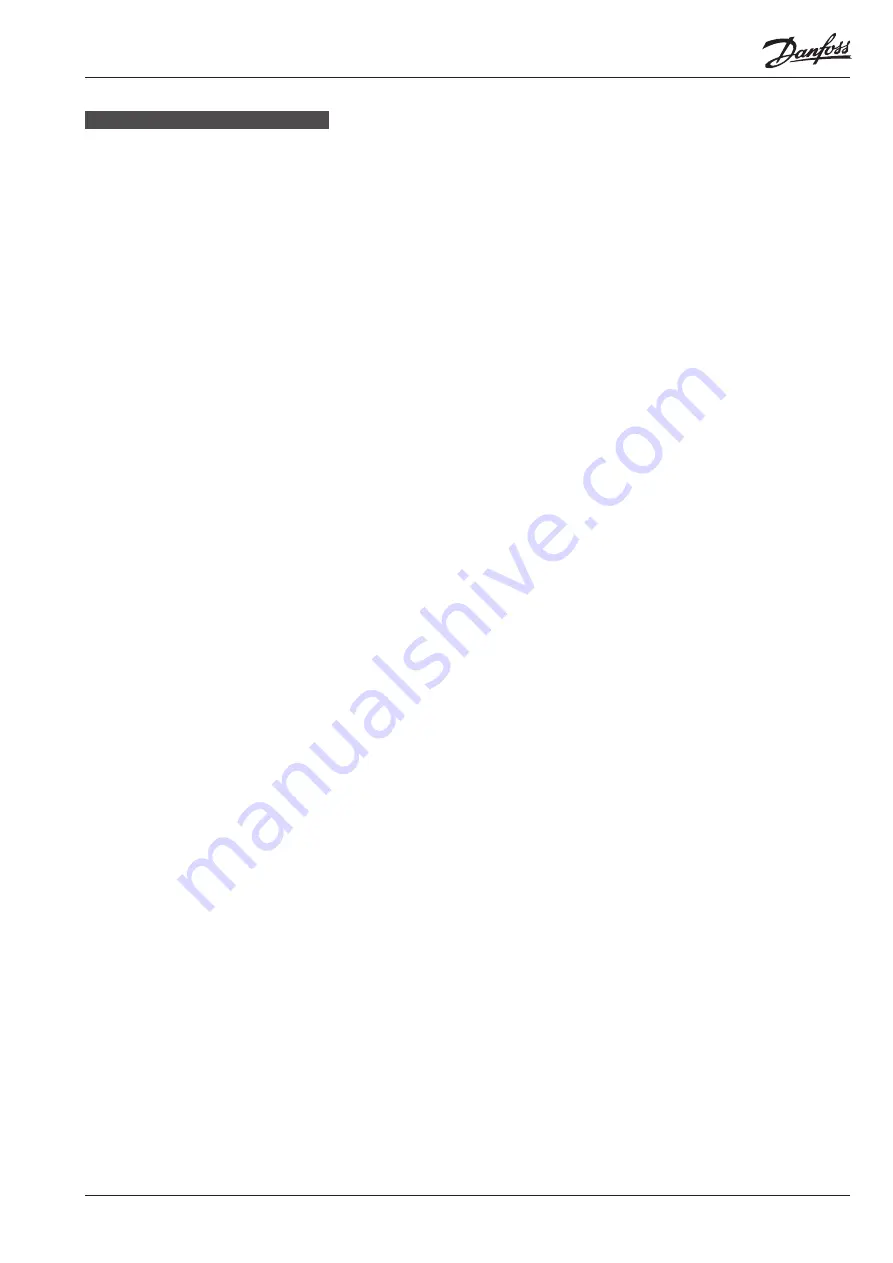
© Danfoss A/S (AC-MCI/MWA), 2013-10
DKRCI.PI.KD1.D2.ML / 520H6448 3
ENGLISH
Installation
Refrigerants
Applicable to all common non-flammable
refrigerants and all non-corrosive gases/
liquids.
Can be used in chemical and petro-
chemical applications.
The valve is only recommended for use
in closed circuits. For further information
please contact Danfoss.
Temperature range
–10°C to +150°C (14°F to +302°F)
Pressure range
The valves are designed for a max. working
pressure of 65 bar g (942 psig).
Installation
The valve must be installed with the
spindle vertically upwards or in horizontal
position (fig. 1). Valves should be opened
by hand (fig. 3) according to the guidelines
in the datasheet. The valve is designed to
withstand a high internal pressure. How-
ever, the piping system should be designed
to avoid liquid traps and reduce the risk of
hydraulic pressure caused by thermal ex-
pansion. It must be ensured that the valve
is protected from pressure transients like
“liquid hammer” in the system.
