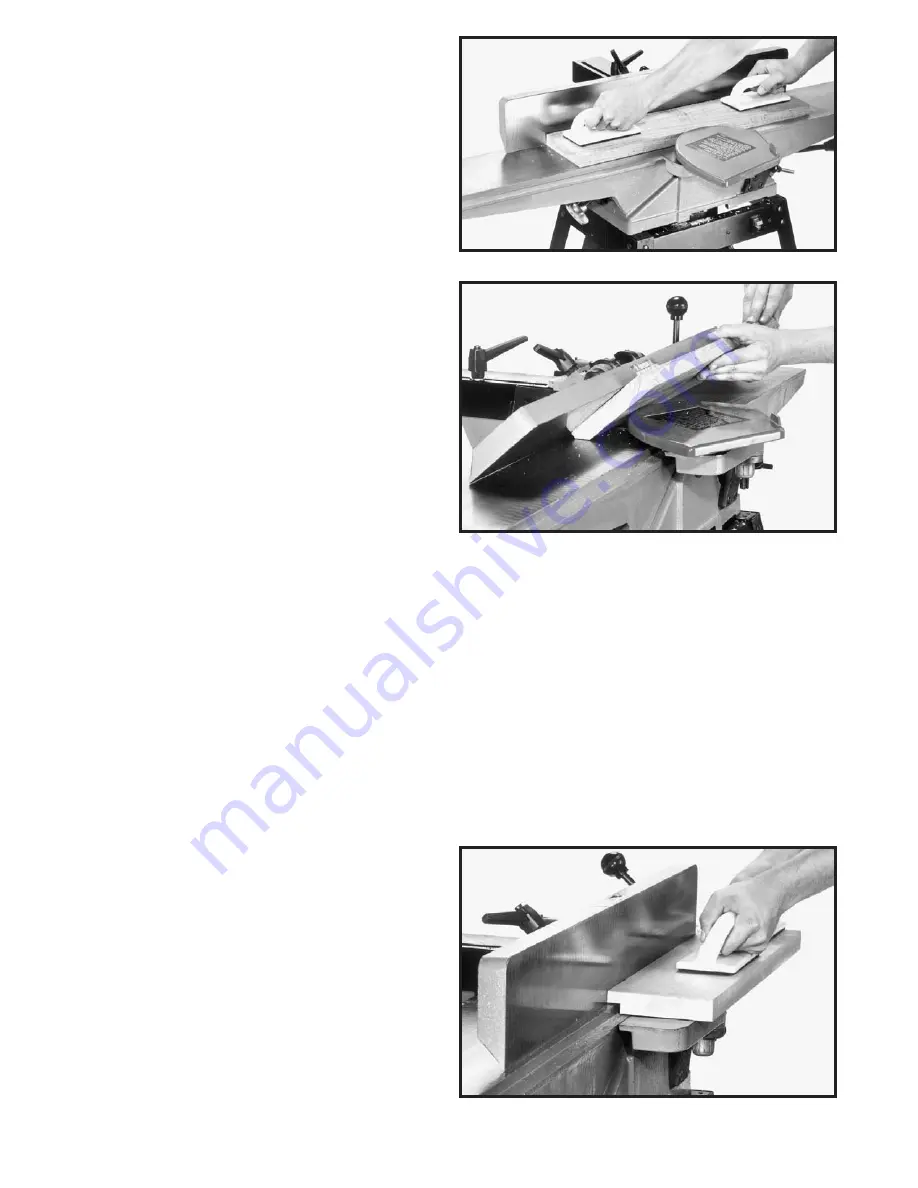
24
PLANING OR SURFACING
Planing or surfacing is identical to the jointing operation
except for the position of the workpiece. For planing, the
major flat surface of the workpiece is placed on the infeed
table of the jointer with the narrow edge of the workpiece
against the fence, a shown in Fig. 67. The workpiece is
moved from the infeed table, across the cutterhead to the
outfeed table establishing a flat surface on the workpiece
Always use push blocks when performing planing opera-
tions and never pass your hands directly over the
cutterhead. Maximum depth of cut should not be more
than 1/8" in one pass.
Fig. 67
Fig. 68
BEVELING
To cut a bevel, lock the fence at the required angle and
run the work across the knives while keeping the work
firmly against the fence and tables. Several passes may
be necessary to arrive at the desired result. When the
angle is small, there is little difference whether the fence
is tilted to the right or left. However, at greater angles
approaching 45 degrees, it is increasingly difficult to hold
the work properly when the fence is tilted to the right.
The advantage of the double-tilting fence is appreciated
under such conditions.
When tilted to the left, the fence forms a V-shape with
the tables, and the work is easily pressed into the pocket
while passing it across the knives as shown in Fig. 68. If
the bevel is laid out on the piece in such direction that
this involves cutting against the grain, it will be better to
tilt the fence to the right.
TAPER CUTS
One of the most useful jointer operations is cutting an edge to a taper. This method can be used on a wide variety of
work. Tapered legs of furniture are a common example.
Instead of laying the piece on the infeed table, lower the forward end of the work onto the outfeed table. Do this very
carefully, as the piece will span the knives, and they will take a “bite” from the work with a tendency to kick back unless
the piece is firmly held. Now push the work forward as in ordinary jointing. The effect is to plane off all the stock in front
of the knives, to increasing depth, leaving a tapered surface.
The ridge left by the knives when starting the taper may be removed by taking a very light cut according to the regular
method for jointing, with the infeed table raised to its usual position.
Practice is required in this operation, and the beginner is advised to make trial cuts on waste material. Taper cuts over
part of the length and a number of other special operations can easily be done by the experienced craftsman.
CUTTING A RABBET
When making a rabbet cut, as shown in Fig. 69, the
cutterhead guard must be removed.
AFTER THE
RABBET CUT IS COMPLETED, BE CERTAIN GUARD
IS REPLACED.
1. Adjust the fence so that the distance between the end
of the knives and the fence is equal to the width of the
rabbet.
2. Lower the infeed table an amount equal to the depth
of the rabbet. If the rabbet is quite deep, it may be
necessary to cut it in two or more passes. In that event,
the table is lowered an amount equal to about half the
depth of the rabbet for the first pass, then lowered again
to proper depth to complete the cut. Maximum depth of
cut when rabbeting with this jointer is 1/2 inch.
Fig. 69
Summary of Contents for Delta JT360
Page 28: ...28 NOTES...