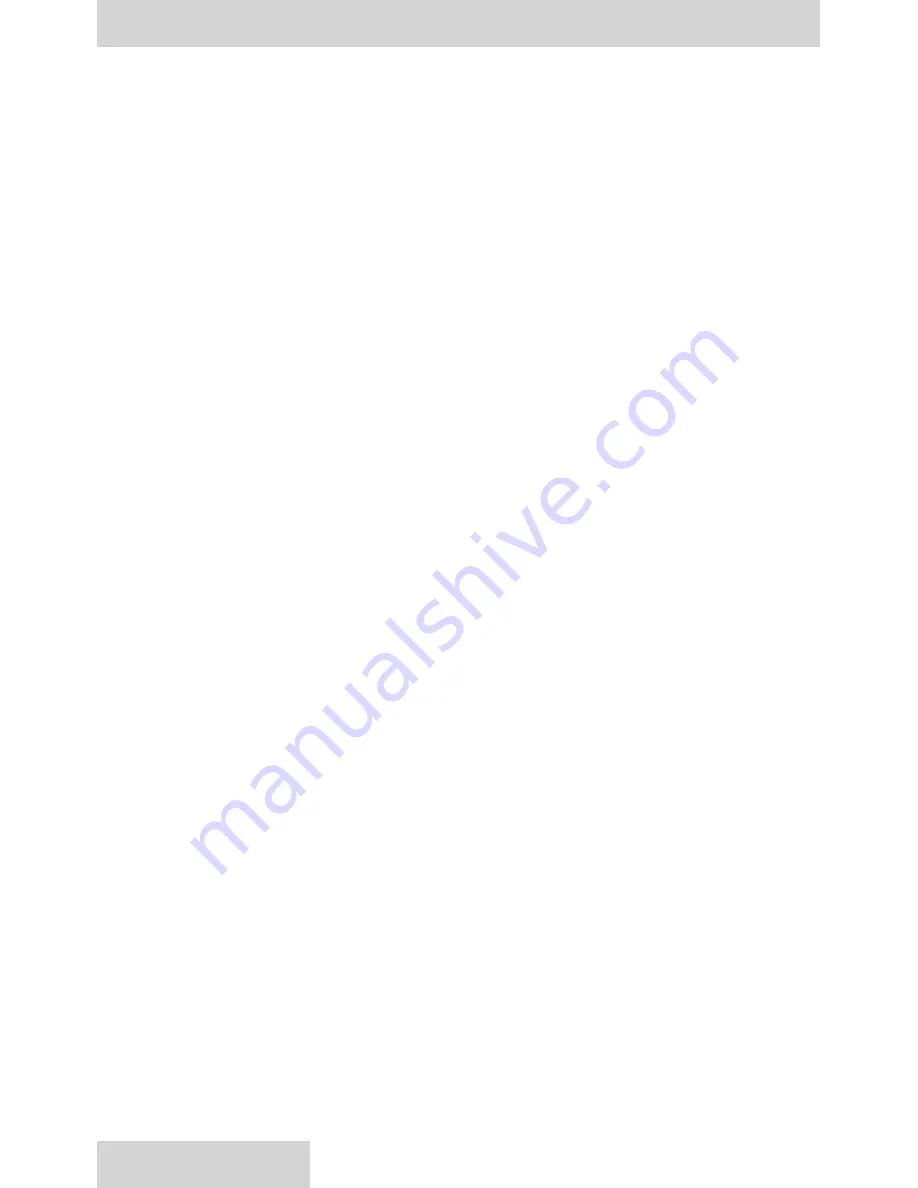
CONTROLS
25
GENERAL
The instructions contained in this manual cover complete disassembly and reassembly of the controls. Before pro-
ceeding with the disassembly or reassembly of any unit, this manual should be studied in order to become familiar with
proper order and parts nomenclature
DESCRIPTION OF OPERATION
A pilot operated valve spool and sleeve combination is the core of the control function. For the compensator, torque
limiter and load sensing controls, system pressure is applied to the input port of a three-way valve, and to one end of
the valve spool. A small orifice feeds this pressure to the other end of the spool, and limits pilot flow to approximately
115 in
3
/minute, 1,9 lpm. A spring on this end biases the spool to normally port the control piston to pump case. This
control piston links to the pump cam. On the opposite end of the control piston a small buck-up piston connects to
system pressure. This force, pump timing forces, and a spring combine to put the pump on stroke.