Recommended flow direction
Direct the flow towards the cone as indi-
cated by the arrow placed on the valve
housing (fig. 2). The force used to open and
close the valve must not exceed the force
of an ordinary handwheel.
Welding
The bonnet should be removed before
welding (fig. 4) to prevent damage to the
O-rings in the packing gland and between
the valve body and bonnet, as well as the
teflon gasket in the valve seat. Only ma-
terials and welding methods, compatible
with the valve housing material, must be
welded to the valve housing. The valve
should be cleaned internally to remove
welding debris on completion of welding
and before the valve is reassembled.
Avoid welding debris and dirt in the
threads of the housing and the bonnet.
Removing the bonnet can be omitted pro-
vided that:
The temperature in the area between the
valve body and bonnet during welding
does not 150°C/+302°F. This tem-
perature depends on the welding method
as well as on any cooling of the valve body
during the welding itself. (Cooling can be
ensured by, for example, wrapping a wet
cloth around the valve body.)
Make sure that no dirt, welding debris etc.
get into the valve during the welding
procedure.
Be careful not to damage the teflon cone
ring.
The valve housing must be free from
stresses (external loads) after installation.
SVA-S valves must not be mounted in
systems where the outlet side of the valve
is open to atmosphere. The outlet side of
the valve must always be connected to the
system or properly capped off, for example
with a welded-on end plate.
Assembly
Remove welding debris and any dirt from
pipes and valve body before assembly.
Check that the cone has been fully screwed
back towards the bonnet before it is
replaced in the valve body (fig. 5).
Tightening
Tighten the bonnet with a torque wrench,
to the values indicated in the table (fig. 5).
Colours and identification
The SVA valves are painted with a red
primer in the factory. Precise identification
of the valve is made via the red coloured ID
ring at the top of the bonnet, as well as by
the stamping on the valve body. The exter-
nal surface of the valve housing must be
prevented against corrosion with a
suitable protective coating after installa-
tion and assembly.
Protection of the ID ring when repainting
the valve is recommended.
Maintenance
Packing gland
When performing service and main-
tenance, replace the complete packing
gland only, which is available as a spare
part. As a general rule, the packing gland
must not be removed if there is internal
pressure in the valve. However, if the
following pre-cautionary measures are
taken, the packing gland can be removed
with the valve still under pressure:
Backseating (fig. 6)
To backseat the valve, turn the spindle
counter-clockwise until the valve is fully
open.
Pressure equalization (fig. 7)
In some cases, pressure forms behind the
packing gland. Hence a handwheel or
similar should be fastened on top of the
spindle while the pressure is equalized. The
pressure can be equalized by slowly
screwing out the gland.
Removal of packing gland (fig. 8)
Cap and packing gland can now be
removed.
Dismantling the valve
Do not remove the bonnet while the valve
is still under pressure.
- Check that the alu-ring (fig. 12, pos. A)
has not been visibly deformed.
- Check that the spindle is free of
scratches and impact marks.
- If the teflon cone ring has been
damaged, the whole cone assembly
must be replaced.
Replacement of the cone (fig. 13)
Unscrew the cone screw (pos. D) with an
Allen key.
SVA-S 6-10
2.0 mm A/F
(An Allen key is included in the Danfoss
Industrial Refrigeration gasket set).
Remove the balls (pos. E).
Number of balls in fig. 13, pos. E:
SVA-S 6-10 .....................................................6 pcs.
The cone can then be removed. Place the
new cone on the spindle and replace the
balls. Refit the cone screw in again using
Loctite No. 648. to ensure that the screw is
properly fastened.
Assembly
Remove any dirt from the body before the
valve is assembled. Check that the cone
has been screwed back towards the bon-
net before it is replaced in the valve body
(fig. 5).
Tightening
Tighten the bonnet with a torque wrench,
to the values indicated in the table (fig. 5).
Tighten the packing gland with a torque
wrench, to the values indicated in the table
(fig. 11).
Use only original Danfoss parts, including
packing glands, O-rings and gaskets for
replacement. Materials of new parts are
certified for the relevant refrigerant.
In cases of doubt, please contact Danfoss.
Danfoss accepts no responsibility for
errors and omissions. Danfoss Industrial
Refrigeration reserves the right to make
changes to products and specifications
without prior notice.