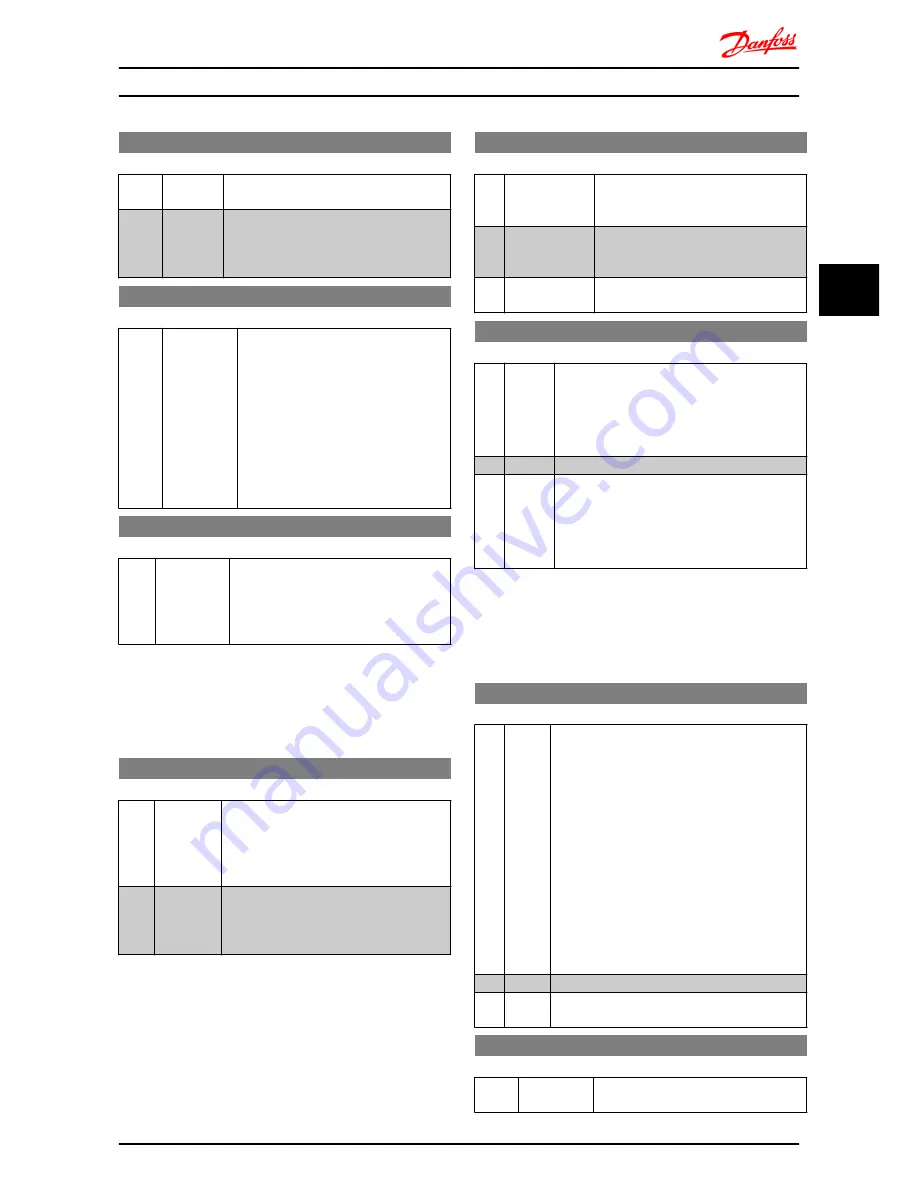
1-61 High Speed Load Compensation
Range:
Function:
Use this parameter to obtain optimum load
compensation when running at high speed.
100 %
*
[0-199 %] Enter percentage to compensate in relation
to load when motor runs at high speed.
Change-over point is automatically
calculated based on motor size.
1-62 Slip Compensation
Range:
Function:
100 %
*
[-400-399
%]
Compensation for load dependent motor
slip.
Slip compensation is calculated automat-
ically based on rated motor speed, n
M,N
.
NOTE
This function is only active when
1-00 Configuration Mode
, is set to
[0]
Speed Open Loop
and when
1-01
Motor Control Principle
, is set to
[1]
VVC
plus
1-63 Slip Compensation Time
Range:
Function:
0.10 s [0.05-5.00 s] Enter slip compensation reaction speed. A
high value results in slow reaction whereas
a low value results in quick reaction.
If low-frequency resonance problems arise,
use longer time setting.
4.2.5 1-7* Start Adjustments
Considering the need for various start functions in different
applications, it is possible to select a number of functions
in this parameter group.
1-71 Start Delay
Range:
Function:
The start delay defines the time to pass from
a start command is given until the motor
starts accelerating.
Setting start delay to 0.0 s disables
1-72 Start
Function
, when start command is given.
0.0 s
*
[0.0-10.0
s]
Enter the time delay required before
commencing acceleration.
1-72 Start Function
is active during
Start delay
time
.
1-72 Start Function
Option:
Function:
[0]
DC Hold/Delay
Time
Motor is energised with DC holding
current (
2-00 DC Hold Current
) during
start delay time.
[1]
DC Brake/Delay
Time
Motor is energised with DC braking
current (
2-01 DC Brake Current
) during
start delay time.
[2]
*
Coast/Delay
Time
Inverter is coasted during start delay time
(inverter off).
1-73 Flying Start
Option:
Function:
The Flying Start parameter is used to catch a
spinning motor after eg. mains drop-out.
NOTE
This function is not suitable for hoisting
applications.
[0]
*
Disabled Flying start is not required.
[1]
Enabled Frequency converter enabled to catch spinning
motor.
NOTE
When flying start is enabled
1-71 Start Delay
,
and
1-72 Start Function
, have no function.
4.2.6 1-8* Stop Adjustments
To meet the need for various stop functions in different
application these parameters offer some special stop
features for the motor.
1-80 Function at Stop
Option:
Function:
The selected function at stop is active in following
situations:
•
Stop command is given and output
speed is ramped down to
Min. Speed for
Function at Stop
.
•
Start command is removed (standby),
and output speed is ramped down to
Min. Speed for Function at Stop
.
•
DC-brake command is given, and DC-
brake time has passed
•
While running and calculated output
speed is below
Min. Speed for Function at
Stop
.
[0]
*
Coast
The inverter is coasted.
[1]
DC
hold
The motor is energised with a DC current. See
2-00 DC Hold Current
for more information.
1-82 Min. Speed For Function at Stop [Hz]
Range:
Function:
0.0 Hz
*
[0.0-20.0 Hz] Set the speed at which to activate
1-80
Function at Stop
.
Parameter Descriptions
VLT
®
Micro Drive FC 51 Programming Guide
MG02C602 - VLT
®
is a registered Danfoss trademark
17
4
4