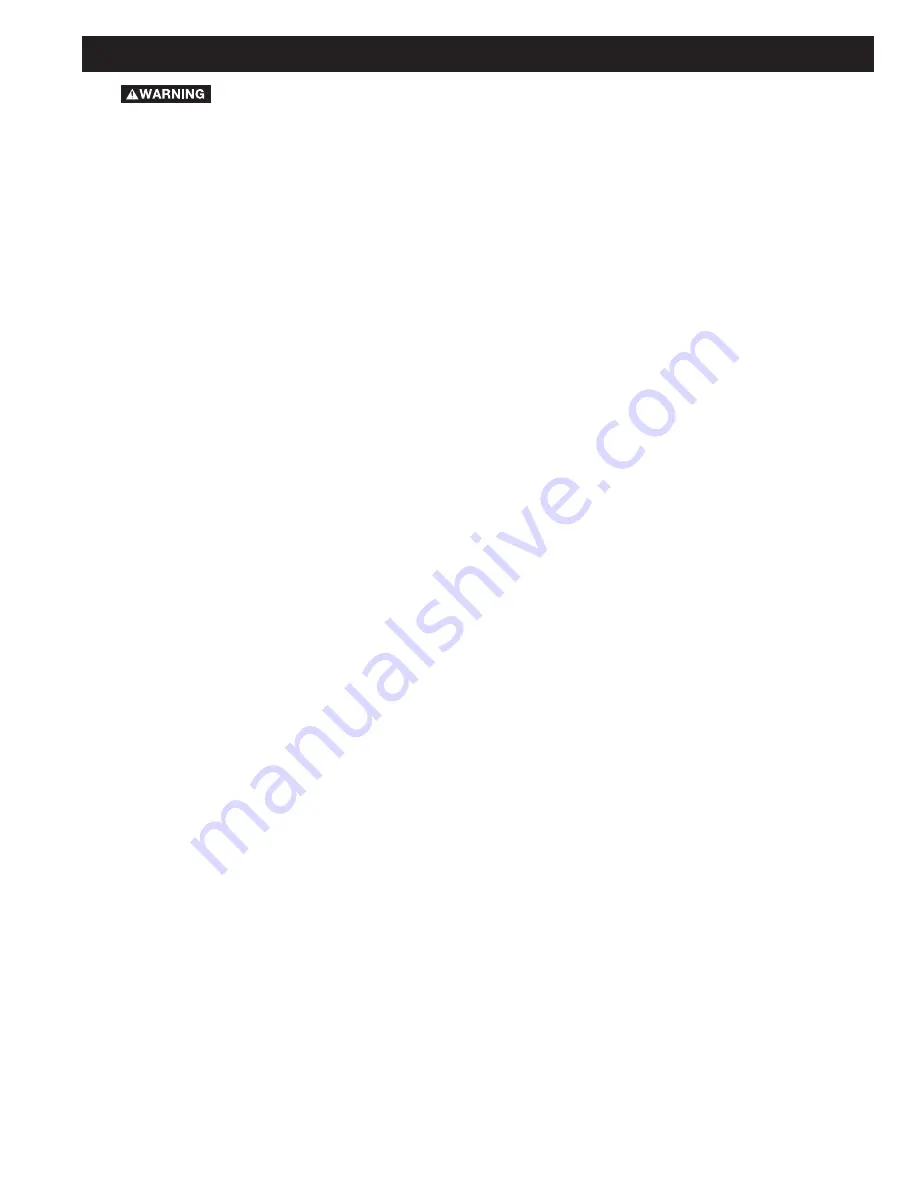
5
FAILURE TO FOLLOW THESE RULES MAY RESULT IN SERIOUS PERSONAL INJURY.
ADDITIONAL SAFETY RULES FOR JOINTERS
SAVE THESE INSTRUCTIONS.
Refer to them often and use them to instruct others.
1.
DO NOT OPERATE THIS MACHINE
until it is
completely assembled and installed according to the
instructions. A machine incorrectly assembled can
cause serious injury.
2.
