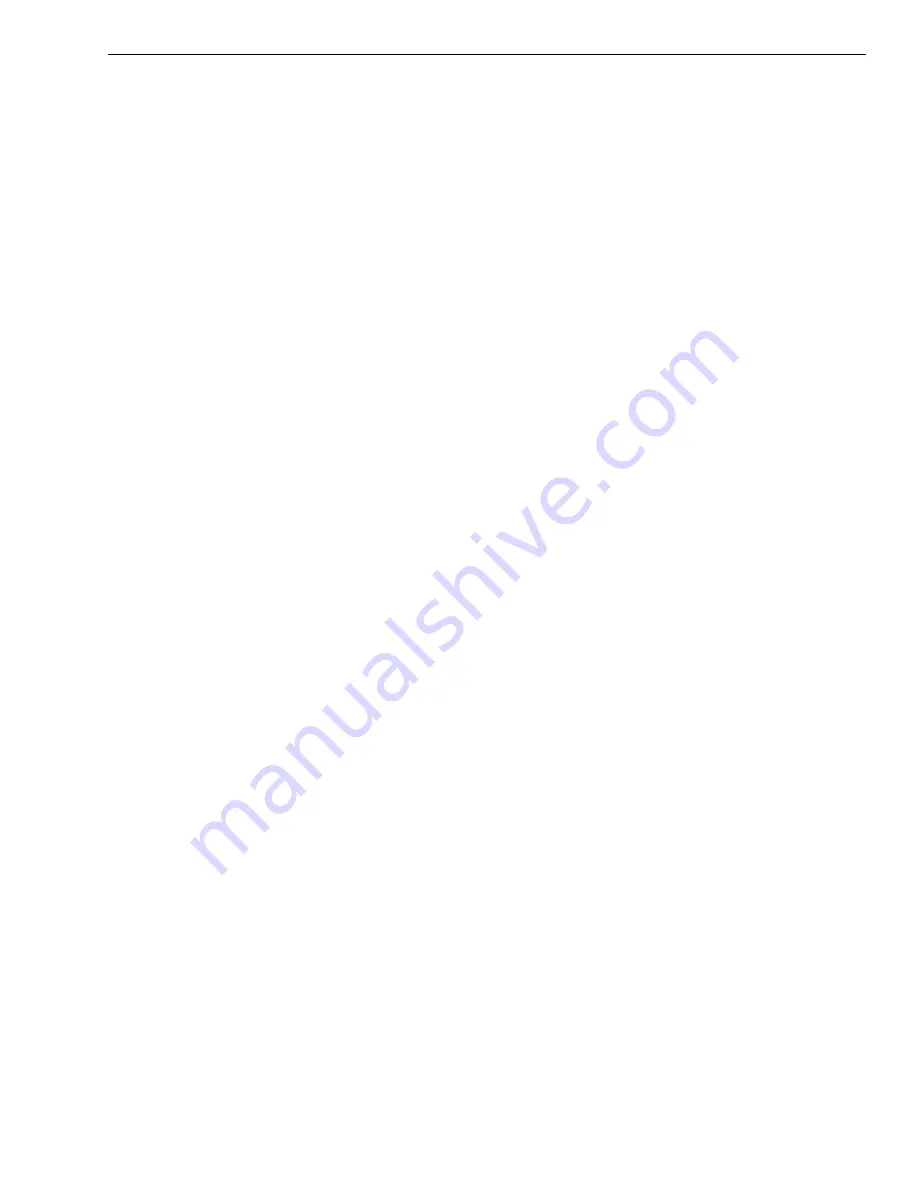
Troubleshooting
79
If Your Module Needs Factory Service
If your module must be returned to Data Translation, do the following:
1.
Record the module’s serial number, and then contact the Customer Service Department at
(508) 481-3700, ext. 1323 (if you are in the USA) and obtain a Return Material
Authorization (RMA).
If you are located outside the USA, call your local distributor for authorization and
shipping instructions; see our web site (www.datatranslation.com) for the name and
telephone number of you nearest distributor. All return shipments to Data Translation
must be marked with the correct RMA number to ensure proper processing.
2.
Using the original packing materials, if available, package the module as follows:
−
Wrap the module in an electrically conductive plastic material. Handle with ground
protection. A static discharge can destroy components on the board.
−
Place in a secure shipping container.
3.
Return the board to the following address, making sure the RMA number is visible on the
outside of the box.
Customer Service Dept.
Data Translation, Inc.
100 Locke Drive
Marlboro, MA 01752-1192
Summary of Contents for DT9824
Page 1: ...DT9824 UM 23782 G User s Manual Title Page ...
Page 4: ......
Page 8: ...Contents 8 ...
Page 12: ...About this Manual 12 ...
Page 13: ...13 1 Overview Features 14 Supported Software 16 Getting Started Procedure 18 ...
Page 19: ...Part 1 Getting Started ...
Page 20: ......
Page 28: ...Chapter 2 28 ...
Page 44: ...Chapter 4 44 ...
Page 45: ...45 Part 2 Using Your Module ...
Page 46: ...Chapter 46 ...
Page 47: ...47 5 Principles of Operation Analog Input Features 49 Digital I O Features 54 ...
Page 56: ...Chapter 5 56 ...
Page 68: ...Chapter 6 68 ...
Page 74: ...Chapter 7 74 ...
Page 80: ...Chapter 8 80 ...
Page 92: ...Appendix A 92 ...
Page 98: ...Appendix B 98 ...