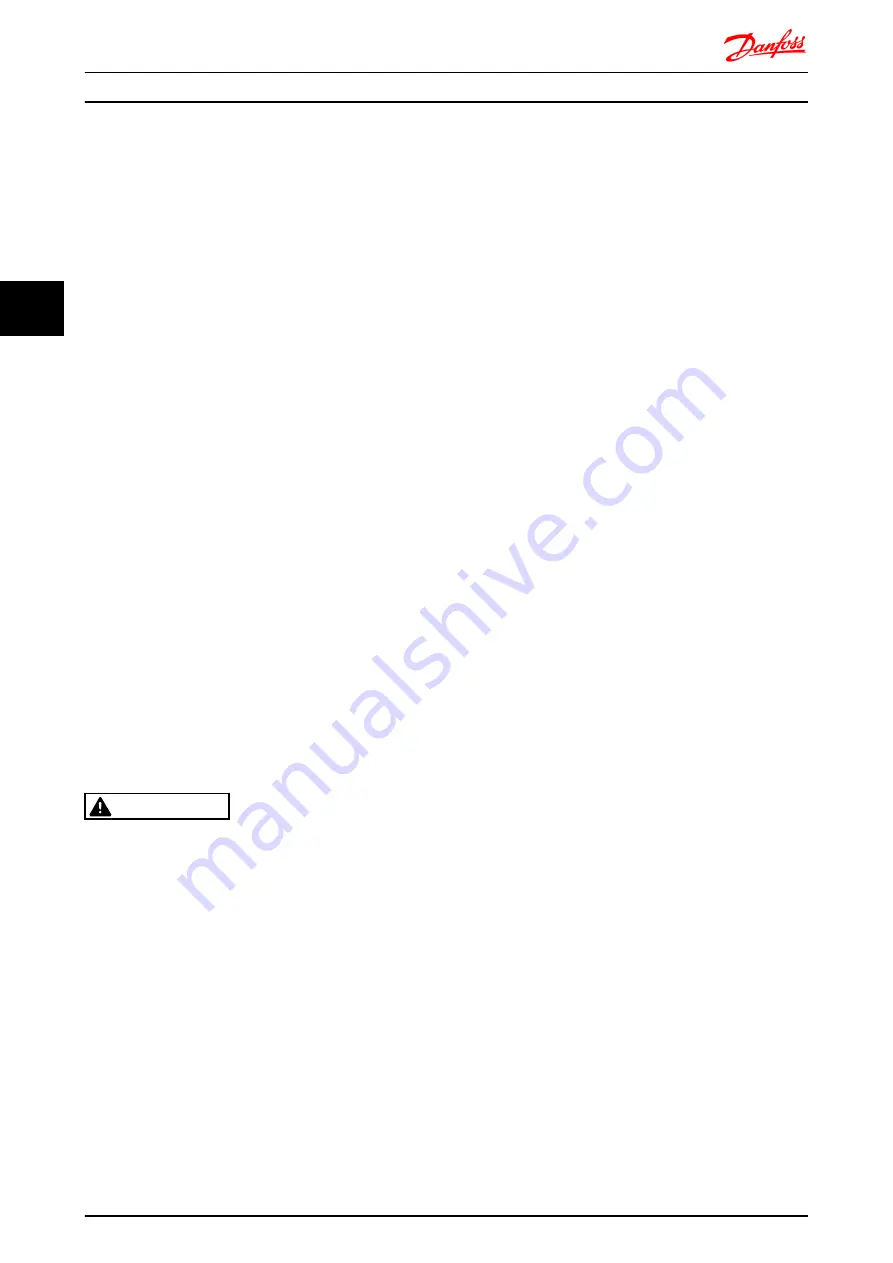
The frequency converter is guaranteed not to restart
creation of a rotational field by an internal fault (in
accordance with Cat. 3 of EN 954-1, PL d acc. EN ISO
13849-1 and SIL 2 acc. EN 62061). After activation of Safe
Stop, the display will show the text ”Safe Stop activated”.
The associated help text says, "Safe Stop has been
activated. This means that the Safe Stop has been
activated, or that normal operation has not been resumed
yet after Safe Stop activation”.
