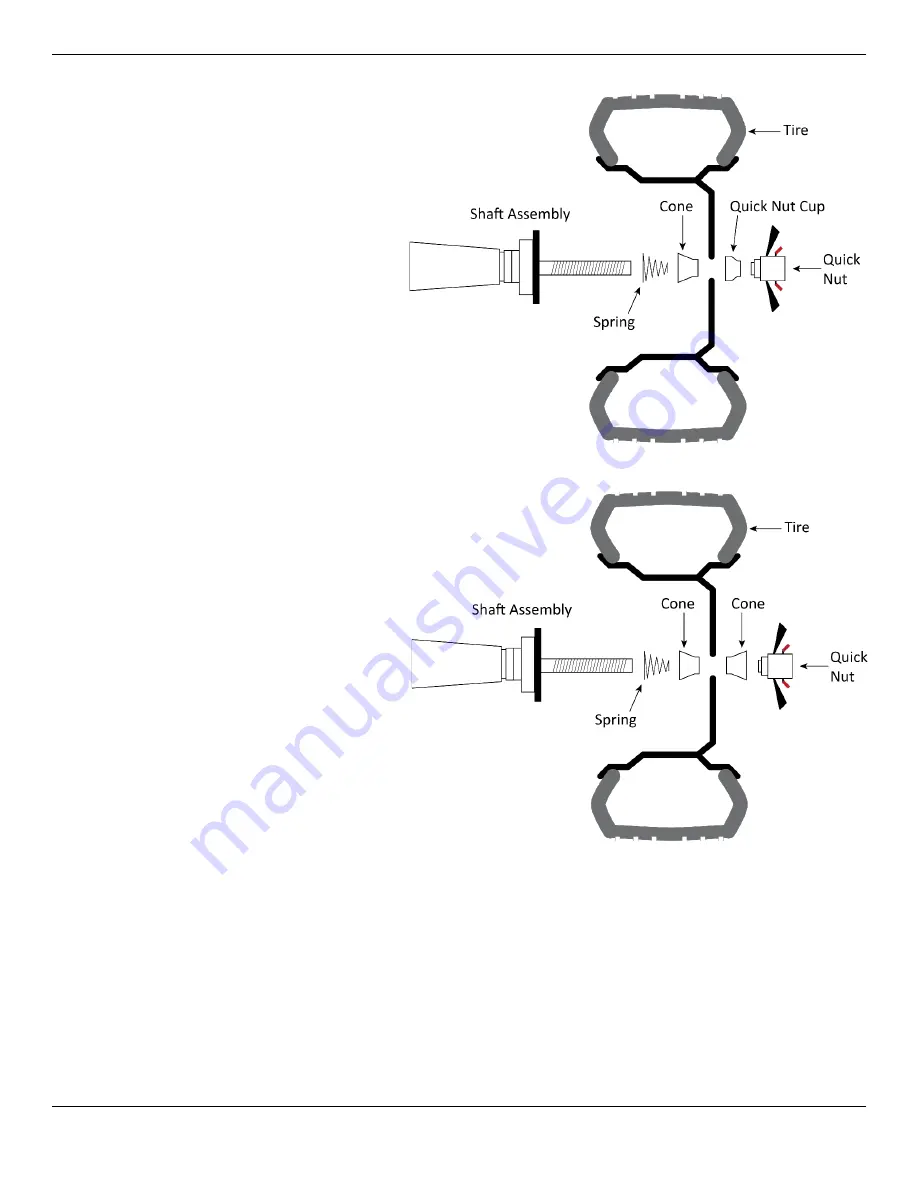
DB-70 Automatic Wheel Balancer
25
P/N 5900261 — Rev. A1 — January 2021
Rear-Cone Mounting.
Use this method if the Wheel cannot
be mounted with the Front-Cone
Mounting. The spring is placed on
the Shaft first, then use an
appropriate sized cone, the Wheel,
the Quick Nut Cup and the Quick
Nut.
Dual Cone Mounting.
Generally only used for some
aftermarket or OEM performance
wheels that have a center hole deep
enough to allow the use of two
cones on the Shaft.
To mount a Wheel
:
1.
Make sure you are dressed
appropriately: leather gloves,
steel-toed work boots, back
belts, hearing protection, and
ANSI-approved eye protection:
safety glasses, face shield, or
goggles.
2.
Determine which mounting method you want to use.
3.
Move the Wheel you are going to mount next to the Shaft.
4.
Select the Mounting Cone that best fits the center hole on the Wheel.
5.
If Rear-Cone or Dual-Cone mounting, install the cone spring and the desired cone onto the Shaft.
6.
Clean the wheel.
7.
Remove accumulated dust and provide a clean mounting surface for the Wheel.
8.
Remove any weights from previous balancing efforts.
9.
Visually inspect the wheel mounting surface for deformations or damage that would prevent the
wheel from riding on the Shaft correctly.
Summary of Contents for DB-70
Page 52: ...DB 70 Automatic Wheel Balancer 52 P N 5900261 Rev A1 January 2021 Labels A...
Page 53: ...DB 70 Automatic Wheel Balancer 53 P N 5900261 Rev A1 January 2021 B C E...
Page 61: ...DB 70 Automatic Wheel Balancer 61 P N 5900261 Rev A1 January 2021 Inner Distance Arm Assy...
Page 65: ...DB 70 Automatic Wheel Balancer 65 P N 5900261 Rev A1 January 2021 Wiring...
Page 66: ...DB 70 Automatic Wheel Balancer 66 P N 5900261 Rev A1 January 2021 Maintenance Log...
Page 67: ...DB 70 Dynamic Wheel Balancing Machine 67 P N 5900261 Rev A1 January 2021 Maintenance Log...
Page 68: ...1645 Lemonwood Drive Santa Paula CA 93060 USA 2021 BendPak Inc All rights reserved Dannmar com...