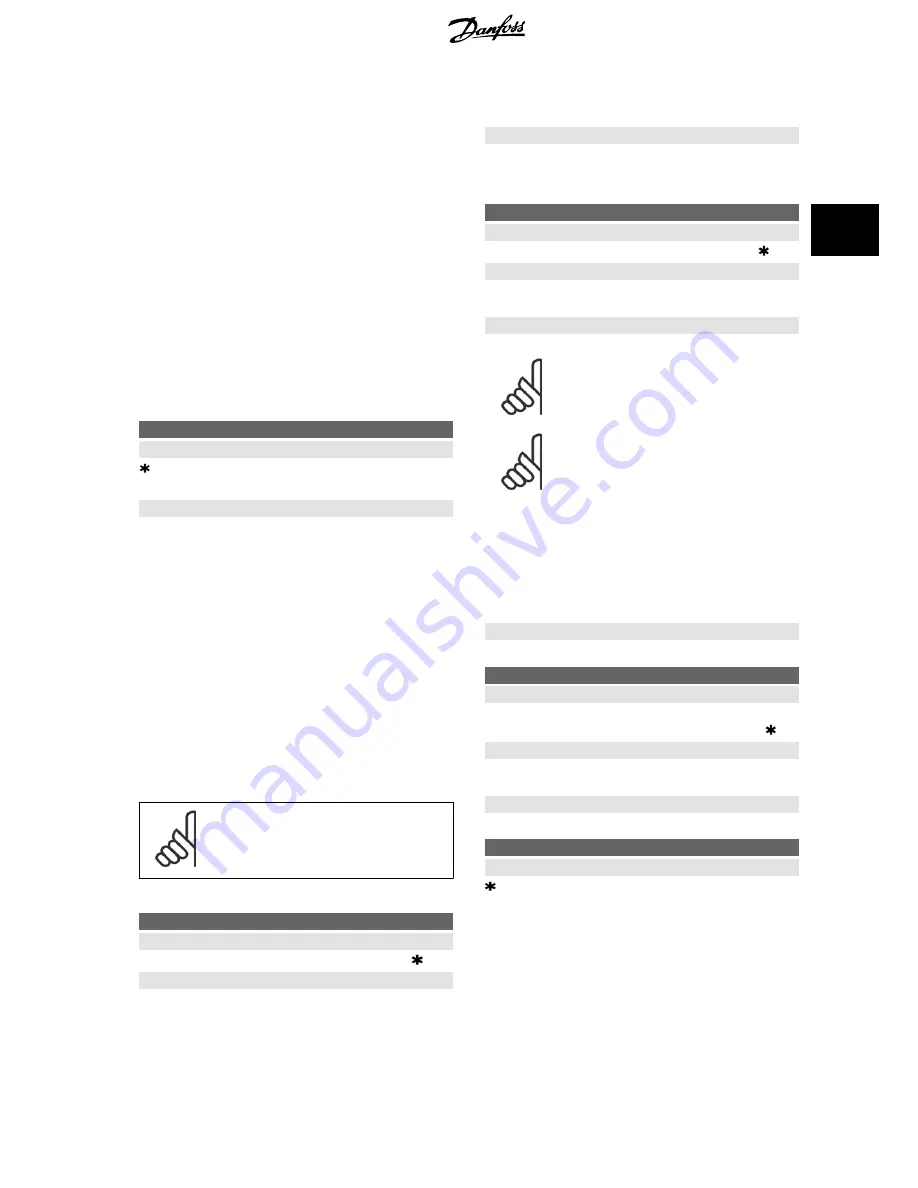
cy
and the output voltage will correspond to the setting in parameter 131
Voltage at start
.
This functionality is typically used in hoist applications. It is used in par-
ticular in applications in which a cone anchor motor is applied, where the
direction of rotation is to start clockwise followed by the reference direc-
tion.
Select
Start frequency/voltage in reference direction
[4] to obtain the
function described in parameter 130
Start frequency
and 131
Voltage at
start
during the start delay time.
The direction of rotation of the motor will always follow in the reference
direction. If the reference signal equals zero, the output frequency will
equal 0 Hz, while the output voltage will correspond to the setting in
parameter 131
Voltage at start
. If the reference signal is different from
zero, the output frequency will equal parameter 130
Start frequency
and
the output voltage will equal parameter 131
Voltage at start
. This func-
tionality is used typically for hoist applications with counterweight. It is
used in particular for applications in which a cone anchor motor is applied.
The cone anchor motor can break away using parameter 130
Start fre-
quency
and parameter 131
Voltage at start
.
122
Function at stop
Value:
Coasting (COAST)
[0]
DC hold (DC HOLD)
[1]
Function:
This is where to choose the function of the frequency converter after the
output frequency has become lower than the value in parameter 123
The
min. frequency for activation of function at stop
or after a stop command
and when the output frequency has been ramped down to 0 Hz.
Description of choice:
Select
Coasting
[0] if the frequency converter is to 'let go' of the motor
(inverter turned off).
Select DC hold [1] if parameter 137
DC hold voltage
is to be activated.
123
Min. frequency for activation of function at stop
Value:
0,1 - 10 Hz
0,1 Hz
Function:
In this parameter, the output frequency is set at which the function se-
lected in parameter 122
Function at stop
is to be activated.
Description of choice:
Set the required output frequency.
NB!
If parameter 123 is set higher than parameter 130,
then the start delay function (parameter 120 and 121)
will be skipped.
NB!
If parameter 123 is set too high, and DC hold has been
chosen in parameter 122, the output frequency will
jump to the value in parameter 123 without ramping
up. This may cause an overcurrent warning / alarm.
3.3.2 DC Braking
During DC braking DC voltage is supplied to the motor, and this will cause
the shaft to be brought to a standstill. In parameter 132
DC brake volt-
age
DC brake voltage can be preset from 0-100%. Max. DC brake voltage
depends on the motor data selected.
In parameter 126
DC braking time
DC braking time is determined and in
parameter 127
DC brake cut-in frequency
the frequency at which DC
braking becomes active is selected. If a digital input is programmed to
DC braking inverse
[5] and shifts from logic '1' to logic '0', DC braking will
be activated. When a stop command becomes active, DC braking is ac-
tivated when the output frequency is less than the brake cut-in frequency.
NB!
DC braking may not be used if the inertia in the motor
shaft is more than 20 times greater than the motor's
internal inertia.
126
DC brake time
Value:
0 - 60 sec.
10 sec
Function:
In this parameter, the DC brake time is set at which parameter 132
DC
brake voltage
is to be active.
Description of choice:
Set the required time.
127
DC brake cut-in frequency
Value:
0.0 (OFF) - par. 202
Output frequency high limit, f
MAX
OFF
Function:
In this parameter, the DC brake cut-in frequency is set at which the DC
brake is to be activated in connection with a stop command.
Description of choice:
Set the required frequency.
128
Thermal motor protection
Value:
No protection (NO PROTECTION)
[0]
Thermistor warning
(THERMISTOR WARN)
[1]
Thermistor trip (THERMISTOR TRIP)
[2]
ETR warning 1 (ETR WARNING 1)
[3]
ETR trip 1 (ETR TRIP 1)
[4]
ETR warning 2 (ETR WARNING 2)
[5]
ETR trip 2 (ETR TRIP 2)
[6]
ETR warning 3 (ETR WARNING 3)
[7]
ETR trip 3 (ETR TRIP 3)
[8]
VLT® Decentral FCD
3 Programming
MG.04.B8.02 - VLT is a registered Danfoss trademark
45
3
Summary of Contents for VLT Decentral FCD 300
Page 112: ......