NOTE
The requirements of Cat. 3 (EN 954-1)/PL “d” (ISO 13849-1)
are only fulfilled while 24 V DC supply to terminal 37 is
kept removed or low by a safety device which itself fulfills
Cat. 3 (EN 954-1) PL “d” (ISO 13849-1). If external forces act
on the motor, it must not operate without additional
measures for fall protection. External forces can arise for
example, in the event of vertical axis (suspended loads)
where an unwanted movement, for example caused by
gravity, could cause a hazard. Fall protection measures can
be additional mechanical brakes.
By default the Safe Stop function is set to an Unintended
Restart Prevention behaviour. Therefore, to resume
operation after activation of Safe Stop,
1.
reapply 24 V DC voltage to terminal 37 (text Safe
Stop activated is still displayed)
2.
create a reset signal (via bus, Digital I/O, or
[Reset] key.
The Safe Stop function can be set to an Automatic Restart
behaviour. Set the value of
5-19 Terminal 37 Safe Stop
from
default value [1] to value [3].
Automatic Restart means that Safe Stop is terminated, and
normal operation is resumed, as soon as the 24 V DC are
applied to Terminal 37. No Reset signal is required.
WARNING
Automatic Restart Behaviour is permitted in one of the two
situations:
1.
The Unintended Restart Prevention is
implemented by other parts of the Safe Stop
installation.
2.
A presence in the dangerous zone can be
physically excluded when Safe Stop is not
activated. In particular,
paragraph 5.3.2.5 of ISO
12100-2 2003
must be observed
4.9.1.2 Safe Stop Commissioning Test
After installation and before first operation, perform a
commissioning test of an installation or application, using
Safe Stop.
Perform the test again after each modification of the
installation or application involving the Safe Stop.
NOTE
A passed commissioning test is mandatory after first instal-
lation and after each change to the safety installation.
The commissioning test (select one of cases 1 or 2 as
applicable):
Case 1: Restart prevention for Safe Stop is required (that
is, Safe Stop only where
5-19 Terminal 37 Safe Stop
is set
to default value [1], or combined Safe Stop and MCB112
where
5-19 Terminal 37 Safe Stop
is set to [6] or [9]):
1.1 Remove the 24 V DC voltage supply to
terminal 37 using the interrupt device while the
frequency converter drives the motor (that is,
mains supply is not interrupted). The test step is
passed when
•
the motor reacts with a coast, and
•
the mechanical brake is activated (if
connected)
•
the alarm “Safe Stop [A68]” is displayed
in the LCP, if mounted
1.2 Send Reset signal (via Bus, Digital I/O, or
[Reset] key). The test step is passed if the motor
remains in the Safe Stop state, and the
mechanical brake (if connected) remains
activated.
1.3 Reapply 24 V DC to terminal 37. The test step
is passed if the motor remains in the coasted
state, and the mechanical brake (if connected)
remains activated.
1.4 Send Reset signal (via Bus, Digital I/O, or
[Reset] key). The test step is passed when the
motor becomes operational again.
The commissioning test is passed if all four test steps 1.1,
1.2, 1.3 and 1.4 are passed.
Case 2: Automatic Restart of Safe Stop is wanted and
allowed (that is, Safe Stop only where
5-19 Terminal 37
Safe Stop
is set to [3], or combined Safe Stop and MCB112
where
5-19 Terminal 37 Safe Stop
is set to [7] or [8]):
2.1 Remove the 24 V DC voltage supply to
terminal 37 by the interrupt device while the
frequency converter drives the motor (that is,
mains supply is not interrupted). The test step is
passed when
•
the motor reacts with a coast, and
•
the mechanical brake is activated (if
connected)
•
the alarm “Safe Stop [A68]” is displayed
in the LCP, if mounted
2.2 Reapply 24 V DC to terminal 37.
The test step is passed if the motor becomes operational
again. The commissioning test is passed if both test steps
2.1 and 2.2 are passed.
Application Examples
VLT
®
Decentral Drive FCD 302
72
MG04H102 - VLT
®
is a registered Danfoss trademark
4
4