OBTAIN ADVICE
from your supervisor, instructor, or
another qualified person if you are not thoroughly
familiar with the operation of this machine.
Knowledge is safety.
3.
FOLLOW ALL WIRING CODES
and recommended
electrical connections to prevent shock or
electrocution.
4.
KEEP KNIVES SHARP
and free from rust and pitch.
Dull or rusted knives work harder and can cause
kickback.
5.
TIGHTEN THE INFEED/OUTFEED TABLES
before
starting the machine. Loss of control of the work-
piece can cause serious injury.
6.
PROPERLY SECURE THE BLADES IN THE CUTTERHEAD
before turning the power “ON”. Loose blades may be
thrown out at high speeds.
7.
NEVER TURN THE MACHINE “ON”
before clearing the
table of all objects (tools, scraps of wood, etc.). Flying
debris can cause serious injury.
8.
NEVER TURN THE MACHINE “ON”
with the workpiece
contacting the cutterhead. Kickback can occur.
9.
AVOID AWKWARD OPERATIONS AND HAND
POSITIONS.
A sudden slip could cause a hand to
move into the cutterhead.
10.
KEEP ARMS, HANDS, AND FINGERS
away from
the cutterhead to prevent severe injury.
11.
NEVER MAKE CUTS
deeper than 1/8" (3.2mm) to
prevent kickback.
12.
NEVER JOINT OR PLANE A WORKPIECE
that is
shorter than 10" (254mm), narrower than 3/4"
(19.0MM), or less than 1/2" (12.7mm) thick. Jointing
smaller workpieces can place your hand in the
cutterhead causing severe injury.
13.
USE HOLD-DOWN/PUSH BLOCKS
for jointing or
planing any workpiece lower than the fence. Jointing
or planing small workpieces can result in kickback
and severe injury.
14.
HOLD THE WORKPIECE FIRMLY
against the table
and fence. Loss of control of the workpiece can
cause kickback and result in serious injury.
15.
NEVER PERFORM “FREE-HAND” OPERATIONS.
Use
the fence to position and guide the workpiece. Loss
of control of the workpiece can cause serious injury.
16.
DO NOT
attempt to perform an abnormal or little-
used operation without study and the use of
adequate hold-down/push blocks, jigs, fixtures,
stops, etc.
17.
DO NOT FEED A WORKPIECE
into the outfeed end
of the machine.The workpiece will be thrown out of
the opposite end at high speeds.
18.
DO NOT FEED A WORKPIECE
that is warped,
contains knots, or is embedded with foreign objects
(nails, staples, etc.) to prevent kickback.
19.
MAINTAIN THE PROPER RELATIONSHIP OF
INFEED AND OUTFEED TABLE SURFACES
and
cutterhead knife path. Loss of control of the work-
piece can cause serious injury.
20.
PROPERLY SUPPORT LONG OR WIDE WORKPIECES.
Loss of control of the workpiece can cause injury.
21.
NEVER PERFORM LAYOUT, ASSEMBLY, OR SET-
UP WORK
on the table/work area when the
machine is running. A sudden slip could cause a
hand to move into the cutterhead. Severe injury
can result.
22.
TURN THE MACHINE “OFF”,
disconnect the
machine from the power source, and clean the
table/work area before leaving the machine.
LOCK
THE SWITCH IN THE “OFF” POSITION
to prevent
unauthorized use. Someone else might accidentally
start the machine and cause injury to themselves.
23.
ADDITIONAL INFORMATION
regarding the safe
and proper operation of power tools (i.e. a safety
video) is available from the Power Tool Institute,
1300 Sumner Avenue, Cleveland, OH 44115-2851
(www.powertoolinstitute.com). Information is also
available from the National Safety Council, 1121
Spring Lake Drive, Itasca, IL 60143-3201. Please
refer to the American National Standards Institute
ANSI 01.1 Safety Requirements for Woodworking
Machines and the U.S. Department of Labor OSHA
1910.213 Regulations.
Summary of Contents for Delta JT360
Page 28: ...28 NOTES...