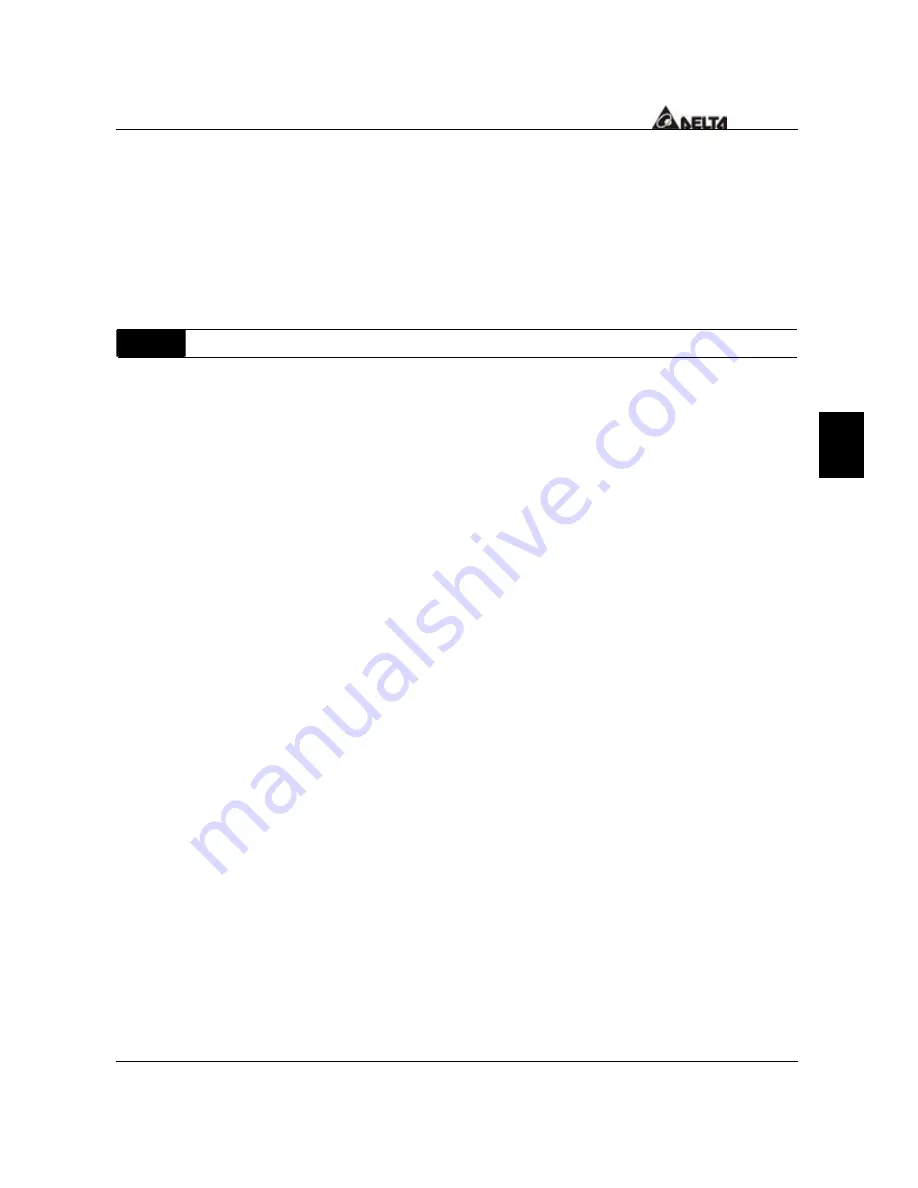
5
VFD-F Series
DELTA ELECTRONICS, INC. ALL RIGHTS RESERVED
5-35
This parameter allows the user to enter their password to unlock the Parameter Protection
feature. The password entered must match the value entered into Pr.6-17. After three
invalid password attempts, the drive will no longer allow any operation. The drive must then
be powered off and back on again.
After successfully entering the password, the user may change parameters as they wish.
Once the drive is powered off, the drive has locked the parameters again. To clear the
password, the user must enter the correct password in Pr.6-16 and then set Pr.6-17 to 00.
06 - 17
Parameter Protection Password Setting
Factory Setting: 00
Settings
00~65535
00: No password protection
This parameter allows the user to set a password for parameter protection. After entering a
password, Pr.6-17 will display 1.
Be sure to keep the password in a safe place. If the password is lost, please return the
drive to DELTA.
Summary of Contents for AC Drive VFD-F Series
Page 1: ......
Page 2: ......
Page 3: ......
Page 107: ...VFD F Series DELTA ELECTRONICS INC ALL RIGHTS RESERVED This page intentionally left blank...
Page 133: ...VFD F Series DELTA ELECTRONICS INC ALL RIGHTS RESERVED This page intentionally left blank...
Page 161: ...VFD F Series DELTA ELECTRONICS INC ALL RIGHTS RESERVED C 8 KPF CC01 Unit mm inches...