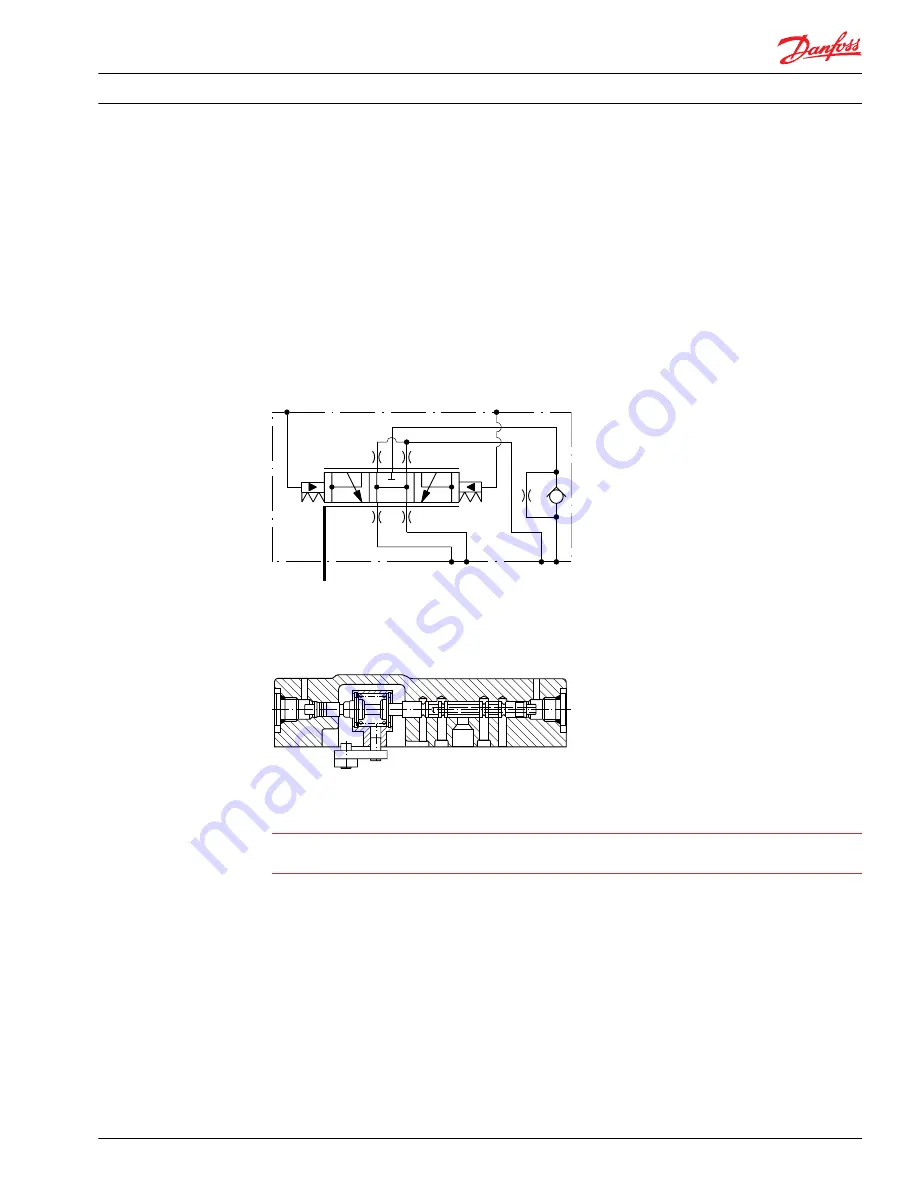
•
Internal mechanical stops on the servo valve allow rapid changes in input signal pressure without
damaging the control mechanism.
•
Precision parts provide repeatable, accurate displacement settings with a given input signal.
•
The swashplate is coupled to a feedback mechanism. The control valve drains the ends of the servo
piston when an input signal is not present.
Benefits:
•
Simple - low cost design.
•
Pump returns to neutral after prime mover shuts down.
•
Pump returns to neutral if there is a loss of input signal pressure or if there is a loss of charge pressure.
Hydraulic displacement control schematic
M5 M4
T P
Feedback
from
swashplate
X2
X1
P102029
Cross-section
T M4 P M5 T
P102 030
X1
X2
W
Warning
Maximum allowable signal pressure is 60 bar [870 psi]. Exceeding allowable signal pressure will cause
damage to the control.
Response time
The time required for the pump output flow to change from zero to full flow (acceleration) or full flow to
zero (deceleration) is a function of the size of the orifice in the control flow passage, charge pressure,
valve plates and other vehicle dynamics.
A range of orifice sizes are available for the Series 90 hydraulic displacement control to assist in matching
the rate of swashplate response to the acceleration and deceleration requirements of the application.
Testing should be carried out to determine the proper orifice selection for the desired response.
For more information regarding response time for individual orifices, please contact your Danfoss
representative.
Technical Information
Series 90 Axial Piston Pumps
Control Options
520L0603 • Rev 0804 • March 2016
33