PRESSURE COMPENSATOR
A spring-loaded cone and seat connected to the spring end of the three-way spool establishes an adjustable pressure
limit on this end of the spool. When system pressure reaches this value, flow through the spool creates a pressure
difference across the spool. At approximately 250 psi, 17,2 bar difference, the spool shifts toward the spring, re-direct-
ing the control piston port to system pressure. This pressure applied to the control piston overcomes the forces
putting the pump on stroke, causing the pump to reduce displacement. When the pump pressure drops, the spool
meters to maintain the pump pressure at approximately 250 psi, 17,2 bar above the controlled pressure on the spring
side. The spring end of this three-way spool may also be connected to a remote pressure control, through the vent
port, “V”.
LOAD SENSING CONTROL
In the load sensing control, the system load pressure is applied to a modulating valve which establishes the compen-
sator vent pressure at 200 psi, 13,8 bar above load pressure. Adding the differential pressure across the compensator
spool to this pressure, the pump outlet pressure is approximately 350 psi to 450 psi, 24,1 to 31 bar above load pres-
sure. There is essentially no flow in the sensing line, and the pump supplies the flow required to develop 350 psi to
435 psi, 24,1 to 30 bar across the.metering valve to the load.
TORQUE LIMITER
The input torque is limited to a set value with the torque limiter control. To limit input torque, pump displacement is
reduced when pressure increases, and vice versa. This is accomplished by controlling the compensator pilot pressure
with a linkage to the pump stroking piston.
The compensator vent connects to one end of a pin which is spring loaded on the other end. The pin slides through a
spool which is positioned by a linkage to the control piston. Vent flow passes through the pin to a cross drilled hole,
which is opened or blocked by the motion of the spool. As system pressure increases, the pin moves against the
springs till the cross drilled passage opens, venting the compensator and causing the pump to reduce displacement.
As displacement reduces, the sleeve follows, closing the cross drilled passage and establishing control at a higher
pressure. For any pressure, there is a corresponding pump displacement. The position of the spool is controlled by
the pressure acting against two springs, one which is always in contact with the pin, and the other which comes in con-
tact as pressure increases, providing an increase in spring rate as pressure increases
TORQUE LIMITER WITH LOAD SENSING
A modulating valve is mounted to a torque limiter body to provide a load sensing control with torque limiting and pressure
compensator override
ROTARY SERVO CONTROL
The rotary servo control is mounted on the off-stroke side of the control piston. Servo pressure is connected to the
input port of a four-way valve, and to the end of this valve spool. A drilling and orifice connects to the opposite end of
the spool. One cylinder port connects to the “off stroke” end of the control piston, while the other cylinder port con-
nects to the “on stroke” end of the control piston, through the control on the opposite side.
A rotatable shaft converts to a linear motion on a pin. A sleeve over the pin is driven by a linkage to the control pis-
ton. The sleeve/pin combination meters pilot flow from the four-way valve controlling the shifting of the four-way valve,
in such a manner that the four-way valve shifts to hold the cylinder position to the corresponding position for the input
rotation.
www.comoso.com
Summary of Contents for P07 C-mod
Page 54: ...PQ HIGH RESPONSE CONTROL 54 PQ CONTROL IN PROCESS OF DEVELOPMENT www comoso com ...
Page 55: ...PQ HIGH RESPONSE CONTROL 55 PQ CONTROL IN PROCESS OF DEVELOPMENT www comoso com ...
Page 56: ...PQ HIGH RESPONSE CONTROL 56 PQ CONTROL IN PROCESS OF DEVELOPMENT www comoso com ...
Page 57: ...PQ HIGH RESPONSE CONTROL 57 PQ CONTROL IN PROCESS OF DEVELOPMENT www comoso com ...
Page 74: ...74 TEST PROCEDURE PQ CONTROL IN PROCESS OF DEVELOPMENT www comoso com ...